IAC Moves Up Value Stream to Control Costs
IAC’s earth-elements initiative entails a process known as plastics compounding, where the engineering characteristics of less-expensive polymer resins are enhanced by adding mineral fillers and other special additives.
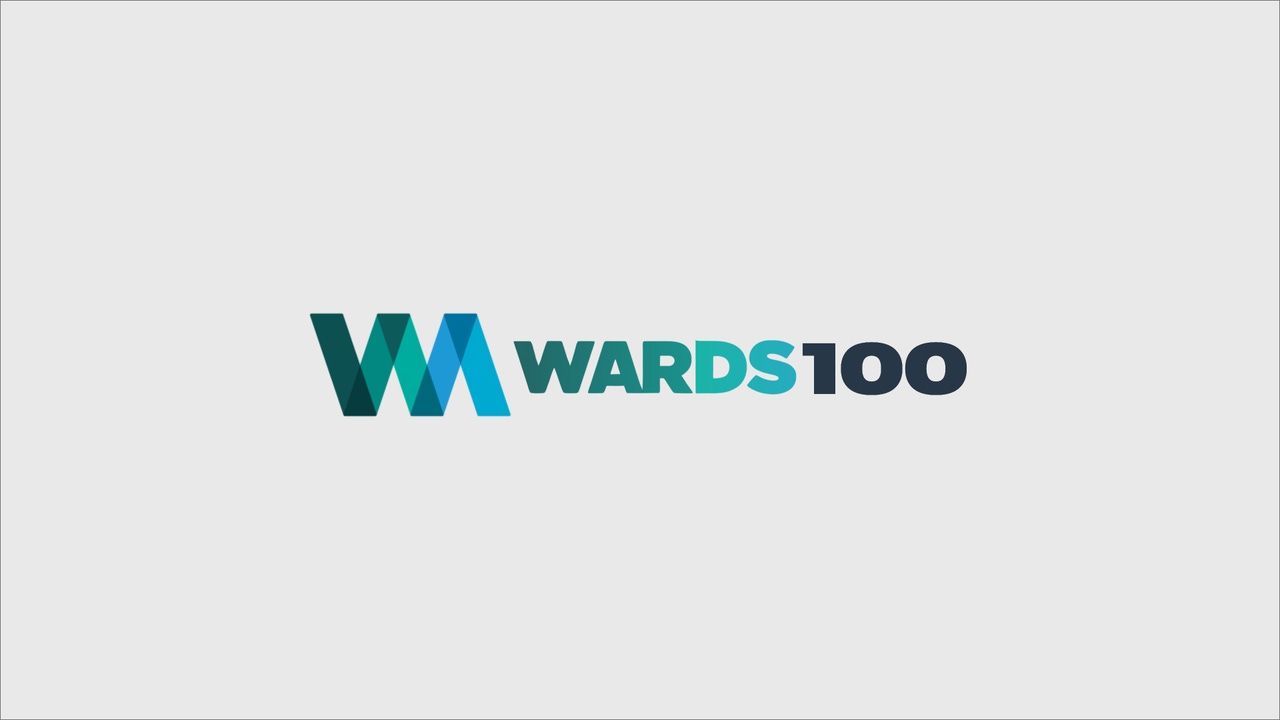
Special Coverage
Management Briefing Seminars

TRAVERSE CITY, MI – Custom engineering the plastics it uses to mold parts for automotive interiors may not have been considered a core business of International Automotive Components, but as polymer prices continue to soar, it is becoming one.
Established in 2005 and including former business units of Lear Corp., Collins & Aikman Inc. and other international interior suppliers, CEO Jim Kamsickas describes IAC as a petrochemical-based interiors products business.
With that description comes the reality the supplier is highly sensitive to oil prices.
That’s led to what Kamsickas calls an “earth-elements initiative.”
This entails a process known as plastics compounding, where the engineering characteristics of less-expensive polymer resins are enhanced by adding mineral fillers such as talc and other special additives.
The result is better-performing, less-expensive plastic parts.
“We’re working toward earth elements on almost all products we manufacture,” Kamsickas tells Ward’s.
“It may have not been core before, but times have changed and if we need to make (plastics compounding) core, we will,” he says.
IAC CEO Jim Kamsickas
Even though IAC, like all suppliers, is struggling with excess capacity caused by falling customer production volumes, Kamsickas says the supplier’s order book is strong and heading in the right direction.
In just one year, IAC’s business has moved from a 50/50 mix of cars vs. trucks to a 60/40 mix. “Call it lucky or call it good, but we’ve dramatically moved from trucks and SUVs over to cars,” Kamsickas says.
IAC’s ability to deliver whole interiors (except for seats) also is an advantage, because it enables the supplier to participate in weight-reduction initiatives.
“You can’t do it in pods,” says Kamsickas. “Our customers come to us today and say, ‘Take the whole package, go to your test lab and come out with the solution.’”
IAC is able to do this because most interior-related weight problems can be traced to acoustic issues.
“The weight usually comes from throwing different Band-Aids at the vehicle interior to either block the sound or absorb the sound,” Kamsickas says.
About the Author
You May Also Like