Look Ma, No Cam!Look Ma, No Cam!
Electrohydraulic valve operation that eliminates camshafts and associated hardware is widely seen as the next big watershed in engine development. Lotus Engineering, a division of Lotus Cars Ltd. in Norfolk, U.K., now could be considered the industry leader in this field. The company says it has a system ready for production, a Tier One supplier to make it and a major OEM to buy it. Lotus is not ready,
March 1, 2003
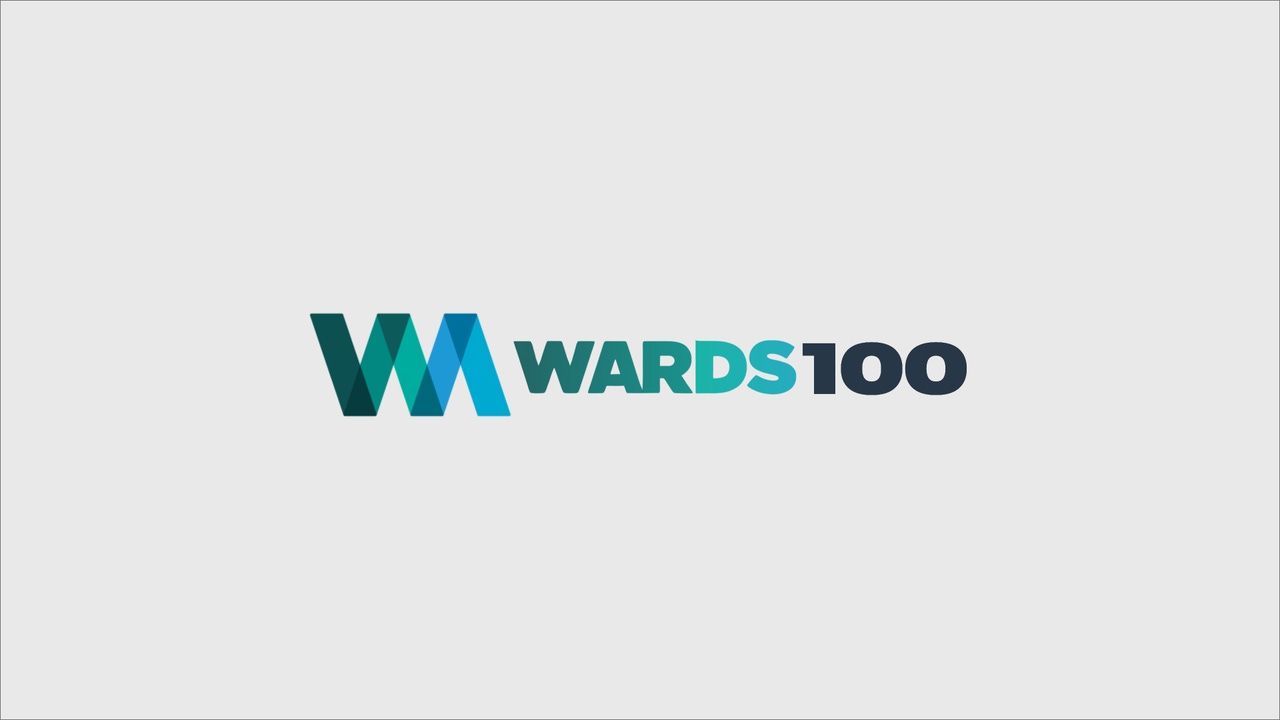
Electrohydraulic valve operation that eliminates camshafts and associated hardware is widely seen as the next big watershed in engine development.
Lotus Engineering, a division of Lotus Cars Ltd. in Norfolk, U.K., now could be considered the industry leader in this field. The company says it has a system ready for production, a Tier One supplier to make it and a major OEM to buy it. Lotus is not ready, however, to identify those partners.
Camless valve activation offers several advantages and possibilities:
Infinitely variable valve lift and duration — as well as timing — throughout the engine speed and load range, creating optimum combustion efficiency.
Use of inlet valves to throttle the engine, eliminating the usual butterfly valve and associated pumping losses. This is the electrohydraulic equivalent of the BMW AG-developed Valvetronic electro-mechanical system.
Alter 4-valve engines to 3- or 2-valve operation, as appropriate.
Deactivate selected cylinders for fuel economy benefits. General Motors Corp. is ready to bring to production a less sophisticated system, dubbed Displacement on Demand, that delivers the same effect.
Reduce parasitic losses on the engine by eliminating the power-robbing camshaft and its drive components.
Facilitate Controlled Auto Ignition (CAI), a closely linked Lotus project using hot exhaust gas instead of a spark plug to ignite the fuel/air mixture.
As a production unit, Lotus' Active Valve Train (AVT) actuator has a hydraulic cylinder above with the stem to open the poppet valve, which then is closed by a conventional return spring.
A linear displacement transducer alongside the stem continuously monitors valve movement, as its instantaneous position is a critical input to the controlling computer. This is combined with a precision electro-hydraulic valve in the lift cylinder feed line that regulates the action and pressure.
The engine's ECU is programmed with 256 different valve lift profiles that replicate camshaft lobe shapes. Such movements are handled by the valve-controlling fluid delivery to each actuator.
But while such camshaft profiles are fixed, the Lotus system offers an array of waveforms that can be varied in both shape and timing, thus regulating the inlet and exhaust valve opening and closing rates.
It is even possible to retard a valve's final closing velocity to give a “soft landing” against the seat, when hydraulic pressure cushions touch-down for quieter operation.
As a production item, the actuator assembly is reported to be marginally shorter than the usual OHC arrangement, so there is no packaging problem. A dedicated engine-driven oil pump supplies the system.
Meanwhile, many auto and engine companies are investigating CAI, but its combination with the Lotus AVT could give the company a competitive edge. Shifting valve operation is the key factor.
In a typical spark-ignition gas engine, the inlet valve might open 20 degrees before top dead center to start the induction stroke, and close 20 degrees after bottom dead center (BDC). With CAI, the exhaust valve is closed much earlier in the four-stroke cycle, while opening of the inlet valve is substantially delayed.
About the Author
You May Also Like