Module Supplier Says Future Bright, Despite In-Sourcing Trend
While auto makers focus their core competencies on engines and powertrains, the CEO of HBPO sees brisk demand for suppliers specializing in front-end modules.
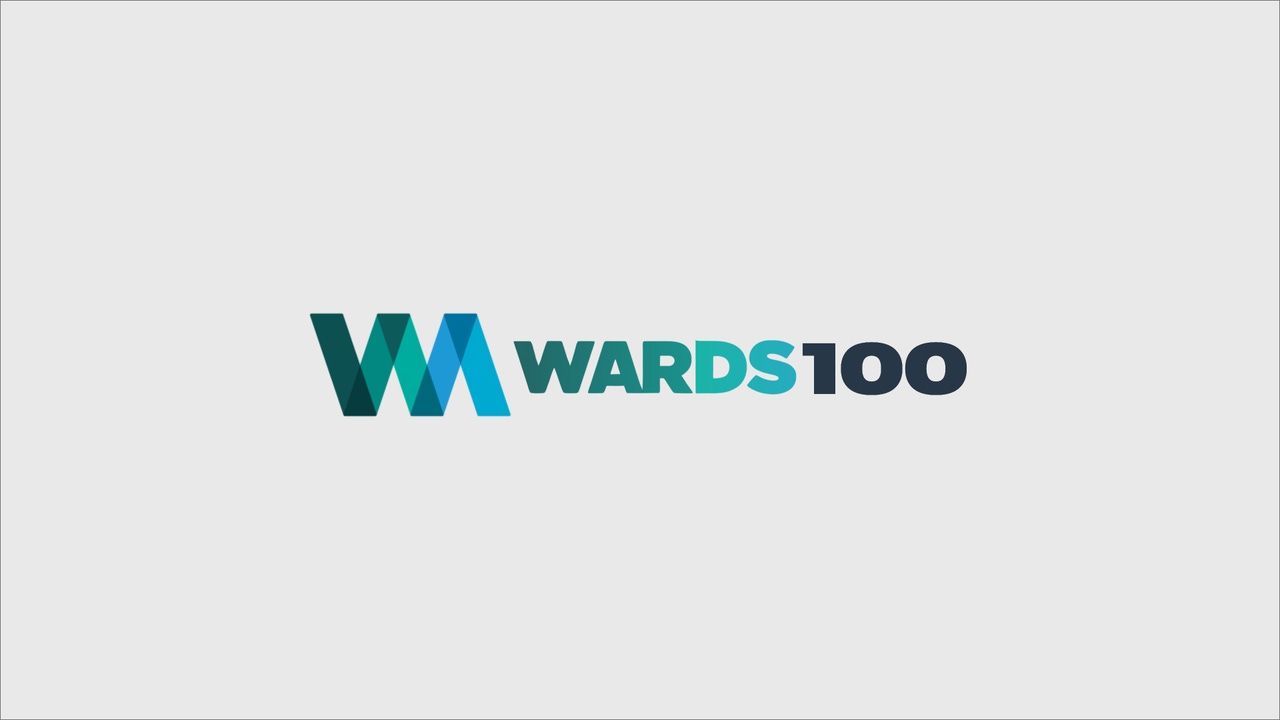
PARIS – Worldwide restructuring of the auto industry has led to more vertical integration at some auto makers, but the leading supplier of front-end assemblies argues the trend toward manufacturing with modules will continue.
In August, Ford Motor Co. said by 2012 it will have brought back enough work from suppliers to add nearly 2,000 jobs at its unionized U.S. plants, and several other auto makers are expected to follow the same path.
Manufacturing with modules is not synonymous with outsourcing. Cockpits, for example, often are manufactured by auto makers, themselves, on separate subassembly lines.
But the effort to reduce costs has led many OEMs to outsource modules, such as cockpits and front ends, to suppliers, whose workers earn lower wages.
HBPO GmbH is an invention of the era of modules. German lighting expert Hella KGaA Hueck & Co. first made a joint venture in 1999 with German cooling specialist Behr GmbH to provide front-end modules to European auto makers.
In 2004, French plastic bumper expert Plastic Omnium SA joined what now is a company with three equal owners.
The module business is “a logical consequence of the world situation in which car models become more and more diversified and overall volumes of each model become smaller, while complexity gets higher, with more engines (and) new powertrains,” HBPO CEO Martin Schueler says in an interview.
“Model diversification fits totally with modules, ” he adds. “(Auto makers) want to produce a car. They don’t want the expense of space in the plant. Throughput is one of the key indicators, and it can only be really good if you have cockpits, you have doors, you have front-end modules.”
HBPO front-end module incorporates head lamps, bumper, fascia, engine cooling and other components.
Auto makers will focus more on their core competencies, including engines and powertrains, while continuing to rely on suppliers in other areas, Schueler predicts.
“We see it happening,” he says. “In the next two years, we are opening three new plants in Europe.”
In addition, new modules are possible, with Plastic Omnium developing rear-hatch modules, and auto makers, themselves, designing battery modules for electric cars.
Modules ought to be a logical consequence of vehicle development, Schueler says. “But there might be good reasons for not doing it, coming from the outside that we don’t control.”
Those factors include the new lower pay scales at some OEM plants in North America, and promises from companies such as Volkswagen AG and Renault SA to their government minority owners to maintain employment.
“On the trend to in-sourcing, there are certain tendencies,” he says, “and of course we are observing this and discussing it with the customers. The tendencies are there, and we look at how we are prepared for this. We are in discussions.”
Schueler believes his module supplier can outlast the in-house trend because “we are totally focused on front-end modules. That is the big difference. It is our only product line, and we believe that we are the experts. It doesn’t mean that the OEMs don’t know how to do it, but they have a different system.”
Auto makers “might develop the best tooling and the best bumper fascia,” he says. But when it comes time for a module, “they might find, ‘Oh, we forgot a clip here and an angle there and some screws.’”
That adds a lot of cost in the end, Schueler says. “We do the integration of the system, and I think that makes the difference.”
HBPO works with its parent companies, but it does not limit itself to them as lower-tier suppliers.
“You can only survive in our business if you have the freedom of sourcing,” says Schueler. “If we were to be limited to using a mother company’s part, that would be a tremendous roadblock in HBPO development.”
The backbone of a front end is the carrier that holds the bumper, radiator, headlamps and other elements together.
“Due to specifications of the car maker, safety regulations, everything, we need to be open to different kinds of technologies,” he says, meaning the supplier has to be ready to meet specifications calling for multiple types of plastic, plastic-metal hybrids and pure-metal designs.
“We are open to all these kinds of technologies, and we don’t find all of them in our mother companies.”
The approach of battery-electric vehicles will have only a small impact on front-end designs, Schueler says.
“A car will have cooling anyway; you will need a condenser,” he points out. “You will have a battery and an electric motor, and there is the question of how that is cooled. You will need a lot of specific know-how in air flow. We are already doing this.”
HBPO has 15 assembly plants worldwide and regional technical centers in North America, Europe and Asia.
“In China, India and the (Association of Southeast Asian Nations free-trade) area, as well, they are looking for some partners to help them with safety regulations and fuel-consumption regulations and appearance problems,” Schueler says. “We expect growth in those areas.”
About the Author
You May Also Like