New Engine Device Cuts Costs 50%
A new fuel-system device reportedly boosting gasoline-engine efficiency and reducing emissions while shaving costs 50% will be introduced at the SAE Congress & Exposition March 6-10 at Detroit's Cobo Hall.Jointly patented by Robert Bosch GmbH and a newcomer to the U.S. auto industry, Hydra LLC, the component relates to how fuel is fed to the engine.Not wishing to scoop himself, Hydra LLC General Manager
March 1, 2000
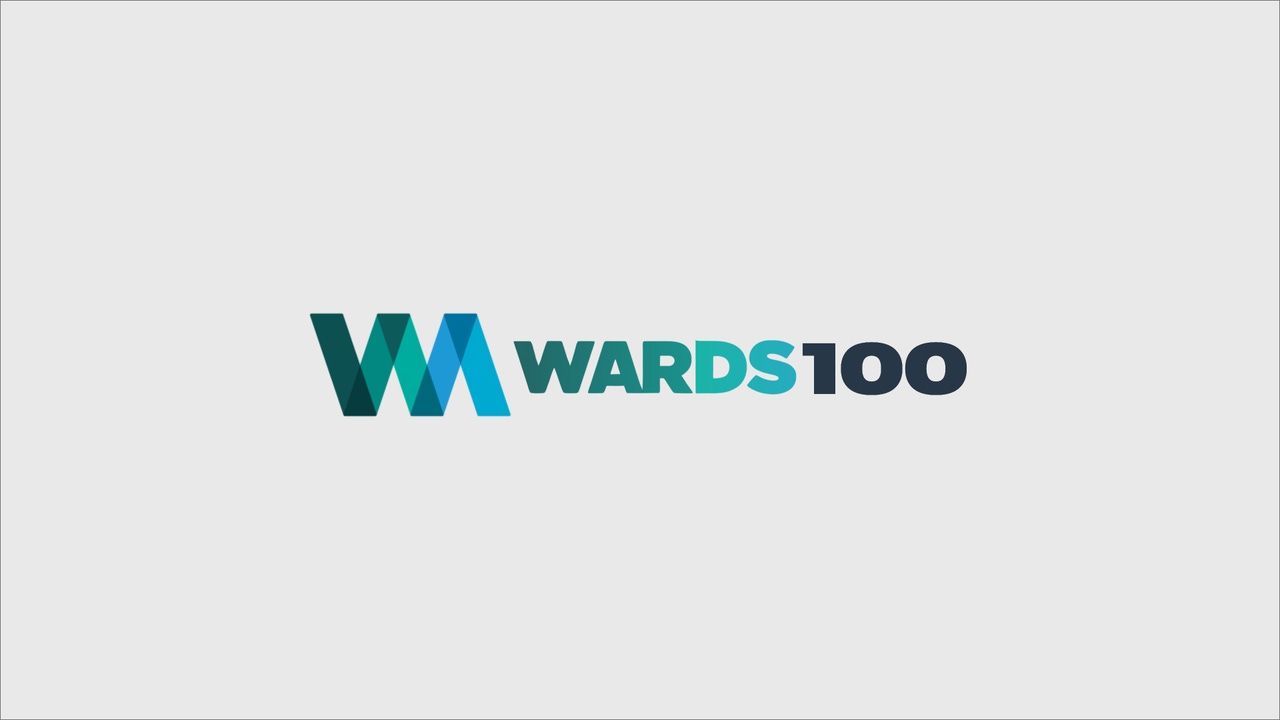
A new fuel-system device reportedly boosting gasoline-engine efficiency and reducing emissions while shaving costs 50% will be introduced at the SAE Congress & Exposition March 6-10 at Detroit's Cobo Hall.
Jointly patented by Robert Bosch GmbH and a newcomer to the U.S. auto industry, Hydra LLC, the component relates to how fuel is fed to the engine.
Not wishing to scoop himself, Hydra LLC General Manager Kurt S. Kushner says only that primary targets are light- and heavy-duty truck engines.
Hydra LCC, a unit of Germany's Witzenmann GmbH, will manufacture the component at its Salem, NH, plant as a Tier 2 supplier to Bosch, says Mr. Kushner. General Motors Corp. Ford Motor C.and DaimlerChrysler Corp. all have shown interest in the development, he adds.
Although little known in North America, Witzenmann is major player in automotive flexible metal products in Europe, boasting a 60% to 65% market share, says Mr. Kushner. Its products include exhaust-system decoupling systems and EGR piping, steering-shaft bellows for front-end collision protection and fuel-cooler systems. Its European customers include practically every automaker.
Nearly half of the Witzenmann Group's $270 million in annual sales ($140 million) are derived from automotive customers. Founded in 1854 by Heinrich Witzenmann, the company remains privately held by the Witzenmann family.
Right now its Hydra U.S. unit is tiny by comparison. Established about five years ago, Hydra LLC's sales totaled $6.5 million in 1999, says Mr. Kushner. His goal: Tripling revenues within three to five years.
The Salem plant was built in 1997 primarily to manufacture exhaust decoupling devices. It has capacity to make 600,000 units yearly, again as a Tier 2 supplier. Much of the plant's output currently is shipped to Europe.
Hydra LLC established headquarters last August in Troy, MI, naming Mr. Kushner to head overall U.S. operations, including the Salem plant.
Hydra's engine/exhaust devices use a variety of metals and manufacturing techniques, such as hydroforming and laser welding, depending on the application. Metal bellows to withstand high pressures and temperature extremes while retaining flexibility are incorporated in many Hydra designs.
The EGR piping, for example, is located between the block and head, where temperatures can range from, say, -2degreesF to +200degreesF (-19degreesC to +149degreesC). "As the system heats up and expands, the bellows absorb the expansion" without deforming, he explains.
Hydra's decoupling devices, located between the manifold and exhaust pipe, are designed to eliminate movement and engine vibrations, an important consideration in an industry obsessed with reducing NVH (noise/vibration/harshness) problems. Some systems are load-bearing, others aren't.
One Hydra design is a complete piece made entirely of stainless steel, with couplings, brackets, bellows and knitted steel covering, eliminating further assembly. Showing a visitor a sample, Mr. Kushner says it can be produced cost-competitively "or cheaper." And because all of the elements are stainless steel, "it will last the life of the vehicle," he says.
Mr. Kushner has no illusions about becoming a big-timer in the North American market anytime soon, however, which can have a positive spin. "We only have 60 people (50 in Salem, 10 in Troy)," he allows. "But because we're small, we're hungry. The drawback of most small companies is they don't have the resources, but we do: a full R&D capability in Germany."
Read more about:
2000About the Author
You May Also Like