New-Generation Diesels Give Cast Iron a Boost
Cast iron once was the most fundamental building block of the automotive industry. It was a major reason why automotive entrepreneurs gravitated to Detroit at the turn of the 20th century. Before it was a production center for engine blocks and other auto parts, Detroit was famous for making cast-iron stoves. Now, 100 years later, few materials have fallen from grace in the automotive world like cast
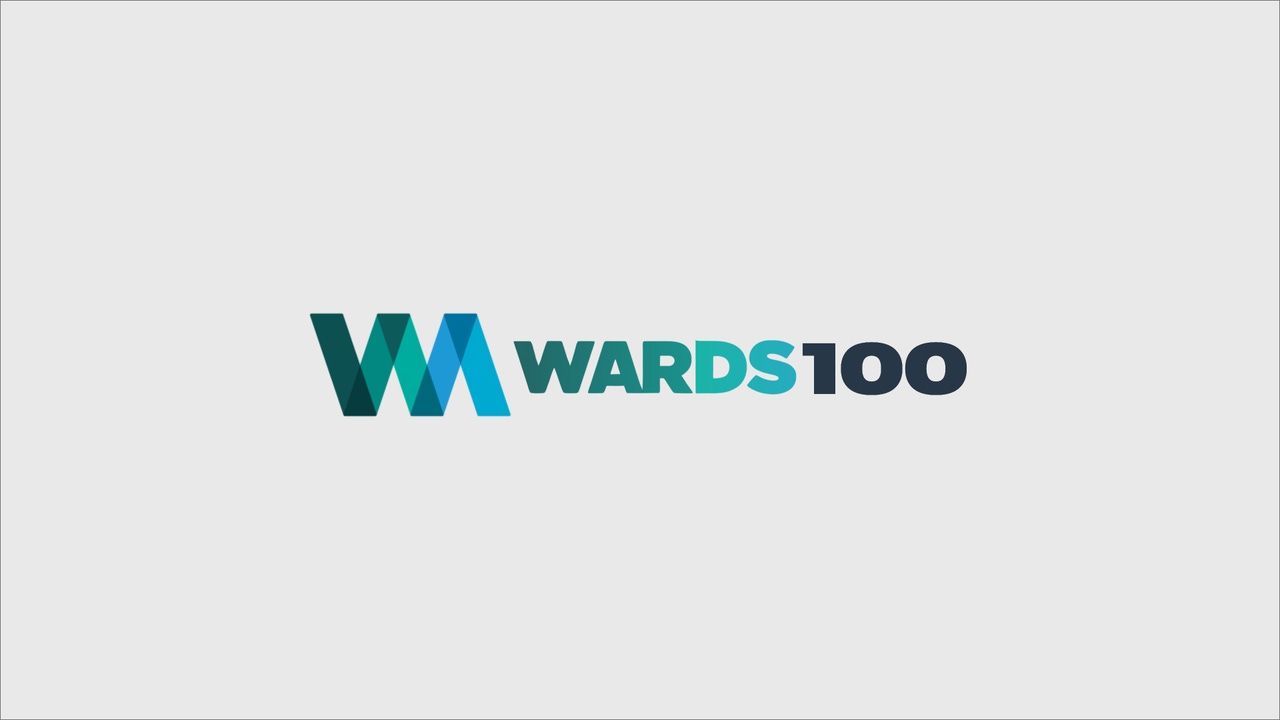
Cast iron once was the most fundamental building block of the automotive industry. It was a major reason why automotive entrepreneurs gravitated to Detroit at the turn of the 20th century. Before it was a production center for engine blocks and other auto parts, Detroit was famous for making cast-iron stoves.
Now, 100 years later, few materials have fallen from grace in the automotive world like cast iron. Starting with the engine block, where 100 lbs. (45 kg) can be saved by switching to aluminum, iron has become the No.1 target of automotive engineers seeking to chop weight by substituting lighter materials.
In the past 10 years, the amount of iron used in a typical North American family vehicle has plummeted 86 lbs. (39 kg), from 431 lbs. (196 kg) in 1991 to 345 lbs. (156 kg) in 2001. The farther back you look, the more dramatic cast iron's slide becomes: in 1977, the typical American car had 540 lbs. (245 kg) of cast iron, according to American Metal Market.
And many experts think iron use hasn't bottomed out. There still remain many older engine families that are expected to be switched over to aluminum when they are redesigned, and now engineers are switching many key suspension parts from iron to aluminum — even on relatively low-priced, high-volume cars and trucks.
There is, however, a small ray of hope on the horizon for cast iron: high-tech diesel engines. Because of their special requirements, these new engines may become a niche that — at least for a while — aluminum won't be able to invade.
For example, after suffering in Europe for falling behind in diesel engine development, Ford Motor Co. appears to be trying to make up for lost time by designing a cutting edge 2.7L V-6 diesel using a new type of high-density cast iron for the engine block that's barely been used in high production before.
Proponents say the move could have far-reaching impact on the world's iron, foundry and automotive industries, although there are numerous skeptics.
Production of the new powerplant — which will be the top engine in the combined Ford-PSA (Peugeot-Citroen Group) global diesel engine strategy — is scheduled to start in 2003 and rise to more than 100,000 units annually beginning in 2004. Applications will include Jaguar, PSA, Land Rover and Ford vehicles.
Sources say the new compacted graphite iron (CGI) cylinder block is exceptionally strong and light and will enable the engine to produce the high cylinder pressures necessary to meet Euro IV (2005) and Euro V (2008) emissions regulations, a job the original aluminum design reportedly couldn't do.
Here's how regular iron differs from CGI: Ordinary grey iron contains carbon or graphite in flake form, which creates tiny planes within metal castings that can fracture when the metal is under stress, reducing overall strength. CGI contains graphite in a vermicular (worm-like) form, which translates into stronger cross sections. That provides the ability to make castings with thinner, stronger walls.
Officials in Ford's powertrain operations aren't talking, but its plans to use CGI for its new diesel engine blocks were revealed in early July in a joint press release by Tupy Fundicoes SA of Brazil, a major iron foundry and SinterCast AB, a Swedish foundry technology company, announcing Tupy had won the contract from Ford.
The contract is a huge victory for SinterCast, which has been struggling to interest automakers in high-volume CGI production since the company was formed in 1988. SinterCast Inc., a wholly owned business unit of SinterCast AB, was headed up for a few years in the 1990s by Theodore N. Louckes, a distinguished 40-year General Motors Corp. veteran who is best known as the architect of the automaker's now-discontinued Quad-4 engine.
CGI offered lots of promise in the 1990s — as engine blocks and heads seemed to be shifting inexorably from cast iron to aluminum — because it was 1.5 to 2 times as strong as conventional grey iron but still much cheaper than aluminum. But after an initial splash, CGI's progress stalled because it was more difficult to mass-produce and machine than anticipated.
Doug Brown, the current president of Clarkston, MI-based SinterCast Inc., says machining issues and other problems now have been resolved, and the enormous demand for advanced diesel engines in Europe have pushed CGI into the spotlight again. But now, instead of just being an improved cast iron, CGI may distinguish itself as the preferred material for next-generation passenger car diesels.
That's because passenger car diesels now are following the trend in heavy-duty trucks to much higher cylinder pressures. Passenger car cylinder pressures of 2,600 psi (180 bar) and higher are being planned by major automakers to meet EURO IV emission regulations and the even more stringent requirements of EURO V coming in '07 and '08. Heavy-duty diesels already operate in excess of 2,900 psi (200 bar).
Increasing cylinder pressure by as much as 580 psi (40 bar) or more for passenger cars to just meet 2005 emissions requires an enormous jump in technology because it creates much higher mechanical and thermal stresses. Ford “just gave up” on aluminum, says one source.
Audi AG already uses CGI for the crankcase on its low-volume 3.3 V8 TDI Diesel, which produces 67 hp/L and a staggering 354 lb.-ft (480 Nm) of torque. BMW also uses CGI for its 3L inline 6-cyl. turbodiesel.
Those engines are produced in comparatively low volumes, however. This important high-volume commitment from Ford verifies that the entire CGI manufacturing process, including machining, satisfies mass production requirements and economics, says Bertil Hagman, president & CEO of SinterCast AB.
About the Author
You May Also Like