OEMs Ponder Dual-Fuel, Cooled EGR Combustion Strategies
A Southwest Research scientist says many automakers have begun working on dual-fuel RCCI systems, and that it will take at least a decade before the technology is ready for production vehicles.
April 22, 2015
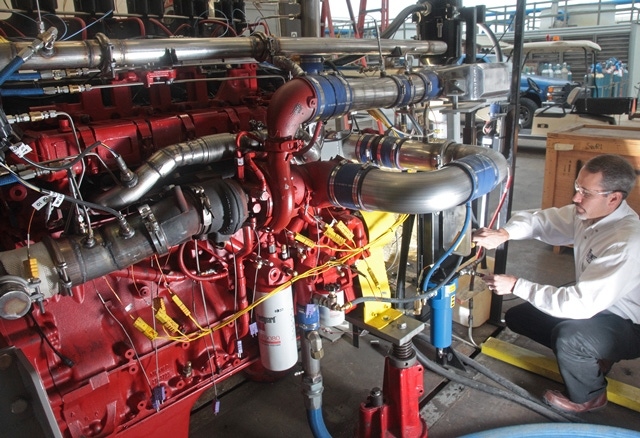
DETROIT – The auto industry and independent researchers are moving ahead at an unprecedented rate with breakthrough ideas, such as combining gasoline and diesel in the same combustion cycle, to address pending greenhouse-gas and criteria-pollutant regulations.
The focus needs to be on better understanding the composition of exhaust gases, says Cary Henry, principal engineer for aftertreatment R&D at Southwest Research Institute, during a presentation at an SAE powertrain symposium held here in tandem with the 2015 SAE World Congress.
Henry says novel combustion approaches are being considered for serial production in the near future and will alter the nature of criteria pollutants, which include oxides of nitrogen, formaldehyde and non-methane organic gases, emitted from internal-combustion engines.
For more than two decades, the industry researched homogeneous-charge compression ignition, which allows a gasoline engine to behave like a more fuel-efficient diesel and reduce NOx and particulate emissions, but that concept has been shelved because controlling the combustion event proved problematic, he says.
Instead, today’s research centers on gasoline direct compression ignition, championed by Delphi, and reactivity controlled compression ignition, which port-injects gasoline and directly injects diesel into the same combustion chamber.
Henry says many automakers are just getting started in their research of the dual-fuel RCCI system, and that it will take at least a decade before the technology is ready for production vehicles.
GDCI may have a bit of a head start in terms of development, so it might beat RCCI to market, within a decade.
“GDCI is a diesel engine using gasoline as the fuel,” Henry says, adding that it has fewer challenges than RCCI.
“Diesel engines use diesel because it’s a very reactive fuel. You direct-inject it, and it burns very well,” he says. “The challenge with gasoline direct-injection is that at light load, it’s hard to get that gas to burn, because gasoline is made purposely to resist combustion. That’s why we have high octane ratings on gasoline. You want to resist knocking.”
RCCI first surfaced in the 1980s, but only recently has the research been kick-started once again. The technology is compatible with forced induction and, like HCCI, can reduce NOx and particulate emissions while cutting fuel consumption.
But dual-fuel RCCI allows greater control of the engine, which results in noise reduction and lower peak cylinder pressures, Henry says. On the downside, RCCI requires on-board storage and delivery of both gasoline and diesel fuels.
Cooled EGR to 'Go Mainstream'
These advanced strategies are necessary because the California Air Resources Board, as part of its LEV III legislation, requires light-duty vehicles to reduce NOx and hydrocarbon emissions 80% between 2015 and 2025.
Henry says the law impacts diesel light vehicles more severely than gasoline. Heavy-duty vehicles must cut NOx emissions 90% by 2031.
Scientists at SwRI have built prototype dual-fuel heavy-duty lean-burn engines, running up to 90% on gasoline.
Compared with a typical HD diesel engine from 2010, the prototype achieves a 95% reduction in NOx and cuts smoke 90%.
But along with the benefits come a few negatives, such as 10 times more carbon monoxide and five times more hydrocarbons. Plus, exhaust temperatures drop 122º F (50º C), which makes it harder for catalysts to scrub emissions.
Most modern diesel engines already employ pre-mixed charge compression ignition, which allows for multiple injections of fuel into the combustion chamber, creating better swirl and helping mitigate noise.
“PCCI already has mainstream acceptance,” Henry says.
He refers to cooled exhaust-gas recirculation, a technology that appears now on the Toyota Prius hybrid. By routing a small amount of exhaust gas back to the intake, conventional EGR lowers in-cylinder temperatures and reduces oxides of nitrogen emissions up to 80%.
Cooled EGR, which drops combustion temperatures even further and became common in heavy-duty diesel applications more than a decade ago, has been proven to decrease particulate emissions. It also can result in reduced fuel enrichment, another important benefit.
Henry points to cooled EGR as a way to lower fuel consumption through reduced pumping losses and heat transfer losses, as well as improved knock tolerance.
For a few hundred dollars per vehicle, cooled EGR can boost fuel efficiency up to 10%, Henry says. “We will see cooled EGR go mainstream,” he says.
Demonstrating the growth in these emissions-focused solutions, supplier BorgWarner earlier this month opened a plant in Chungju, South Korea, to manufacture EGR valves and coolers, among other emissions products.
Low-temperature combustion, another technology for reducing NOx emissions and the formation of soot, also is considered as a way to cut carbon-monoxide emissions up to 30%, Henry says.
Industry observers suggest LTC may lead to broader use of cleaner diesel engines, but the technology also can result in higher carbon-monoxide and hydrocarbon emissions.
New approaches to combustion are essential because certain recent powertrain trends are creating new challenges.
For instance, the widespread use of gasoline direct injection, while boosting horsepower, torque and fuel economy, is resulting in substantial increases in both the size and number of particulates being emitted from tailpipes.
In addition, GDI engines have been known to leave carbon deposits on the back side of valves, which can lead to warranty claims. Conventional port-injection systems avoid this problem, because fuel injected upstream burns off and prevents those deposits from forming.
For this reason, Henry says low-cost PFI systems will remain popular well into the future.
You May Also Like