Quality Swat Team
A defective part threatens to shut down the line at a Canadian assembly plant. Speed is imperative in today's just-in-time automotive world - but the supplier is based in the U.S., Mexico, maybe even Japan.Increasingly, the call for help is being answered by companies such as Engineered Solutions Corp. (ESC) of Cambridge, Ont., with a float of quality engineers available 24 hours a day, seven days
August 1, 2000
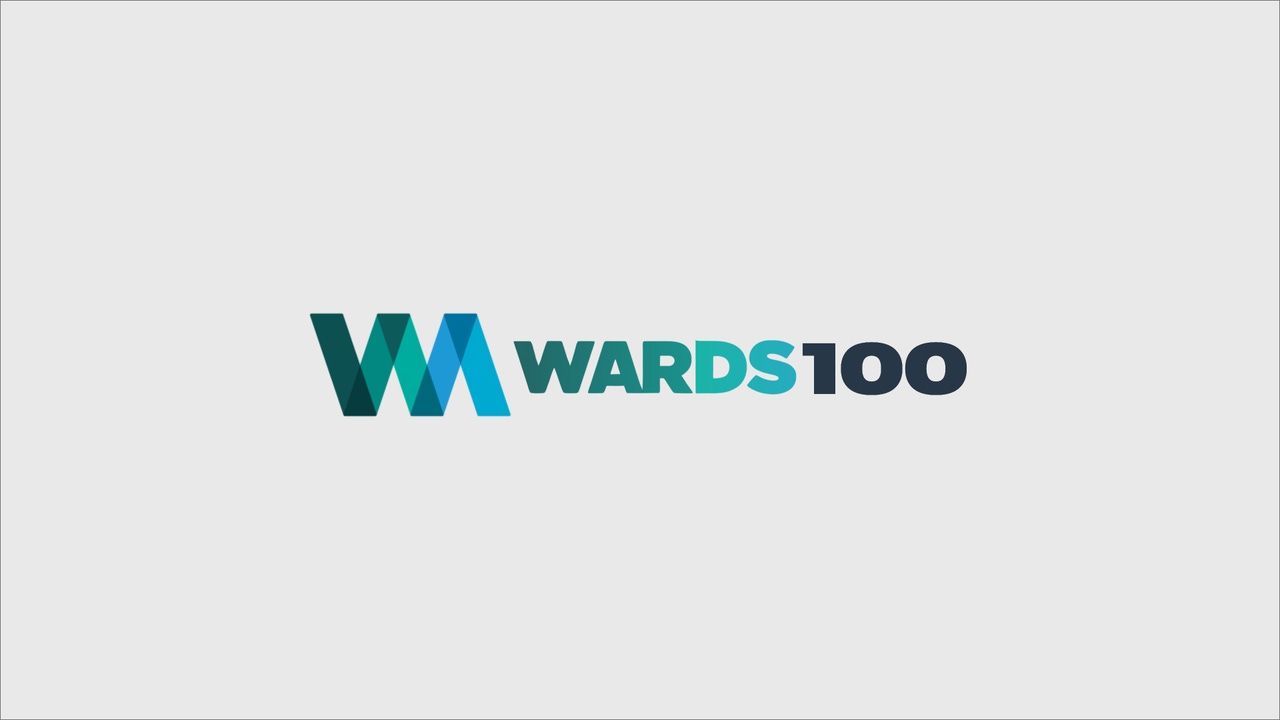
A defective part threatens to shut down the line at a Canadian assembly plant. Speed is imperative in today's just-in-time automotive world - but the supplier is based in the U.S., Mexico, maybe even Japan.
Increasingly, the call for help is being answered by companies such as Engineered Solutions Corp. (ESC) of Cambridge, Ont., with a float of quality engineers available 24 hours a day, seven days a week.
ESC set up shop in February 1998, offering its services as a quality swat team of sorts. Co-founder and president Ron McKelvey could see that a global industry that puts a premium on both quality and speed could use on-call troubleshooters to fix problems, fill gaps.
"We get called in when an assembly plant's about to be shut down," says Mr. McKelvey, who employs 40 to 175 at a given time. The numbers swell when a customer is in the midst of a launch.
When a defective part threatens production, ESC offers itself as the solution next-door. It can send a containment team to a plant in the Canadian automotive heartland (greater Toronto and Windsor areas) within two hours.
The team uses digital camera equipment to document the problem and email it back to the supplier for immediate assessment. The supplier can devise a course of action and authorize ESC to fix it on-site.
"Everyone wins," says Mr. McKelvey.
That has been the experience at FAG Bearings Ltd. of Stratford, Ont., which first brought ESC in four months ago when they realized they had received some bad product, says quality support leader Debbie Vanstone. ESC came in to sort, measure and rework the parts that were not to spec.
In a situation like that, "we don't have people available to pull from their regular work," says Ms. Vanstone. And flying in people from out of town generates time and cost, whereas ESC employees can be dispatched immediately and go home at night.
"They definitely fill a void," says Ms. Vanstone.
"Using a company like us takes the onus and responsibility off their own people," says Kevin Roberts, ESC's quality engineering manager. "It's a relief to know there's someone competent to call."
"When you have a problem, you need someone now," agrees Robert Laughlin, supplier quality engineer for Roctel Mfg., a high-volume machining division of Linamar Corp. that handles as many as 10,000 parts a day. "They had people here within an hour or two."
ESC started with a single, major supplier experiencing quality problems with a component. ESC handled the inspection and sorting, and filed a report documenting it all.
The client base has grown, largely by word of mouth, says Mr. Roberts. Today the company has sales in the $4.5 million range and does business with more than 200 companies including most major carmakers and many suppliers.
There are ESC representatives stationed at about eight off-site offices, including two Ford of Canada assembly plants in Oakville, Ont.
American companies often lack resources to work with Canadian plants. "We can represent a U.S. supplier at an Ontario plant. We save time and money for them," says Mr. Roberts. "We are an extension of their business for some clients."
"We have a service agreement with the supplier so the OEM never sees anything but clean product," says Mr. McKelvey.
ESC has two Cambridge, Ont., facilities with 40,000 sq. ft. (3,700 sq. m) of space. The quality watchdogs perform services on or off-site and offer warehousing space as well as just-in-time sequencing and shipping, light assembly work and repair.
But 60% of their calls are emergencies that require fast reaction time and the ability to understand and perform the task, says Mr. Roberts.
Mr. Laughlin of Roctel says he appreciates that the workers remain attentive to detail through the repetitive work of high volumes.
In addition to solving the immediate problem, ESC works with clients on a long-term fix. This does not eliminate work for ESC, says Mr. Roberts, but gives them credibility so they are called upon when a customer experiences a new problem.
There are similar companies in North America, but ESC is the largest in Canada within its particular service niche, says Mr. McKelvey.
About the Author
You May Also Like