Ringing Endorsement
As a high-volume SUV program was preparing to launch a few years ago for a Big Three auto maker, wind noise and water leaks suggested a serious problem with a closure panel. Eager for a solution, the auto maker first had to identify the source of the problem, which baffled its body engineers. Perceptron Inc., a supplier that specializes in laser-based measuring, got the call to analyze five doors,
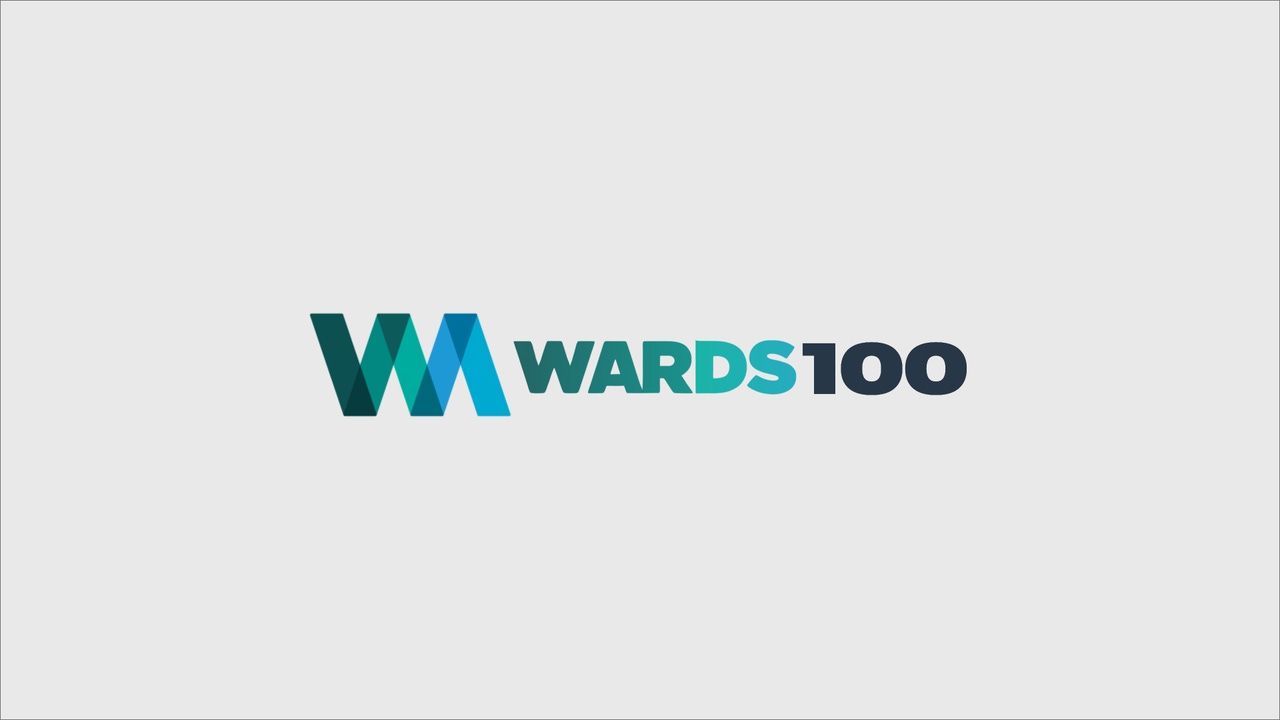
As a high-volume SUV program was preparing to launch a few years ago for a Big Three auto maker, wind noise and water leaks suggested a serious problem with a closure panel.
Eager for a solution, the auto maker first had to identify the source of the problem, which baffled its body engineers.
Perceptron Inc., a supplier that specializes in laser-based measuring, got the call to analyze five doors, all of them allegedly identical. Perceptron engineers eventually learned the five doors were anything but. They found significant variation in the dimensions of all five.
The proposed solution has given rise to a tidy new business unit with a promising future for the Plymouth, MI, supplier.
For decades, the auto industry has relied on “ring gauges” to check the dimensions of closure panels. First, the panel is fabricated. The ring gauge, a large, steel tool, is then custom made, like a frame around a picture.
The tool is parked alongside the vehicle assembly line and used by quality-control staffers to manually check a series of measurements, usually at a rate of one in 10 or one per shift after rampup. Every hood, door and decklid on every car gets its own ring gauge, at a cost of $100,000 per tool.
Here's the kicker: A ring gauge is not reusable. Once it has fulfilled its job and a vehicle program ends, the tool is scrapped and a new one built for the next closure panel. Even a minor vehicle facelift can require extensive ring-gauge modification.
The recent Big Three SUV program demonstrated a shortcoming with the current technology. “Either the ring gauge was bad, or the measurement was faulty,” says John Kidd, Perceptron market manager.
Specifically, some of the doors were poorly aligned, bending too far inside the body in some cases and bowing too far outside in others, Kidd says.
The problem with traditional ring gauges — besides devouring plant space and being inflexible — is they rely completely on the skill of the person using them, Kidd says. Variation due to human error happens on occasion, as demonstrated by the SUV program.
Perceptron's solution is its Flexible Ring Gauge, which employs a computer-aided-design model of the closure panel to be measured. Instead of placing the panel inside a hand-made checking fixture, Perceptron's scanning device uses the CAD model to project a “virtual gauge” over the panel to replicate the body opening that mates with the panel.
An operator no longer takes a series of measurements manually. Instead, a digital non-contact scanner mounted to a robot takes 1 million measurements, checking gaps and body flushness, within four minutes. Placing the door in a conventional tool and gathering measurements takes about 15 minutes.
“The operator shouldn't need too much skill to do it,” Kidd says. “He would load the part and press a button. (The software) would present a report on gap and flush for the door.”
Plus, the Flexible Ring Gauge can be reprogrammed with new software, allowing it to be reused for a new vehicle program.
The potential savings in tooling costs are significant. For a new-vehicle program, an OEM can expect to spend about $720,000 for six conventional ring gauges for a 2-door and 4-door body style. One Flexible Ring Gauge, which can measure all six doors, will cost about $500,000, Kidd says.
Over the course of three vehicle generations, the conventional ring gauges would cost more than $2.1 million ($720,000 times three generations). Over that same time, the only additional cost for the Flexible Ring Gauge for each generation is about $60,000 for new software, bringing the total investment to $620,000.
But getting industry buy-in has been difficult because the ring gauge has a long manufacturing legacy.
A U.S. OEM is testing the new tool in a supplier factory and plans to begin using the system for door measurements in a vehicle-assembly plant by early 2005, Kidd says.
Although in its infancy, the market for the Flexible Ring Gauge could take off.
Bill Corriveau, Perceptron senior vice president, says it will take about three years before the new equipment begins taking away share from established technology, namely coordinate-measurement machines and conventional ring gauges.
About the Author
You May Also Like