SAE Panel: Cutting Weight Doesn’t Always Mean Adding Cost
DETROIT – Here’s good news for an auto industry continually pressured to improve fuel economy and curb emissions: Cutting weight – the most effective way to hike fuel economy and chop emissions – doesn’t always have to cost money. Jaguar says weight-cutting techniques improved fuel economy, performance for new XJ flagship. That’s the refreshing message from panelists at the “Innovative Applications
March 12, 2004
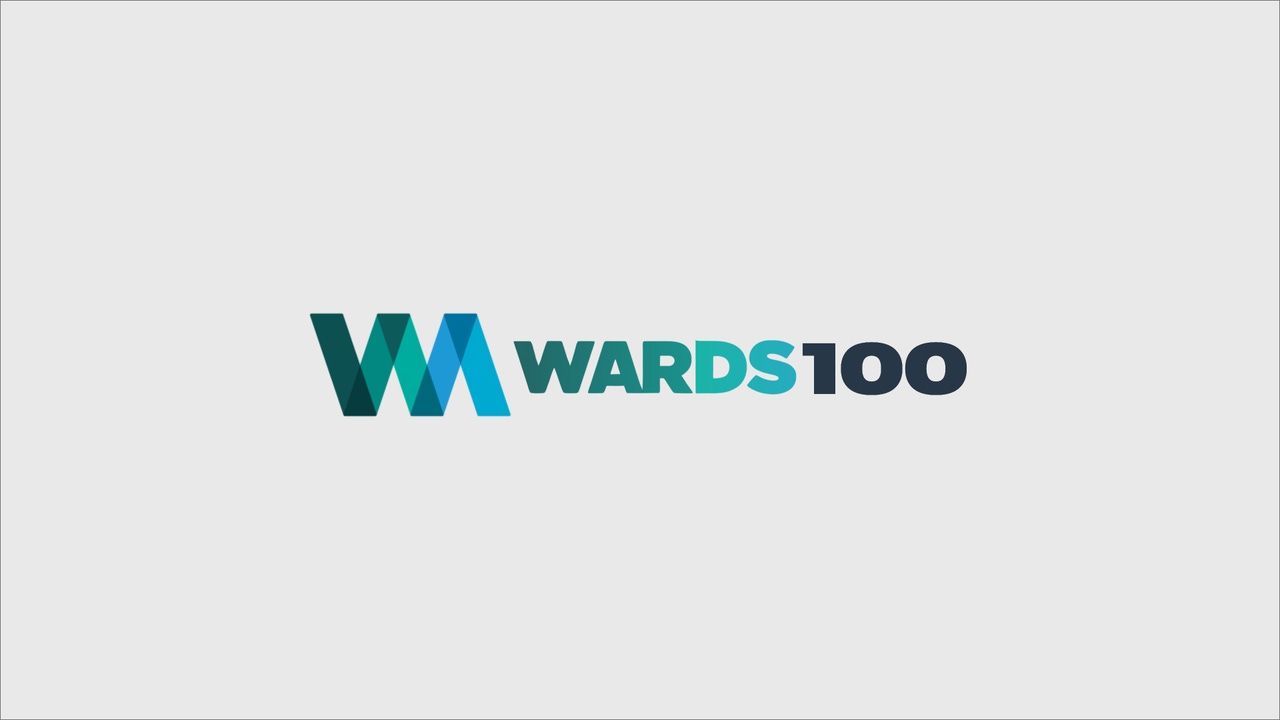
DETROIT – Here’s good news for an auto industry continually pressured to improve fuel economy and curb emissions: Cutting weight – the most effective way to hike fuel economy and chop emissions – doesn’t always have to cost money.
Jaguar says weight-cutting techniques improved fuel economy, performance for new XJ flagship. |
That’s the refreshing message from panelists at the “Innovative Applications of Materials – Selecting the Right Combination of Materials and Manufacturing Processes to Save Time, Weight and Money” technical session at the Society of Automotive Engineers World Congress here.
Conventional wisdom says using lightweight materials almost invariably is more costly than employing the cheap iron and steel the auto industry has favored since its inception. But panelists here say the industry is instituting novel new practices and processes to make weight-efficient measures cost-efficient as well.
Jeffrey Helms, Ford Motor Co. manager-materials research and advanced engineering, reveals Ford is working on a prototype light-truck platform, dubbed Impact Project, that weighs 12% less, yet is projected to be less expensive to manufacture.
Helms also says Ford is developing a dual-phase-steel truck frame that costs less than a current-production counterpart but weighs 10% less.
Michael D. Bernas, manager-materials development group, Toyota Technical Center USA Inc., echoes Helm’s points, noting Toyota now is employing a unique materials-evaluation model that allows the company to “design for materials rather than selecting a material for a design.”
The Toyota process has three main elements, Bernas says:
Outsourced resin optimization, a database that suggests the best plastic material for a given part, based on weight, cost and performance. This formula allowed the company to cut $0.75 from the cost of a Corolla door panel, for example.
Localization of materials, a strategy of increasingly sourcing materials from the areas or regions where a vehicle is built. Using this process for the U.S.-built Camry, Toyota coordinated with a U.S. supplier for the headliner, which previously was imported from Japan. The result was a similar headliner at a savings of $8 per car. The same supplier now makes the headliner for the Avalon large car, saving $9.80 per unit.
Material unification, which seeks to identify and develop single plastic formulas suitable for both interior and exterior applications. Reducing the number of plastics results in a net cost savings, says Bernas.
Mike Richardson, manager-Jaguar and Land Rover Research Group, says the industry is working hard to reverse a general upsizing of all vehicles. He says the weight increase for a typical luxury car now averages nearly 4.5 lbs. (10 kg) every year.
Richardson says the weight-creep effect is part of what drove Jaguar to use an aluminum monocoque construction for its all-new XJ flagship. The first series-production car to use aluminum for a unitized body structure, the Jaguar XJ is hundreds of pounds lighter than competitive vehicles in its segment, says Richardson.
Thanks to extensive use of aluminum, the V-8 powered XJ is 10% more fuel-efficient than the previous-generation XJ yet also accelerates 10% faster, he adds.
Read more about:
2004About the Author
You May Also Like