SPE Honors Plastics Innovation
The auto industry has responded to cost pressures and fuel-economy challenges with a flurry of creative ideas. The Automotive Division of the Society of Plastics Engineers recently honored the best of the best in the plastics field with its annual innovation awards: Powertrain: Diesel Exhaust Fluid System Both the category and Grand Award winner, the diesel exhaust fluid system on the '11 Ford Motor
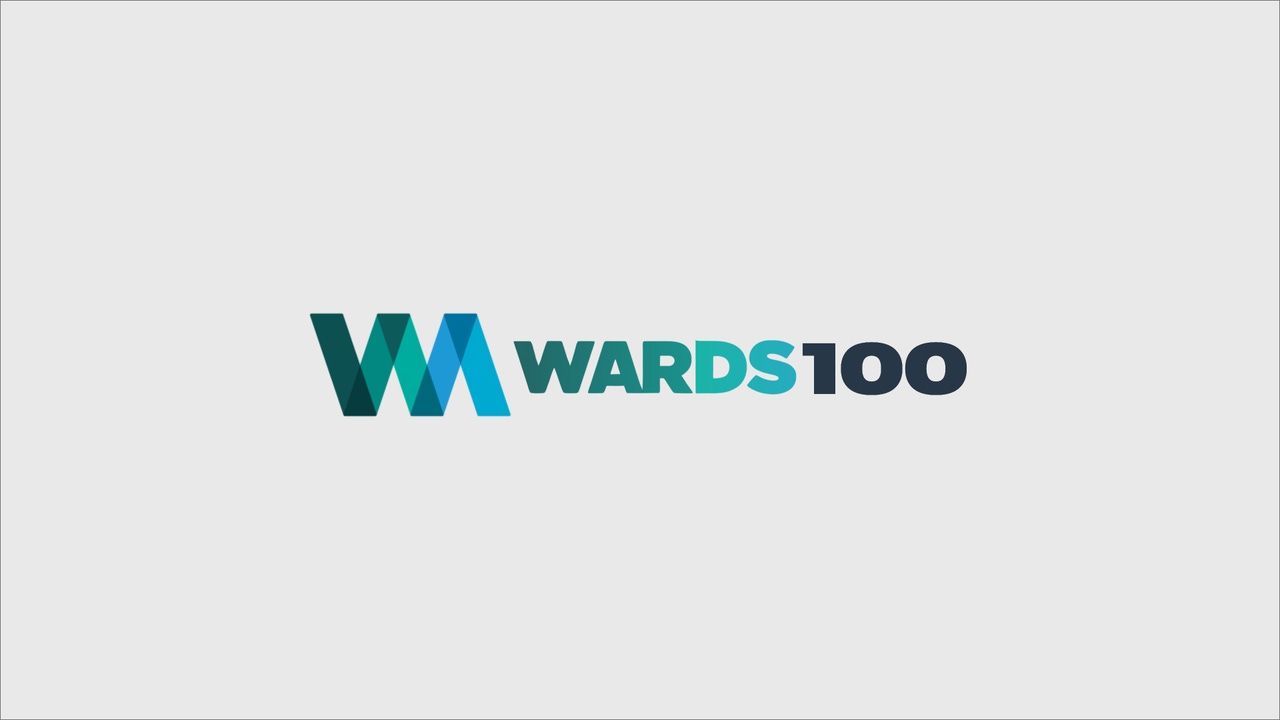
The auto industry has responded to cost pressures and fuel-economy challenges with a flurry of creative ideas.
The Automotive Division of the Society of Plastics Engineers recently honored the best of the best in the plastics field with its annual innovation awards:
Powertrain: Diesel Exhaust Fluid System
Both the category and Grand Award winner, the diesel exhaust fluid system on the '11 Ford Motor Co. SuperDuty pickup is the first all-plastic system on a high-volume pickup. It delivers urea fluid to the exhaust system to meet new emissions requirements.
Multiple materials and molding processes are featured on the system, which includes key components such as the filler pipe assembly, supply module with integrated pump, reverting valve, pressure sensor, heater and filtration unit.
The only other material that could have been used for this application would have been stainless steel, and that would have been seven times heavier and cost 40% more. Ford collaborated with Robert Bosch LLC and Kautex Textron GmbH & Co. KG.
Environmental: Recycled polyol for seat foam
Chrysler Group LLC collaborated with Magna Seating of America Inc. to create the first use of flexible urethane seat foam produced with polyols manufactured from post-industrial scrap foam.
A 2-stage closed-loop recycling process converts the scrap foam back into a polyol product, resulting in zero landfill waste and allowing up to 10% recycled content in new parts.
Body Exterior: Dual material sealing
Ford and suppliers Rochling Automotive AG and Rochling Automotive Italia srl use a projectile-injection technology process to enable a hollow ethylene propylene diene monomer bulb seal to be co-molded with a polypropylene cowl grille in a single process step, producing a single part. The result is a 30% weight savings (compared with a separate, extruded seal) and a 10% cost savings.
Body Interior: Self-reinforced airbag door system
PSA Peugeot Citroen worked with supplier Visteon Corp. to create the industry's first airbag door system that uses all polypropylene construction. That makes it fully recyclable and typical post-mold scoring and weakening of the door flap is not required.
Chassis & Hardware: Integrated carrier rail for rear-plastic door module
Previous plastic door module designs had separate metal rails that are attached to the module after molding. This innovative design has the window-regulator guide rail molded as part of the module.
Wire-harness clips, drum housing, location pin and the door-handle bracket also are integrated into the design. Hyundai Motor Co. Ltd. worked with suppliers Pyeong HWA Automotive Co. Ltd., ArvinMeritor Inc. and Arkal Automotive on the part, used on the '10 Hyundai Sonata.
Materials: Heat-resistant engine cover
Power-dense turbocharged engines create lots of heat and can present a challenge to underhood plastics. General Motors Co. worked with suppliers Camoplast Inc. and DuPont Automotive to develop an injection-molded engine cover that handles routine temperatures of 356° F (180° C) and periodic 392° F (200° C) temperature spikes.
The cover features a PA copolymer with new shielding technology for high-heat stability while doubling heat-aging property retention, compared with conventional nylons, and some specialty resins. The cover is used on the 2.0L Ecotec Turbo for a version of the Cadillac CTS sedan sold in China.
Process, Assembly & Enabling Technologies: High-gloss finish without paint
Interior trim parts on the '11 Ford Escape wins this category for being the first molded-in color, high-gloss, jet-black ABS instrument panel, console and door-finish panel applications produced by a modified injection process that eliminates paint while avoiding molding defects, such as flow marks and knit lines. The supplier is Summit Polymers Inc.
Safety: Inflatable seatbelts
Ford and supplier Key Safety Systems Inc. wins this category for an inflatable seatbelt design on the '11 Ford Explorer.
Special tubular webbing used in the shoulder portion of the rear seatbelts hides an inflatable airbag that provides extra protection for second- and third-row occupants. A new weaving technique is used to form the tubular webbing and a frangible edge that allows the belt to split and the airbag to deploy.
About the Author
You May Also Like