Suppliers Want More Sharing of Costs and Benefits from Systems Engineering
Automakers are looking to suppliers more and more for engineering work and to provide component "systems," but the conflict over how to distribute costs is escalating.The subject was spotlighted at the annual SAE International Congress and Exhibition's Blue Ribbon Panel in late February. Comments of leading executives from suppliers and automakers indicate the jury is still out.Nearly everyone involved
April 1, 1998
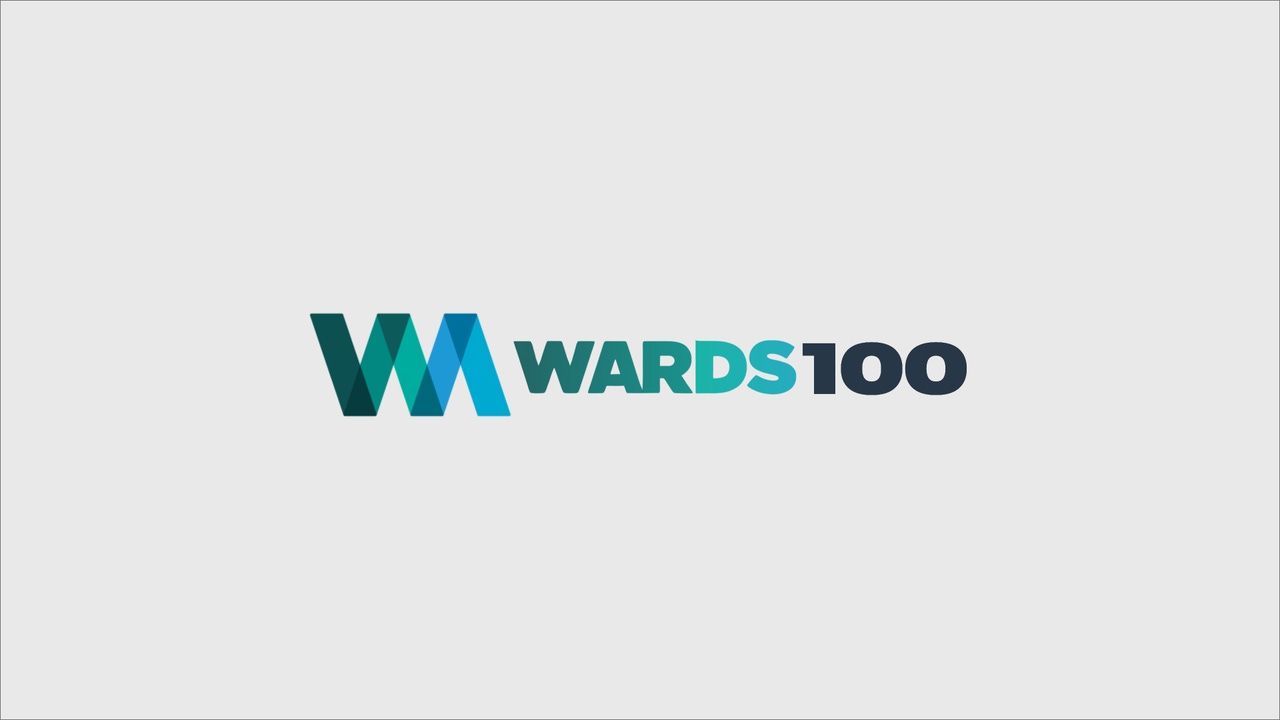
Automakers are looking to suppliers more and more for engineering work and to provide component "systems," but the conflict over how to distribute costs is escalating.
The subject was spotlighted at the annual SAE International Congress and Exhibition's Blue Ribbon Panel in late February. Comments of leading executives from suppliers and automakers indicate the jury is still out.
Nearly everyone involved agrees that the trend, which has its roots in Europe, is breaking new ground in North and South America.
"We're in a period of experimentation now," says Richard Parry-Jones, head of worldwide product development for Ford Motor Co. "Most people think there's more systems engineering work that will go to Tier One suppliers. Ford is going that way. BMW and Mercedes-Benz have been there for some time."
That should be good news for suppliers. Maybe.
So far the bulk of cost savings created by systems engineering is going to the automakers' bottom line.
Robert Bosch Corp. Chief Executive Robert S. Oswald says suppliers need to start making money soon on all this systems work, or the sourcing shift may be short-lived.
"If Tier Ones are not able to be profitable and support the research and development and equipment investments, then the whole idea of Tier One systems sourcing will die," Mr. Oswald says.
He says Bosch was involved with 15 to 20 projects over the last three years where it was asked to develop, tool for and deliver "systems" or "modules" - and most of them lost money.
"When most customers talk about modules they are talking about a delivery mechanism, not a design and engineering mechanism. If all you are doing is moving work around without sharing in the cost, that's a loser," Mr. Oswald says.
Chrysler Corp. is working to figure out some of the new realities, says Thomas W. Sidlik, executive vice president for procurement and supply and general manager of small car operations.
"Clearly, because of consolidation, the supplier base is putting more money into research and development," he says. "Where we can break through the cultural barriers and recognize those factors we're better off. No one can waste efforts. The cost is too high."
Eventually, he predicts, the larger suppliers will have more power in influencing design decisions and will save money by standardizing more parts that can serve more than one customer.
"The supplier has a potpourri of parts on the shelf. They come to us and say if we can make it fit, here's the price," says Mr. Sidlik. "If we want to modify the piece for our own purposes, then here's the price. We have to work together."
Systems engineering definitely is changing the way suppliers and OEMs relate, says Bill J. Carroll, Dana Corp. president of diversified products and distribution. Dana's rolling frame project for Dodge Dakotas built in Brazil is an example of the industry pushing new boundaries. The Dana frame is said to account for 45% of the total value of the truck.
"It's a juggling act. We add value and offer solutions and try to set the right price," Mr. Carroll says. "The way we dealt with each other in the past is not the future. We'll be further tied in. I don't think the OEs recognize all that can be done yet or all that will be done."
At the SAE, Lear demonstrated a future concept that would use robots to install an entire interior into a vehicle in four modular parts.
"The onus is on us to put the case in front of the OE," says Daniel A. Jannette, president of Lear Corp.'s technology division. "We've got to sell this idea."
There are limits to what automakers are willing to turn over to suppliers, executives admit.
"Cars are not like computers. They can't be made from pieces supplied by different vendors that you connect with plugs," says Francois J. Castaing, former executive vice president turned technical advisor to Chrysler Corp. "Chrysler has decided to keep specific technology in-house - platforms, suspensions, bodies, engines and automatic transmissions. Everything else, we bring in people to work with us," says Mr. Castaing.
Mr. Sidlik says Chrysler will continue to push its Supplier Cost Reduction Effort (SCORE), to encourage suppliers to find savings that Chrysler will share with the implementing supplier.
"Are we doing a better job than 10 years ago?" he asks. "Absolutely. Do we have a long way to go? Sure."
Read more about:
1998You May Also Like