Value Stream Mapping: Visteon’s Rude Awakening
Louis Whitlock has a cruel exercise to demonstrate for his employees at Visteon Corp. how inherently wasteful the manufacturing process can be. It’s called “value stream mapping,” a concept that may be familiar for manufacturing engineers. But it’s not often that a company will share the bare-knuckled results of such an evaluation with their peers at a major industrywide event. Attendees at Monday’s
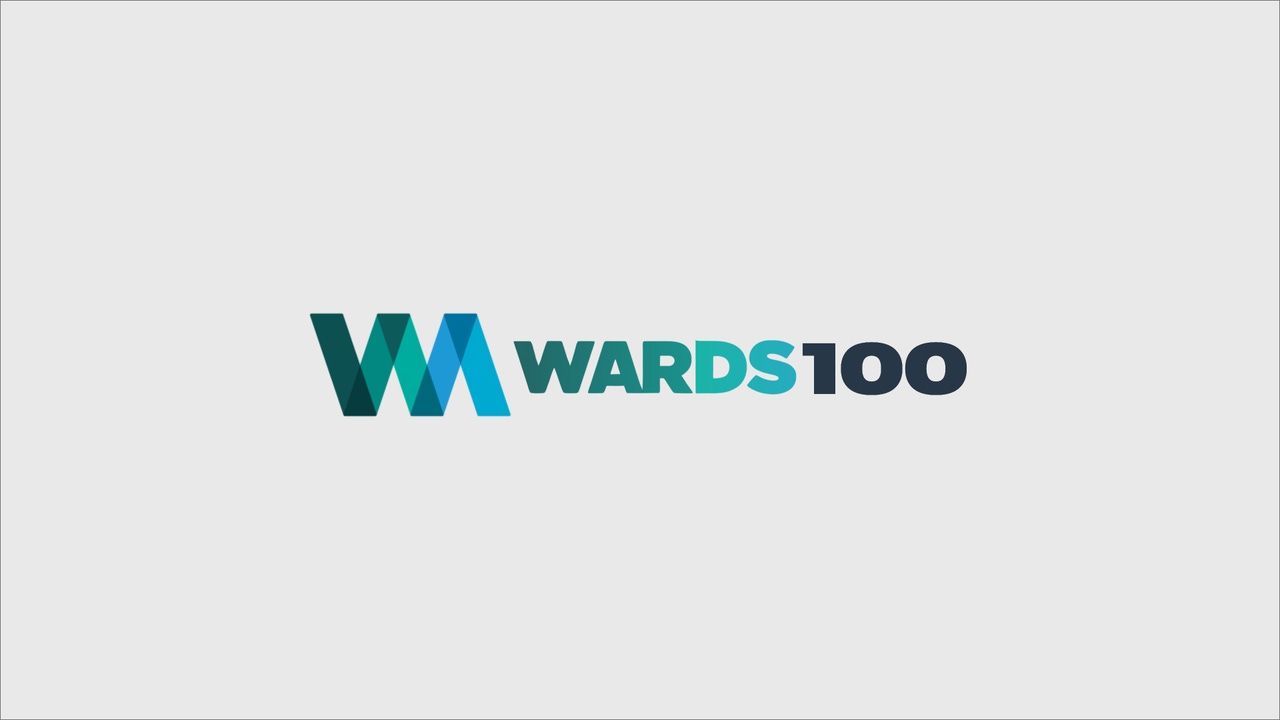
Louis Whitlock has a cruel exercise to demonstrate for his employees at Visteon Corp. how inherently wasteful the manufacturing process can be.
It’s called “value stream mapping,” a concept that may be familiar for manufacturing engineers. But it’s not often that a company will share the bare-knuckled results of such an evaluation with their peers at a major industrywide event.
Attendees at Monday’s World Class Manufacturing session got exactly that from Mr. Whitlock, Visteon’s manufacturing director who oversees seven North American instrument panel and electronics plants.
Through value stream mapping, Visteon tallied exactly how much value each plant creates in producing an instrument panel or the associated components.
Mr. Whitlock defines “value” as something the end consumer will pay for –- an air-conditioning system, for instance. The consumer will not pay, however, to test, ship, package or inspect the HVAC system.
The exercise revealed that Visteon’s Saline, MI, plant adds value only 0.26% of the time it takes to assemble a full instrument panel.
It sounds minuscule -– until compared to Visteon’s Atlantic Automotive plant in Benton Harbor, MI, which adds value only 0.05% of the time it takes to produce glove boxes, Mr. Whitlock says.
That’s not to say everything else is waste. Mr. Whitlock says certain processes are unavoidable in manufacturing, but value stream mapping can pave the way for major improvements.
His advice: Follow the flow of raw material, inventory and information within a factory. Diagram the quantity of material, where it enters and the time it takes for each process. Measure the cycle time, the average time between failures, the average time to repair and the amount of scrap.
“These are the exercises you have to go through,” Mr. Whitlock says. “It indicates we have a ways to go.”
It’s hard to estimate a target percentage for adding value because every product and process is different. But Mr. Whitlock says Toyota Motor Corp., with its much-emulated Toyota Production System, achieves 10% of value-added with its vehicle manufacturing process.
Why do such a gut-wrenching exercise? Because Saline is a crucial plant for Visteon, as it supplies complete instrument panels just-in-time to Ford Motor Co.’s Michigan Truck, Wixom and Wayne assembly plants. And Mr. Whitlock reports that every minute of downtime at Saline costs Visteon $100.
Read more about:
2001About the Author
You May Also Like