Why Not Us?
RAMOS ARIZPE, Mexico Metaldyne Corp. CEO Tim Leuliette got an interesting phone call recently from an executive with a European auto maker. He asked me about building an engine, Leuliette tells Ward's. Suppliers such as Metaldyne have been assuming more development work for powertrain components and systems, so it didn't come as a total shock. We have been working our way up the value chain, Leuliette
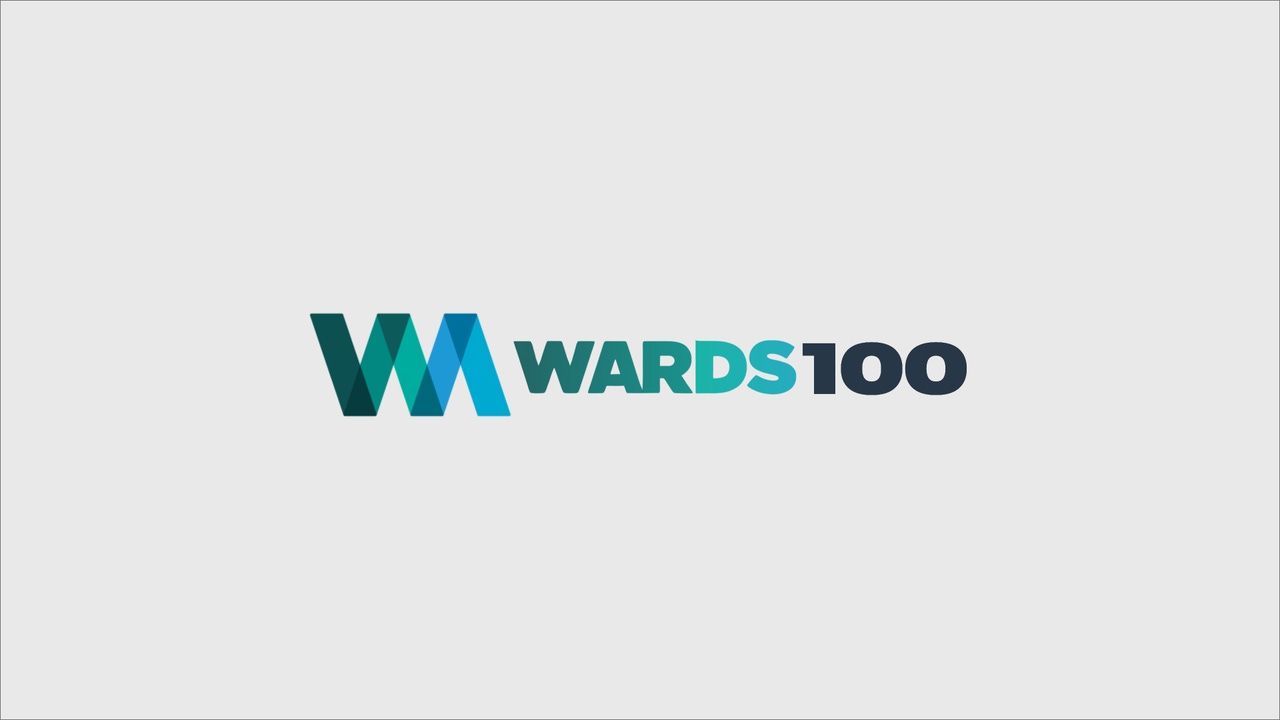
RAMOS ARIZPE, Mexico — Metaldyne Corp. CEO Tim Leuliette got an interesting phone call recently from an executive with a European auto maker.
“He asked me about building an engine,” Leuliette tells Ward's. Suppliers such as Metaldyne have been assuming more development work for powertrain components and systems, so it didn't come as a total shock. “We have been working our way up the value chain,” Leuliette says.
Here in the Sonoran desert 500 miles (804 km) southwest of Houston, Metaldyne celebrates a significant event that demonstrates the degree to which auto makers are handing off engineering and production of engine components once deemed a core competency of the OEMs. Few engine components are sacred anymore.
The Ramos Arizpe plant, which opened in 2000, produces forged powder-metal connecting rods for the Big Three auto makers located in the region.
Last year, the plant produced nearly $10 million worth of connecting rods for the Chrysler Group's 2.4L 4-cyl. engine and the 5.7L Hemi Magnum V-8 and for Ford Motor Co.'s 2L Zetec 4-cyl. and its newer 1.8L/2L I-4 world engine.
In January, Metaldyne opened a 30,000-sq.-ft. (2,787-sq.-m) expansion of the plant to machine the connecting rods forged next door. Machining begins in June. It's a big step, as OEMs traditionally have machined connecting rods themselves.
The expansion represents the first time a U.S. auto maker — in this case General Motors Corp. — has outsourced a fully machined connecting rod to a forging supplier for a high-volume engine program.
The connecting rods are for GM's new 3.5L “High Value” V-6 engine, which GM will assemble at its Ramos Arizpe plant. The engine is expected to replace the current 3.1L and 3.4L V-6 engines. The first recipient is the all-new '04 Chevy Malibu.
So what did Leuliette say when the European OEM called with such an intriguing proposition? He didn't dismiss it. The Metaldyne chief says his company is willing to take risks if the business case is there.
“Someone will supply an auto maker with a low-volume engine by the end of this decade,” Leuliette says. “If someone has to do it, why not us? If we have the capital, we'll do it.”
George Thanopoulos, president of Metaldyne's Engine Group, admits his company is not fully capable of engineering and building a complete engine, and that Metaldyne likely would partner with other component and engineering companies.
The company estimates 81% of the $180 billion global market for metalforming of driveline and chassis components remains in control of the OEMs. Leuliette expects that figure will fall to 50% by decade's end, with suppliers assuming control of the other half.
The expansion in Mexico is the latest in a series of events demonstrating Metaldyne's willingness to assume more product development responsibility.
In December, the supplier acquired a 40% share of the Chrysler Group's New Castle, IN, Machining and Forge facility, which produces suspension, engine and transmission parts. The investment cost Metaldyne $20 million, and it expects to take over 100% of the operation by year's end.
Meanwhile, Metaldyne management holds up the Ramos Arizpe plant as a testimonial to the hard work of its 115 employees.
For a powder metal forging plant, it's remarkably clean. The entrance to the plant, with its terra cotta roof and ceramic tile stairway, looks more like a Chi Chi's restaurant than a manufacturing facility.
Its quality record is superb: In three years, the plant has produced 4.2 million connecting rods for Chrysler Group, with a defect rate of only two parts per million. For Ford, the plant has produced 3.9 million connecting rods without a single defect in 27 straight months.
Metaldyne has spent $35 million at the plant, and more investment is coming to accommodate new business. The facility currently is at break-even, and the profit picture looks brighter with new programs ramping up.
The new machining plant is set up with traditional transfer lines — a series of machines, each dedicated to a specific task, such as tapping and rough boring. In the next plant expansion, another machining line will be added for connecting rods, and computer-numerically controlled machines will be employed for greater flexibility, each capable of multiple functions.
Read more about:
2003About the Author
You May Also Like