New Lexus Big Test for Toyota’s Georgetown Plant and Its New Manager
Launch of the TNGA-based ES marks the first time the U.S. facility will undergo a complete model change on its Lexus line, where quality is paramount.
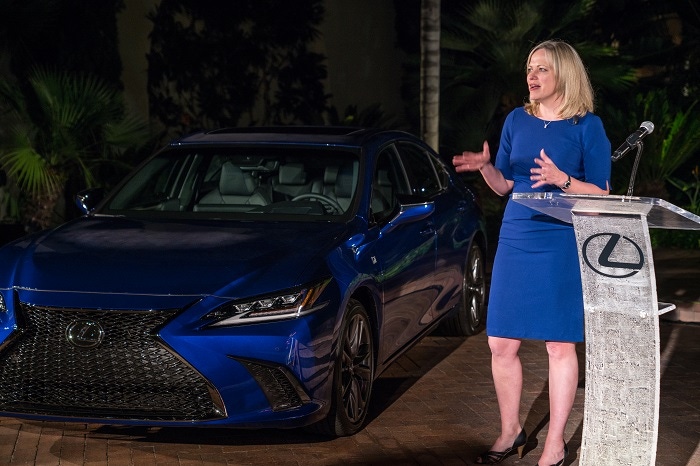
RANCHO PALOS VERDES, CA – The pressure’s on and the bar is high as Toyota gets set to begin production of the all-new ’19 Lexus ES at its Georgetown, KY, plant.
The new model marks the first major redo of the car since the automaker started building Lexuses at the U.S. facility four years ago, making the launch an extra challenge for the Toyota Motor Mfg. Kentucky plant. It also presents a big test for Susan Elkington, who took over as president of the operation in January and now is managing an entire vehicle-assembly plant – Toyota’s largest in the world – for the first time.
“Yeah, a little pressure,” Elkington acknowledges in an interview with WardsAuto here, where the cover was taken off the new ES that will hit U.S. showrooms in the fall. “The Lexus launch is pretty significant for us.”
In 2015, when the ES initially went into production at TMMK, the plant earned a top-ranked platinum (quality) award from consultant J.D. Power and Associates, putting it on par with the Lexus facility in Kyushu, Japan, she notes.
“So that’s a pretty high bar to stand up to (when) making this big of a change,” Elkington says. “But I think we’ll do a great job.”
With the new model, the ES moves to the Toyota New Global Architecture (TNGA) platform that underpins the Toyota Camry and Avalon models built on a separate line at the Georgetown plant.
Output of Camry, begun in July, is now at full speed, while the new Avalon is just in its third week of production and should reach peak volume within another six weeks.
Successful launches of the Avalon and ES topped the list of three key objectives Elkington set this year in taking over the reins at TMMK.
“Second is to make manufacturing competitive here in the United States,” she says, alluding to reports last year Toyota was disappointed with production costs at the Georgetown facility following the launch of the new Camry and a massive $1.3 billion redo required to convert the operation to TNGA production. “We’ve had some bumps in the road, so we need to continue to make kaizens (ongoing process refinements) and improve our efficiency.”
Many of the current inefficiencies stem from the aggressive transformation of the Georgetown plant and will be eradicated with time, a confident Elkington predicts.
“Ninety percent of our parts changed, 90% of our processes changed,” she says. “You become the most efficient…when you’ve been doing that same process for a long period of time. (But) since we’ve launched, our team members have come up with hundreds and thousands of kaizens, how we can save a step here, a cent here, and we’ve been implementing those over the last (few months).”
Third on Elkington’s list, and related to the first two, is extensive and continued training for the more than 8,000 workers at the 30-year-old Georgetown facility. Some 40% of the labor force has been on the job less than five years due to plant expansion and a large number of workers reaching retirement age.
“There’s a lot of education that needs to still happen and to really embrace the Toyota Production System and Lexus mindset,” says Elkington, who began her Toyota career with the startup of the Princeton, IN, assembly plant that launched truck production in 1999. “It’s not something that happens overnight. It takes years of training.”
The ’19 ES is undergoing its second set of production trials at the plant, with the new models mixed in during output of the current cars. Some of the manufacturing processes are unique to the new model, however, and must be tested on weekends, Elkington says, “but we can do a quick change and start back on Monday doing our regular production.”
Job One is set for late summer, and it will take about eight weeks for production to reach full capacity, she says. TMMK will produce most of the V-6 models for the U.S. market. Kyushu will supply some V-6 cars and ES hybrids.
With the shift to TNGA, more than 2,000 ES parts are all-new or modified. Georgetown added aluminum-hood production for the new Camry, and that operation will be expanded to hoods and fenders for the ʼ19 ES. The new Lexus also gets a revised wishbone suspension in the rear. Laser-screw welding processes are new to the body shop, increasing torsional rigidity of the new ES.
“We say it is going from buttons on coats to zippers,” Elkington says of the body construction.
A new color – a striking Sonic Blue – also adds complexity to the ES operation, because it requires multiple coats and two trips through the paint line.
“We’ve been doing trials to ensure we can paint those perfect the first time,” she says. “Repairing those is not so easy.”
TMMK will undergo the equivalent of 150,000 hours of training for the new ES, Elkington says.
“It’s more than just being able to install the parts in the right sequence,” she says. “We spend a lot of time on sensory training.”
Workers must be able to identify the right bolt by touch or learn to grab the right quantity of clips in the first try. Quality inspectors need to be able to spot fits outside the tight tolerance of 0.01 ins. (0.3 mm) by running gloved hands along gaps in the sheet metal and ensure by feel that stitching throughout the interior is at the perfect pitch and depth.
“Our expectation of our Lexus members is to utilize all their senses,” Elkington says.
She dismisses any suggestions Georgetown’s future is at risk from building only sedans in a market increasingly leaning toward CUVs, pointing to Toyota’s move to broaden the Camry, Avalon and ES offerings and market reach with more performance-oriented versions.
“I don’t think sedans are going to go away,” Elkington says, adding the switch to the TNGA platform will allow Georgetown to add other models to the mix more easily.
Georgetown has capacity for 550,000 vehicles and 650,000 engines. Last year, it assembled 420,589 vehicles, down 16.0% from 2016. That included 41,657 ES models, off 4.4% from a year earlier. Through March, plant production was down 6.4% to 108,033 units, including 10,807 outgoing ES models and 5,180 Avalons.
Wards Intelligence forecasts Georgetown will build 462,000 vehicles this year.
@DavidZoia
About the Author
You May Also Like