DCC Has Just One Word for You: 'Plastics'DCC Has Just One Word for You: 'Plastics'
Offering further proof that it is serious about someday producing plastic-intensive vehicles, DaimlerChrysler AG reveals last month it plans to offer 4,000 or 5,000 Jeep Wranglers with unpainted, thermoplastic hardtops beginning in '01. The new removable thermoplastic caps will replace those made of painted, thermoset sheet molding composite (SMC) material.The new top weighs just 47 lbs. (21 kg).
December 1, 1999
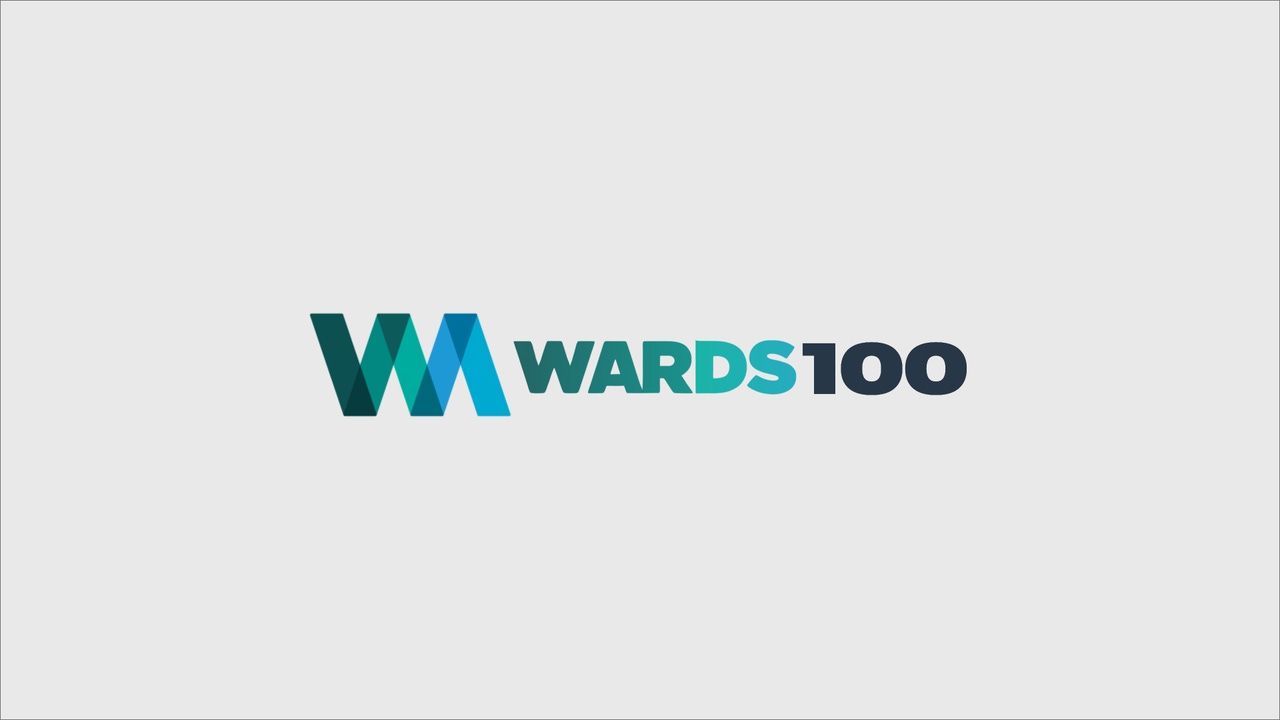
Offering further proof that it is serious about someday producing plastic-intensive vehicles, DaimlerChrysler AG reveals last month it plans to offer 4,000 or 5,000 Jeep Wranglers with unpainted, thermoplastic hardtops beginning in '01. The new removable thermoplastic caps will replace those made of painted, thermoset sheet molding composite (SMC) material.
The new top weighs just 47 lbs. (21 kg). That's 23 lbs. (10 kg) less than the current SMC parts. They also can be made 30% faster and are about 10% less expensive to produce, says DCC President James P. Holden.
The biggest advantage of the new material, though, is the fact that it allows components to be colored as they are molded, eliminating a trip through the paint shop. A typical automotive-plant paint shop can cost $200 million to $400 million, including the expense of costly emissions control equipment, so if painting is eliminated it can yield huge cost savings.
The fact that the material being used is a thermoplastic rather than a thermoset SMC also offers several advantages, DCC says, most notably ease of recyclability. Although SMC proponents say their material is indeed recyclable, once it is heated and formed into a part, it cannot be melted down again and reused.
Chemists liken the thermoset process to making a hard-boiled egg. Thermoplastic polymers, on the other hand, are more like ice and water. They can be fabricated into parts, and then melted down and recycled into new parts fairly easily - although not as easily as some thermoplastic interests would have you believe. The properties of thermoplastics often degrade over time and with exposure to sunlight and various environmental contaminants.
DCC first signaled its plastic car research in late 1997 when it unveiled the CCV; a small concept car aimed at emerging markets. About 18 months ago it showed off the Pronto Spyder, a plastic-bodied 2-seat concept roadster and several other plastic-bodied prototypes. Although plans to make the Jeep hardtops signals some progress has been made, a complete car or truck using this plastic molding process is likely five, 10 or more years away, Mr. Holden says.
At the center of the process is the world's largest (8,800-ton) dual-platen injection molding machine housed at the new Detroit Technical Center of Husky Injection Molding Systems in Novi, MI. The machine is claimed to be twice the size of the largest molding machines used in the auto industry today and can inject more than 100 lbs. (45 kg) of thermoplastic material at one time. That's enough to create half of a car body in one "shot," DCC claims.
Mr. Holden says there still is work to be done in perfecting surface finishes of the plastic panels, improving body rigidity and solving the recycling issues for adhesives. But he says molded-in color, large plastic body panels "could become an essential part (of the company's) small car strategy" around the world. "We have to prove this will work still, but we're beyond the stage where we can't see our way through," he says.
About the Author
You May Also Like