High-End Acceptance
Aluminum may be losing some high-volume applications in the U.S., but it increasingly is well accepted by European auto makers, particularly high-end producers such as Ford Motor Co.'s Jaguar Cars and Volkswagen AG's Audi Div. And while they don't have all-aluminum showcase vehicles like the Jaguar XJ or Audi A8, BMW AG and Mercedes-Benz also are heavy users of the light metal. In a geographic area
September 1, 2004
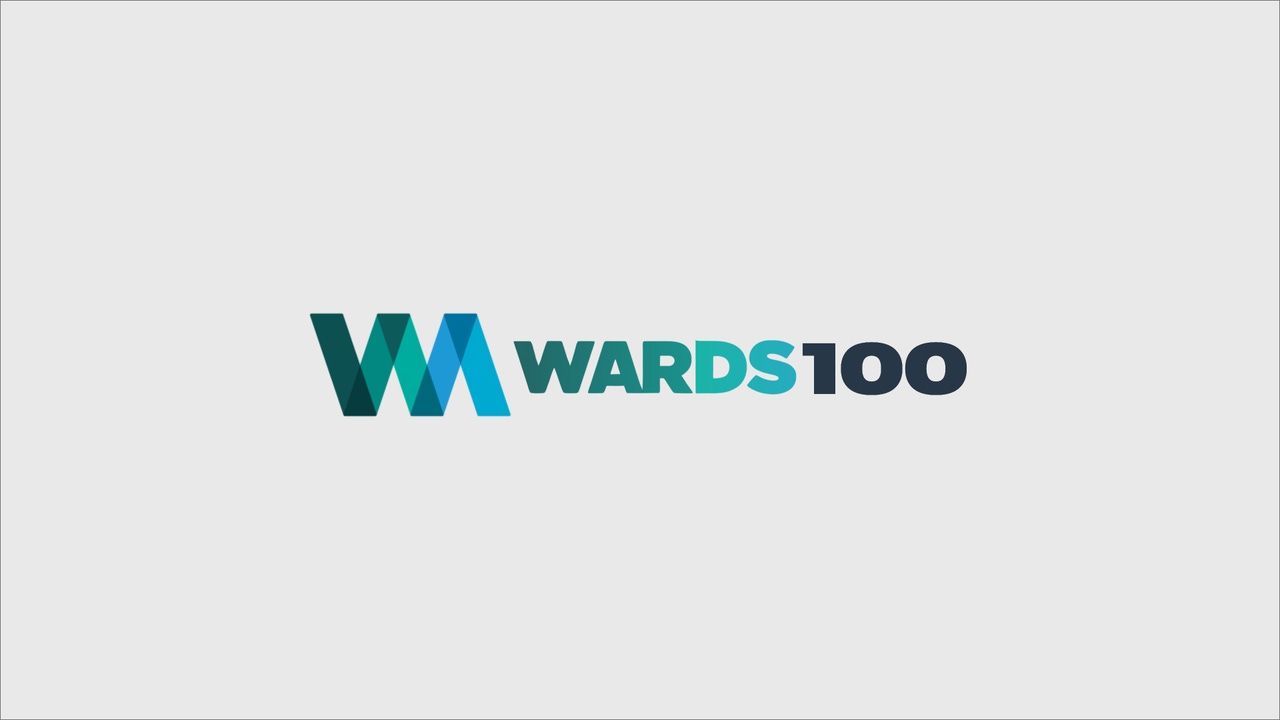
Aluminum may be losing some high-volume applications in the U.S., but it increasingly is well accepted by European auto makers, particularly high-end producers such as Ford Motor Co.'s Jaguar Cars and Volkswagen AG's Audi Div.
And while they don't have all-aluminum showcase vehicles like the Jaguar XJ or Audi A8, BMW AG and Mercedes-Benz also are heavy users of the light metal.
In a geographic area where fuel costs two or three times as much as it does in the U.S. and all-out performance is highly valued, designers and engineers in Europe are finding it easier to justify aluminum's higher cost in body panels and structural areas.
According to Mark White, senior body structures manager for Jaguar and Land Rover vehicles for Ford Motor Co., aluminum costs about $1,400 per metric ton, compared with $600 for conventional steel.
Using aluminum for next-generation Jaguars “is not something we can confirm today, but given the fact that we spent five years researching and doing all the work on aluminum and we're so pleased with the results we've got back so far, there's a very good chance it will stay a part of our future,” Michael Mohan, chief program engineer-XJ Series, tells Ward's at a recent long-wheelbase XJ drive event.
“It's great for fuel economy, (it provides) strength, durability and it transpires into a fantastic car.”
Jaguar Cars' Castle Bromwich assembly plant in the U.K. is preparing its case for more aluminum vehicles, having successfully validated the concept with the aluminum XJ.
The upfront investment is paying off, says Jaguar's White. The XJ is profitable, he says.
The next step is the business case for future aluminum monocoque Jaguars. Following the brand's cycle plan, the next-generation S-Type would be up for consideration first, as an '06 or '07 model, followed by the XK around 2010.
Bromwich assembles the current S-Type and XK, but only the XJ has an all-aluminum unibody architecture with steel subframes.
Ford has invested in a dedicated aluminum pressing facility at Bromwich for the XJ. The stamping facility, adjacent to the body assembly line, can handle aluminum versions of the S-Type and XK, should the auto maker go that route in the next generation.
“We have the ability to do all three (cars in) aluminum if the business case is there,” White says. “We know what it costs to do it for other models. But if they don't meet the cost target, we won't do it,” he says, noting he will have a series of deadlines to meet over the next three years.
The auto maker is identifying where costs are too high and working to reduce them. The goal is to further cut weight (aluminum currently reduces weight 40%-45% over conventional steel); develop an even more efficient aluminum body structure; and improve manufacturing, such as rationalizing some of the 17 different riveting processes.
Despite growing acceptance in Europe, and rising fuel prices in the U.S., Detroit-based auto makers are far less enamored with aluminum as an auto body material. In fact, General Motors Corp. is backing off its use of aluminum for hoods and liftgates on nine cars and trucks starting in the '05 model year, says Jody N. Hall, engineering group manager-GM Metal Fabricating Div.
Last year, the company produced almost 700,000 aluminum hoods and 407,000 aluminum liftgates.
The auto maker currently uses the lighter, but substantially more-expensive, material for hoods on nine models and for the liftgates of its large SUVs.
That number will drop to six for a 3-year stretch ('05-'07) and increase by one for '08, says Hall.
— with John Stoll
Read more about:
2004About the Author
You May Also Like