Mercedes-Benz Launches eCampus Battery Development CenterMercedes-Benz Launches eCampus Battery Development Center
The German-based research operations aim to cut the cost of future electric-vehicle batteries while significantly increasing energy density.
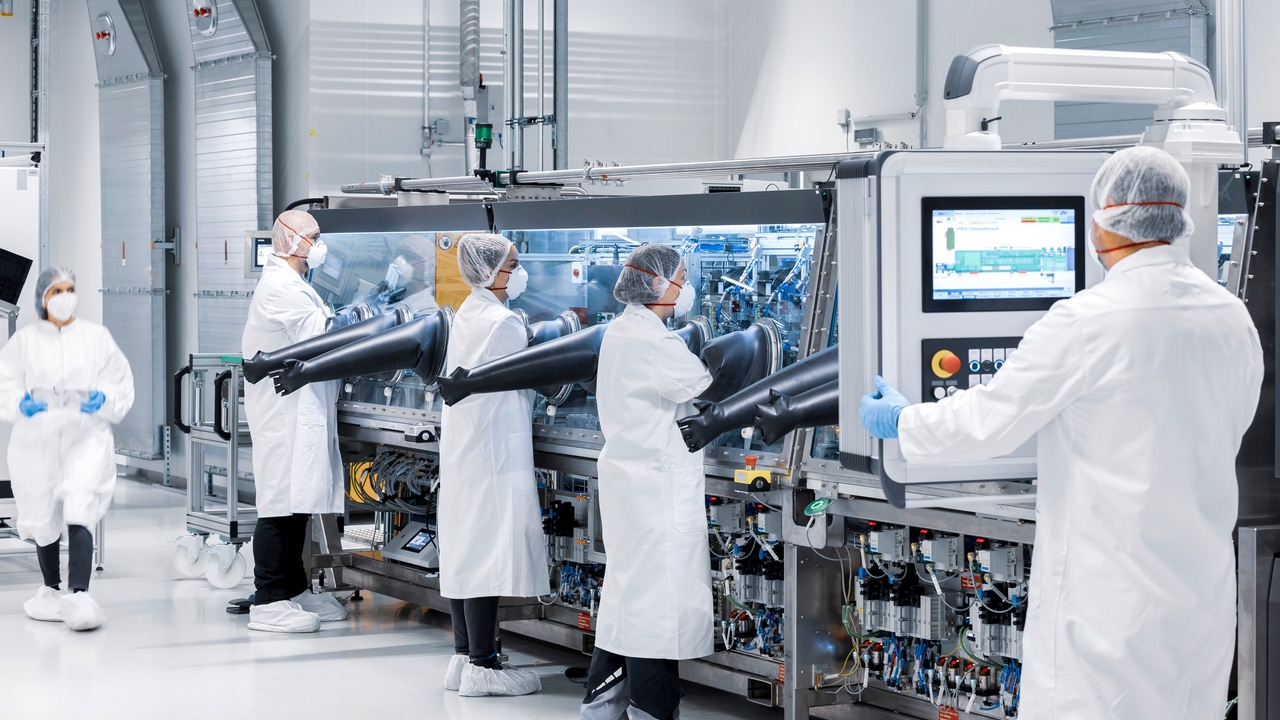
STUTTGART, Germany – Mercedes-Benz opens its eCampus battery R&D center here, aiming to dramatically reduce costs and improve batteries’ energy efficiency for future electric models.
The center, located in the heart of the German automaker’s existing internal-combustion engine development operations at its Untertürkheim factory on the outskirts of Stuttgart, is part of a $15.2 billion (€14 billion) investment earmarked by Mercedes-Benz for passenger car development operations in 2024.
The eCampus has been created to test and develop different variations of battery cell chemistry, including lithium-ion cells with silicon composite anode material, cobalt-free cathode chemistries and solid-state battery technology, providing Mercedes-Benz with the sort of in-house battery competency it has traditionally enjoyed with gasoline and diesel engines.
“The goal is to develop the best possible cells with Mercedes-Benz DNA, as well as to build expertise for their industrialization. We’re seeking to take a leading technological role. The eCampus brings us closer to this. The work being done here will help reduce battery costs by more than 30% in the coming years,” Mercedes-Benz’s chief technology officer, Markus Schaeffer, tells WardsAuto.
At a ceremony accompanying the opening of the center, Mercedes-Benz reveals it is working to increase the energy density of batteries for electric vehicles to up to 900 Wh/l.
This compares to the 550 Wh/l energy density of the CATL-supplied lithium manganese cobalt cells used by the recently updated EQS.
Previously, Mercedes-Benz said the lithium-ion cells with silicon composite anode being developed in partnership with U.S. company Sila Nanotechnologies and earmarked to first appear in the electric-powered G-Class had been tested at up to 800 Wh/l.
High-energy-density batteries can be manufactured to a smaller overall capacity without any reduction in range, lowering the overall cost, says Schaeffer.
Mercedes-Benz says the construction of a so-called “Industrial Cell Lab” on the site of its eCampus will enable it to independently manufacture and test battery cells with differing chemistries on an industrial scale with much shorter lead times than is currently the case.
Schaeffer reveals tens of thousands of cells (pictured, below) can be produced annually at the eCampus facility – from electrode production through cell assembly with electrolyte filling and formation with the first charge and discharge cycles.
Battery cells developed by Mercedes-Benz are planned to be placed into production both in-house and in cooperation with selected partners, including Automotive Cells Co. operated together with Stellantis and Total Energies/Saft as well as China’s CATL.Besides developing its own batteries, Mercedes-Benz also is committed to producing its own electric motors and power electronics software packages in-house. The move, which lessens its dependence on traditional component suppliers such as ZF, Bosch and Mahle, is part of efforts to reduce the overall cost of electric drivetrains.
About the Author
You May Also Like