Part Shortages Likely to Recur
It didn't take an expert to see this crisis looming: Auto-part suppliers that downsized in the face of historic-low vehicle sales likely would face capacity shortages once the market recovered. That day has arrived. Ford, Chrysler, Volkswagen and Daimler have suffered recent plant closures because suppliers could not ship enough components, particularly microchips and certain plastic resins. The shortages
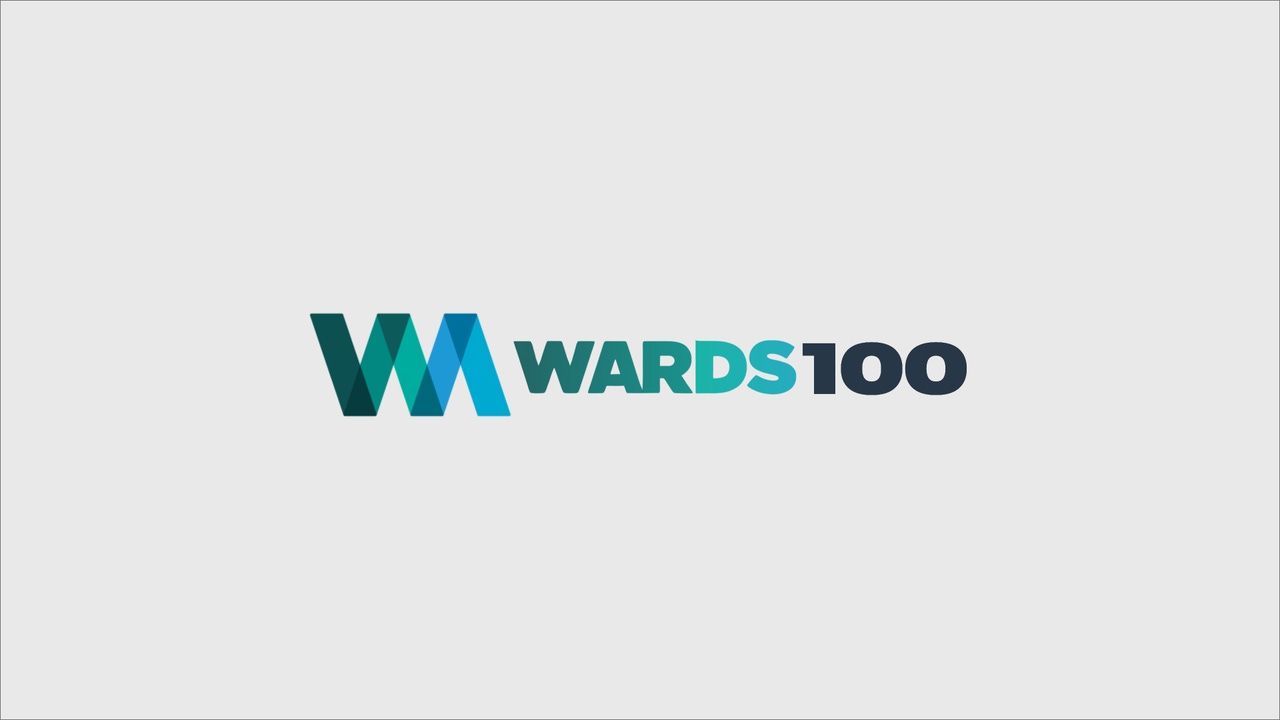
It didn't take an expert to see this crisis looming: Auto-part suppliers that downsized in the face of historic-low vehicle sales likely would face capacity shortages once the market recovered.
That day has arrived.
Ford, Chrysler, Volkswagen and Daimler have suffered recent plant closures because suppliers could not ship enough components, particularly microchips and certain plastic resins.
The shortages have been temporary, and the worst of them have passed, thanks to premium-fee air shipments and other suppliers stepping in to fill the void.
But the problem is sure to resurface if vehicle-production volumes continue their upward trajectory, industry sources say.
The issue is destined to alter the competitive landscape as suppliers jostle to win new business during part shortages and do everything they can to retain those contracts. The problem also could drive further consolidation of the supply chain by opening the door to acquisitions.
“It does mean the suppliers that are there for the OEMs might be better positioned as a more reliable supplier who can get some new contracts,” Paul McCarthy, automotive transaction services strategy leader for PricewaterhouseCoopers, tells Ward's.
“That's a key lesson from past economic cycles,” he says. “This is a good time for suppliers to try to change market share. It could affect some of the competitive positions of these companies and their reputations.”
TI Automotive CEO Bill Kozyra says the parts shortage is most acute among smaller Tier 2 and Tier 3 suppliers that were forced to downsize and remain unable — and perhaps reluctant — to secure financing for expansion.
“We've known for the past six months this was coming with some of the smaller suppliers,” Kozyra tells Ward's. “Most of us can go out and borrow money today, but some of the smaller guys are still struggling. The terms by which they have to agree to borrow money are still unacceptable.”
As chairman of the board for the Original Equipment Suppliers Assn., Kozyra speaks for 380 parts producers and says shortages would be less frequent if auto makers could better predict how many components they will need.
“We continue to voice the challenges suppliers have around instability in the forecast and not being able to plan properly for capacity,” he says.
The shortage of microchips and integrated circuits, necessary for electronic controllers governing everything from engines and transmissions to door locks and window regulators, is “almost coming to an end,” Kozyra says. “That's been something the big suppliers of electronics and the OEMs have been managing vigorously for the last 12 months.”
Those Tier 1 suppliers affected include Delphi, Robert Bosch, Denso and Continental.
Continental spokeswoman Kathryn Blackwell says the supplier has suffered a chip shortage for the last 12 months as vehicle output picked up.
“The increase in vehicle production was far more steep than anyone predicted and that put a stress on the entire system,” she says. “But we felt it most sharply in the chip supply,” partially because auto suppliers must compete with makers of consumer electronics for the finite pool of chips.
With U.S. vehicle-production volumes stabilizing, Blackwell says, “the worst is behind us” with regard to the chip shortage. “We've now had enough time to ramp up our production, and we've also had time to work with our suppliers to increase their production.”
Delphi spokesman Lindsey Williams says the supplier is facing a chronic shortage of integrated circuits. “Although IC suppliers are adding capacity, supply is expected to be tight until the second half of the year,” he says.
Much of Delphi's excess capacity was eliminated during the recent restructuring as part of its 4-year bankruptcy case.
Today, the supplier is growing and recently established manufacturing operations in Kokomo, IN, to support production of power electronics. It also opened a new connection-systems facility in Mexico to support regional customers.
Williams says the shortage could remain problematic, along with escalating costs in the commodities market through mid-year.
“As fuel prices continue to increase, we could see stronger demand for alternative-fuel vehicles, which could drive greater demand for specialized power electronics and related components,” he says.
A number of suppliers see parts shortages as an opportunity to snag new business by filling the pipeline when the customer needs it most.
Interior-trim supplier International Automotive Components was formed in 2007, just in time for a massive industry downturn that forced the closure of 10 plants. IAC weathered the downturn of 2008 and 2009 by maintaining sufficient manufacturing capacity with the expectation that volumes eventually would return.
Along the way, the company filled some of that capacity with about $400 million of transfer business taken over from failing suppliers, says John Smail, senior vice president for IAC North America and Asia.
“If some suppliers are incapable of fixing their capacity issues, OEMs will know this and likely take a more cautious approach in terms of who they award the business to,” he says. “Also, OEMs have a proven track record of suppliers they can airlift business to, in the event some suppliers cannot keep up with demand.”
Smail says IAC on more than 20 occasions since 2008 has demonstrated its ability to quickly take over supply contracts and employ airlifts without disrupting the customers' production schedules.
In its core product sectors (instrument panels, cockpits, consoles, door trim, overhead systems and acoustics), Smail says IAC can “keep up with demand anywhere in the world. Where we do not have the capacity, we have taken steps to add it.”
As suppliers scramble to meet rising component demand, they must be careful not to sacrifice quality in the process, experts say.
Blackwell says Continental's suppliers have added production capacity, “and we have seen continuously improving quality levels from our electronics suppliers through this challenging time.”
But quality can't be rushed, she says. “Even with new segments — turbochargers, for example — we are talking years, not months, before we are ready to introduce a quality product to the market.”
TI's Kozyra says the shortage of PA 12 resin used to make nylon has motivated his engineers to develop replacement materials, which TI intends to introduce near-term.
“It's a new material that will serve the same purposes,” he says. “You can't operate under a global shortage of raw materials year-round.”
OESA conducts a monthly “Supplier Barometer” and in January found 61% of 102 participating companies reporting raw-material shortages, up significantly from last year, and expecting the shortages to continue for at least three more months.
Specialty steels are among the raw materials in short supply as of late, says OESA Senior Vice President David Andrea. “Steel suppliers have taken out too much capacity. It doesn't take much with very lean inventories through the entire system to raise an issue very quickly.”
In North America, steel mills were running at a capacity utilization rate of about 40% during the downturn, so plants were mothballed. “But it takes time and a lot of money to bring the furnaces back online,” Andrea says. He estimates steel mills presently are operating at 70% efficiency rates.
The sagging economy in recent years set the stage for a parts shortage, as 62 major bankruptcies negatively impacted the industry supply chain in 2009, alone. As suppliers failed, tooling was moved from dozens of manufacturing sites to other more stable companies.
Andrea says many suppliers “put together SWAT teams to have the capability to go in quickly, accept the tools from a competitor and start production in a very timely and efficient manner.”
But in some cases, continuity of supply was not maintained. “The cardinal sin is to shut down an assembly plant,” he says. “It can ruin the best of reputations.”
As the industry recovers, so do economic indicators. Employment among U.S. auto suppliers stood at 435,000 workers as of October — a sign of improved productivity — after bottoming out at 392,000 in July 2009. A decade ago, the supply chain employed some 845,000 people in the U.S., OESA reports.
Capacity utilization among U.S. supplier plants also is on the rise, from the low-water mark of 45.3% in June 2009 to about 62% today, Andrea estimates.
So even though there may be too much capacity in certain product sectors, there's not enough in others. “We need to add capacity in electronics as we take out underutilized capacity elsewhere,” he says.
McCarthy, from PwC, says the parts shortage stems from the supply chain's “insufficiently flexible business model” with regard to staffing, labor and materials. “All that is a testament to really how bad we are at planning in the auto industry.”
But he sees the situation easing in the next six months.
“It will get better because we'll get smarter,” McCarthy says. “We'll now be ready for something we frankly should have been ready for, which is the volatility and sometimes the quick and uncertain periods of recovery and volume shift that you tend to see in a recovery.
“It's shame on us for not being prepared for this.”
WARDSAUTO.COM
OEMs Willing to Swallow Raw-Material Price Increases subscribers.wardsauto.com/ar/oems_price_increases_110202
Read more about:
2011About the Author
You May Also Like