Leaf Expected to Fit Right in at Smyrna Plant
Nissan will assemble its new Leaf EV on the same line as the Altima and Maxima, using similar installation procedures.
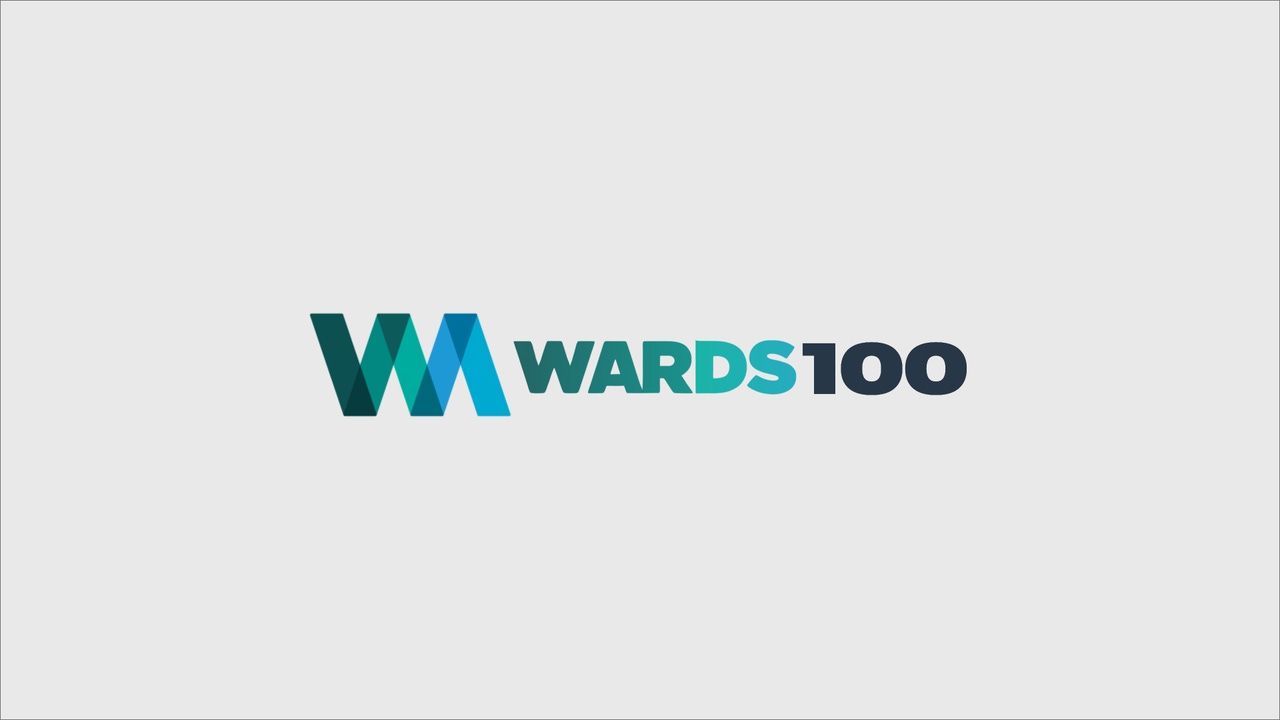
SMYRNA, TN – Nissan North America Inc. is looking to slip its Leaf electric vehicle into the production mix here with as little upheaval as possible.
“As unique as the (Leaf) is from a parts standpoint, what we want to do for our (assembly-line workers) is make it just like any other car,” Dan Heur, project manager-vehicles, says here during a media tour of Nissan’s Smryna plant.
Rather than dedicating a line to the Leaf, Nissan will be weaving the EV into the mix with the Altima and Maxima gasoline-powered passenger cars currently built here.
The scheme is the same at Nissan’s Oppama, Japan, plant, where the Leaf is built on a line that includes the Juke and Cube cross/utility vehicles.
Leaf production is set to get under way at Smryna in fall 2012. Nissan also will build the car at its Sunderland, U.K., plant starting in 2013.
The car’s lithium-ion battery and electric motor, which Nissan calls an “e-powertrain,” are the main two components that differentiate the Leaf on the assembly line, Heur says.
To make it easy for Smyrna workers to adapt to building the car, the battery and motor will be installed at the most obvious points in the assembly process.
Overhead system to be upgraded to carry heavy batteries.
For instance, the Leaf’s Li-ion battery will be dropped in where Nissan decks, or installs, the fuel tank for the Altima and Maxima.
The e-powertrain will be installed at the point where the gasoline engine for the Altima and Maxima is mounted.
Assembling the Leaf at Smryna will require some equipment upgrades, for which Nissan has earmarked an unspecified portion of the $1.4 billion loan it received in January from the U.S. Department of Energy.
Because of the extreme difference in weight between the 5- to 15-lb. (2.3- to 6.8-kg) plastic fuel tanks and the Leaf’s 600-lb. (272-kg) battery, Nissan will need to reinforce the assembly line’s claw-type carriers, Heur says.
The Leaf’s motor is similar in shape to the Altima’s I-4 and V-6 engines, but slightly smaller in size, he says, so only a limited “tear-up” and process change is required at this part of the line.
Nissan officially hasn’t announced where it will source the Smyrna-built Leaf’s motor, but Heur says it is likely final assembly will be nearby.
“We do a little powertrain assembly here, where we marry the transmission together with the gas engine,” he says. “We’ll do something similar for our electric powertrains.
“They’ll be married in an offsite area, then they’ll be brought in in sequence, so you’ll see a V-6, an I-4, an e-powertrain or whatever the production mix is for that day.”
Nissan also is applying a portion of the DOE loan toward a new onsite battery plant, opening in fall 2012.
Construction of the battery facility is in the early stages, with excavation already completed and footings now being poured.
Heur says Nissan is trying to be as frugal as possible, calling the new plant’s design “no frills.”
In the spirit of the Leaf, the auto maker is employing some green practices in the construction process. Rather than hauling away boulders unearthed onsite, the rocks are being crushed into two different types of gravel to be used later in the construction process.
Workers at the new battery plant, located where the old test track used to be at the back of the property here, will manufacture the Li-ion cells, assemble four cells into single modules and install 48 modules into each Leaf pack.
While Leaf capacity at Smyrna will be 150,000 units annually, the auto maker will be able to produce 200,000 packs per year.
Heur says Nissan hopes to sell the packs it doesn’t use for the Leaf to other manufacturers.
“We’re actually looking to see if there’s additional outside interest for the batteries. None have been identified yet, but that’s a possibility.”
Read more about:
2010About the Author
You May Also Like