Nissan Oz Plant Producing Aluminum Castings for EVs
The auto maker last year awarded the plant exclusive manufacturing contracts for the three EV parts that eventually will generate about A$160 million in export revenue.
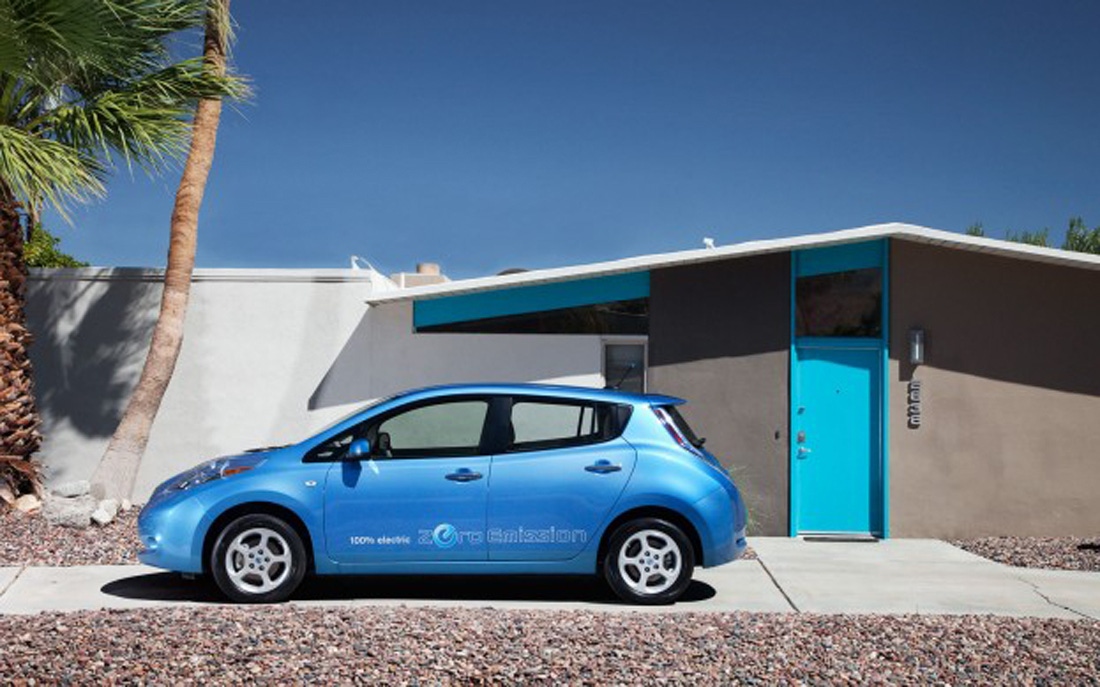
The first shipment of Australian-made components for Nissan electric vehicles is on its way to Japan.
The aluminum components made at the Nissan Casting Australia Plant in Dandenong, Victoria, include the inverter case, inverter water jacket and water jacket cover for EVs such as the Nissan Leaf.
The facility is operating three shifts, six days a week, and employs 140 full-time employees who this year will produce more than 2 million aluminum castings, most of them exported to Nissan factories in Japan, Thailand, Mexico and the U.S.
The parent company last year awarded the plant exclusive manufacturing contracts for the three parts that eventually will produce about A$160 million ($164.2 million) in export revenue.
The components use new casting technologies developed in Victoria in consultation with Nissan, the Commonwealth Scientific and Industrial Research Organization and the Center for Applied Special Technology Co-operative Research Center.
Nissan expects to spend a total of A$21 million ($21.6 million) on its sustainable, zero-emissions technology manufacturing operation to support the Dandenong plant.
The main business activities of the factory located 20 miles (30 km) southeast of Melbourne are high-pressure die casting, low-pressure die casting and CNC machining.
Founded in 1982, the plant reinvented itself as a stand-alone supplier after Nissan’s withdrawal from Australian vehicle manufacturing in 1991.
It produces core aluminum castings including transmission housings, clutch housings, rear-drive housings, cylinder heads and oil-pan assemblies. Accessory manufacturing was introduced in 2011 with tow bars, sports bars and nudge bars.
The Australian castings can be identified by a small kangaroo stamped on the outside of each casting.
About the Author
You May Also Like