Nissan’s Flexible Manufacturing Moves to India, Other JVs
Nissan has lowered its breakeven point to 60%-70% of capacity in Japan, or less than 1 million vehicles annually, the auto maker’s top manufacturing executive says.
February 3, 2010
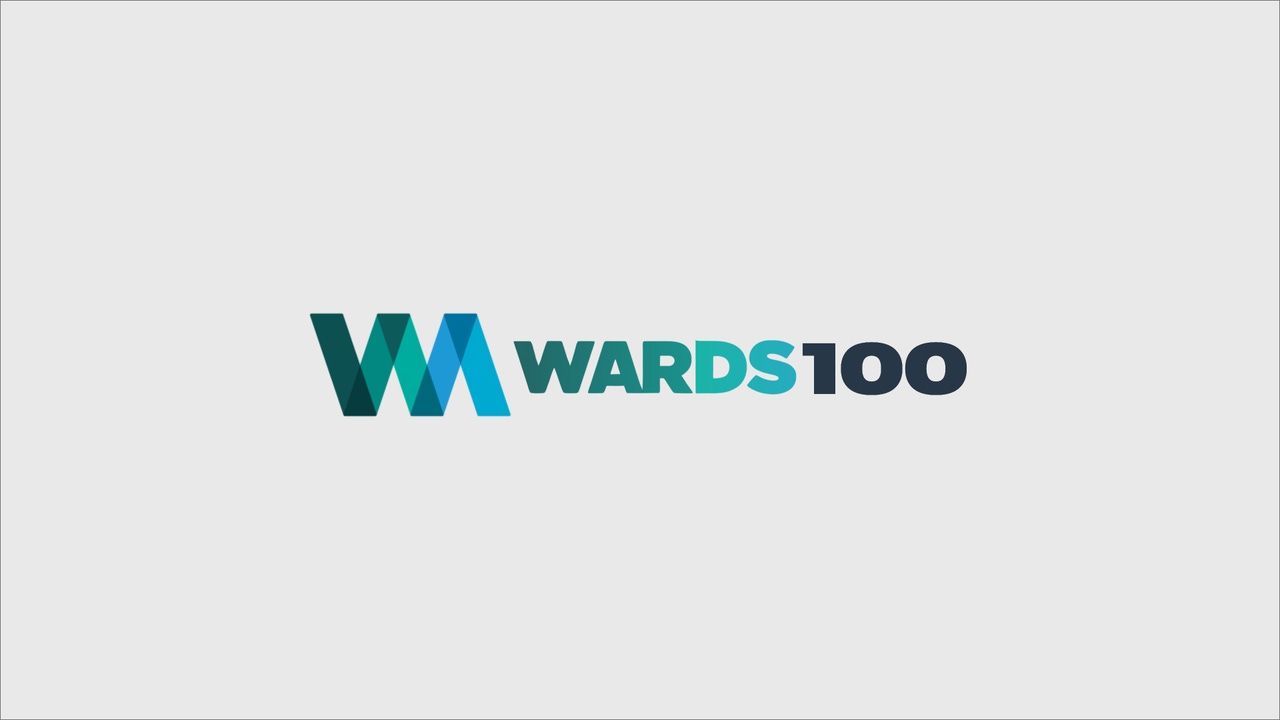
TOKYO – Having engineered a dramatic financial turnaround and significantly lowered its breakeven in the wake of the global economic slump, Nissan Motor Co. Ltd. is embarking on the next wave of efficiency initiatives.
Included is a broadening of its flexible manufacturing system to joint-venture plants in emerging markets and expansion of a modular-assembly philosophy that has suppliers co-locating inside Nissan assembly plants.
For an update on where things are headed, Ward’s interviewed Nissan’s manufacturing head, Executive Vice President Hidetoshi Imazu. In his current position since February 2009, Imazu previously headed up European manufacturing and supply-chain operations.
Here’s an edited excerpt from that interview:
Ward’s: Nissan reported a devastating ¥230.4 billion ($2.5 billion) operating loss in the fourth quarter of fiscal 2008, then surprised analysts with first- and second-quarter fiscal 2009 profits and now is forecasting a ¥120 billion ($1.3 billion) surplus for the full fiscal year ending March 31. Last spring, when you announced fourth-quarter results, you forecasted a ¥100 billion ($1.1 billion) loss for the current fiscal year. That is a ¥220 billion ($2.4 billion) turnaround. How did you achieve this?
Imazu: We cut production sharply to deal with growing inventories after the Lehman shock. But we began reducing output several months prior to the market meltdown at our Canton, MS, truck plant in response to the decline in demand for pickup trucks and fullsize SUVs, following the sharp rise in petroleum prices earlier in the year.
We then targeted variable costs, in particular temporary workers, cutting some 1,600 at Nissan Iberica (in Spain) and 1,200 each at Nissan Motor Mfg. (U.K.) and Nissan North America.
Imazu: Modular production to remain important Nissan strategy.
Finally, we froze many capital investments and switched to kaizen-oriented (continuous-improvement) activities inside our plants, what I call intelligent factory automation, or IFA.
While we saw earnings fall sharply in the third quarter, October through December 2008, and reported a huge fourth-quarter loss, we put in place the foundation for improved earnings which carried over into the current fiscal year beginning last April.
Ward’s: What is Nissan’s breakeven point in terms of capacity utilization of your plants?
Imazu: Somewhere between 60% and 70%. But note there are two aspects to breakeven: One is plant capacity; the second is headcount. Even before the Lehman shock, we had lowered headcount to meet long-term, 10-year market trends.
Ward’s: Even in Japan, where the market contracted 20% over the past five years and production in calendar 2009 plummeted by 30% from a near 16-year high the year before?
Imazu: Yes.
Ward’s: And in terms of production volume, what is Nissan’s breakeven?
Imazu: In Japan: around 1 million units; slightly less, in fact.
Ward’s: For a half-year period, Nissan would be profitable at less than 500,000 units?
Imazu: Yes. In fact, between July and December we produced more than 550,000 units and had to add workers to meet increased volumes. At Oppama, for instance, we added 150 temporary workers. But basically 1 million is a good number for us. We can operate profitably at that level.
Ward’s: Even for exports at a $1:¥90 exchange rate?
Nissan Plant Capacity in Japan
Plant | Unit Capacity | 2009 Volume* |
---|---|---|
Oppama | 425,000 | 255,120 |
Kyushu | 425,000 | 118,749 |
Hiratsuka** | 320,000 | 227,373 |
Tochigi | 210,000 | 205,466 |
Imazu: It varies by model. For instance, we have great price flexibility with our Infiniti lineup, whereas for B- and C-segment cars like the Tiida, Micra or Cube we are more vulnerable to the currency rates.
Ward’s: So, $1:¥90 is close to the point where Nissan can’t export from Japan?
Imazu: It’s not that simple, because there are countermeasures we can pursue including shifting production to low-cost countries or increasing component purchases from those same countries – or at least from countries in which exchange rates give advantage to imports.
For instance, we already shifted part of Tiida production to Nissan Mexicana from our Oppama plant in Japan. And we plan to build our all new V-platform cars in five countries outside Japan. On the components side, we have begun importing components for the new NV200 passenger van from China.
And this trend will continue – to source key components from China, Thailand or India – but with one caveat: We can’t make sourcing changes mid-cycle because that would mean double-tooling for our suppliers. Thus, we must wait, like we did with the NV200, for a full-model change or a new-model launch.
Ward’s: And you won’t import core components such as continuously variable transmissions from JATCO Ltd. in China or Mexico?
Imazu: No, no. Nor will we import other bulky parts such as seats or instrument panels, which need to be close to our assembly plants.
Ward’s: With respect to module production in general, an area Nissan has led by bringing suppliers inside its plants, can we expect further expansion of this operation?
Imazu: Module production, in the sense of suppliers coming into our plants, will remain an important feature of Nissan’s manufacturing strategy. And where possible, we will continue to invite suppliers into our plants, as we’ve done at Smyrna (TN) and Canton in the U.S. and Oppama, Tochigi and elsewhere in Japan. In fact, we have established a supplier park inside our new joint-venture plant with Renault (SA) in Chennai, India.
Among other things, having suppliers onsite helps us reduce inventories. Cost and productivity merits are indisputable.
(Despite proven productivity merits, purchasing chief Yasuhiro Yamauchi believes Nissan module makers, in particular Calsonic Kansei Corp., may not have the financial wherewithal to negotiate effectively with its suppliers. In the future, the auto maker may purchase components directly from the second-tier suppliers, while letting the module makers continue to handle assembly operations inside Nissan’s plants. In Japan, Calsonic Kansei makes front-end and cockpit modules at Nissan’s Tochigi, Oppama and Kyushu plants and the Hitatsuka plant of Nissan Shatai Co., an affiliated manufacturer.)
Ward’s: Speaking of the new Chennai plant, which begins operations this spring, have you installed the Nissan Integrated Manufacturing System, or NIMS?
Imazu: Yes, but at Chennai we call it ‘AIMS.’
Ward’s: Which is?
Imazu: Alliance Integrated Manufacturing System. Essentially it is the same concept as NIMS: a flexible manufacturing system which creates common assembly processes between plants and, in this case, between companies (Nissan and Renault) so that similar platforms can be shifted easily and cost-effectively. The system incorporates welding, painting and final assembly operations along with injection molding and stamping.
Ward’s: And deployment of this new AIMS process will begin in Chennai?
Imazu: Yes.
Ward’s: How many plants will incorporate AIMS?
Imazu: First India, then Morocco and finally China – specifically at Renault Nissan Automotive India’s new Chennai plant, Renault’s Tangier plant and Dongfeng-Renault ’s joint venture in Huada (China), although we haven’t finalized our Huada plans.
Ward’s: And you have no plans to introduce the system in Europe?
Imazu: Not at this time. If we establish a new joint-venture plant, yes.
Ward’s: With respect to NIMS, how many plants have adopted the system so far?
Imazu: I believe 25 lines at 17 plants in the U.S., Mexico, U.K. and Japan.
Related document: Nissan NIMS Installations
Ward’s: But all plants don’t have the same level of automation?
Imazu: That’s correct. Plants like Dongfeng’s Huada or Renault Nissan’s Chennai have far less automation than Smyrna, Canton and all of our domestic plants. Basically, the level of automation is a function of labor cost and depreciation and how we balance those two factors.
Ward’s: And the main advantage of both NIMS and AIMS is?
Imazu: It enables us to cut lead time and investment in half when launching new models.
Ward’s: Do you credit NIMS with your rapid turnaround last year?
Imazu: Certainly it was one of the major factors. We were able to respond to changing market conditions quickly and flexibly.
Ward’s: Any examples?
Imazu: We've made Thailand the base for our Navara pickup and added the Dualis, the Japanese version of the Qashqai, at our Kyushu plant.
Ward’s: As a general question, how long does it take Nissan to introduce a new model from design freeze to production?
Imazu: We’ve lowered lead time to 10.5 months. And ramp-up, in part because of our Global Production Engineering Center in Zama (Japan), is around four weeks. Basically, we can launch models simultaneously as we’re planning to do with the new V-platform model initially in India, China and Thailand.
Ward’s: Switching subjects, will the Leaf and other electric vehicles be built on the same assembly line with standard cars at your Oppama plant like you do with the Altima Hybrid at Nissan North America’s Smyrna plant?
Imazu: Yes. And like at Smyrna, we will have separate zones for battery and other EV component installation integrated into the main line.
Ward’s: With respect to the Leaf and Nissan’s battery technology, do you feel Japanese car makers, and particularly Japanese battery makers, are leading in the global EV race?
Imazu: Japanese car makers and suppliers are very strong in manufacturing and quality management. Our objective in battery production is to achieve “absolute” reliability. Nissan has been developing lithium-ion batteries for 17 years and I believe our technology is very advanced.
Ward’s: And this operation will be almost completely machine-run?
Imazu: But this isn’t only for quality purposes. If substantial manpower is needed to make batteries, we won’t be able to locate production facilities in high-cost countries and regions like Japan, the U.S. and Europe. For many reasons, not only quality, we feel it is necessary to locate battery production as close to Nissan’s vehicle plants as possible. Thus, automation is critical.
Ward’s: You are basically saying then that labor-intensive operations can’t meet the extremely high quality standards needed to produce lithium batteries?
Imazu: That’s right.
Ward’s: And according to your current business plan, it is Nissan’s intention to have capacity to produce about 500,000 Li-ion batteries by the end of 2012?
Imazu: Yes.
Ward’s: Who is assisting Nissan in manufacturing and engineering your battery?
Imazu: We have formed a team with NEC (Corp), NEC Tokin (Corp.) and several Nissan affiliates, plus equipment and facility suppliers.
Ward’s: Are there any names you can disclose?
Imazu: No, (not) of equipment and facility suppliers. But they’re not big companies.
Ward’s: Last year, due in part to the urgency surrounding the market downturn, Nissan achieved exceptional reductions in production cost. What is your normal rate of cost-cutting?
Imazu: It’s difficult to say, but I would say ballpark, 5%.
About the Author
You May Also Like