Smyrna Epicenter of Nissan’s Quest for QualitySmyrna Epicenter of Nissan’s Quest for Quality
A new quality auditing effort is helping inspectors double the number of vehicle flaws discovered.
June 27, 2006
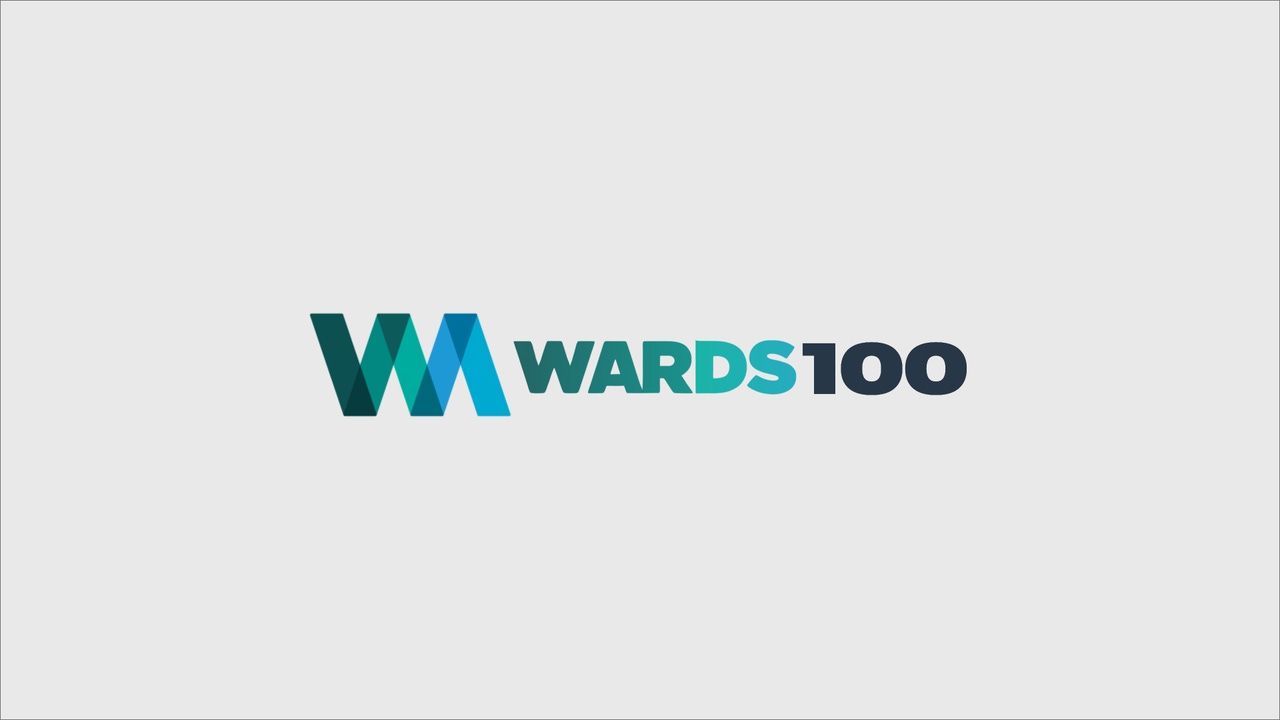
SMYRNA, TN – One important reason Nissan North America Inc. is moving its headquarters from Los Angeles to Franklin, TN, is to be closer to its largest and oldest U.S. production facility here.
Smyrna, the first plant to build the flagship Maxima outside of Japan, is Nissan Motor Co. Ltd.’s primary benchmark for North American production.
In many ways, it serves as a mentor facility to the auto maker’s 3-year-old Canton, MS, plant, which is on the rebound after scoring basement ratings in the J.D. Power & Associates 2003 Initial Quality Study. The plant since has remedied many of its earlier issues, Nissan says.
Smyrna builds about 1,000 Altima sedans a day and also produces the midsize Frontier pickup and midsize Xterra and Pathfinder SUVs.
Canton also builds the Altima, in addition to the Quest minivan, Titan fullsize pickup truck and Armada and Infiniti QX56 fullsize SUVs.
Engines produced at Decherd, TN, are funneled to Smyrna.
All three facilities are within a couple hours’ drive time of the new North America headquarters, located near Nashville and slated to open in 2008, with Smyrna being the closest.
New Nissan headquarters, seen in concept drawing, will be located within hours of production plants.
The proximity will aid Nissan’s quest for quality, officials say.
One new Smyrna initiative that likely will find its way to Nissan’s other production facilities, tentatively dubbed “best practice inspection,” is an attempt to better detect production flaws.
The process singles out one line from among five inspection lines to run a variety of up close and personal quality tests.
Overhead lighting has been tweaked to better catch flaws, while touch inspections identify inconsistencies in difficult to detect door-side moldings and other fittings, says Doug Betts, senior vice president-total customer satisfaction.
Betts likens traditional inspection methods to staring at computer-generated art, which at first glance resembles an abstract blur, but from a different angle appears to contain a specific image or design. The same can be true for quality inspectors, who stare at hundreds of vehicles a day.
The super sleuth effort appears to be paying off. When comparing the sequestered inspection line with the other four lines, Betts says auditors have discovered twice the number of defects.
Nissan likely will export the process to Canton, which is continuing to work through a 23-step “Built-In Quality” evaluation to examine what it can do to prevent production defects before vehicles get to showrooms.
The 13 customer-satisfaction teams executing the quality reviews focus on everything from braking to handling to squeaks and rattles. Nissan calls the teams “cross-functional,” meaning they include representatives from both the design and manufacturing sides.
“Without a cross-functional team, they’ve got to guess whether it’s a design problem or a manufacturing problem,” Betts says, noting the project’s timesaving advantage.
“Things that would take a month in a classic organization take 15 minutes,” he says.
Betts instituted a similar quality initiative during his tenure as general manager for quality at Toyota Motor Corp.’s Princeton, IN, plant.
As with Toyota, Nissan’s evaluation teams are trying to anticipate problems unique to U.S. driving conditions. “The (original) rulebook is made in Japan,” Betts says. “The (U.S.) market is different, and the driving conditions are different.”
With 5.4 million sq.-ft. (501,660 sq.-m) under one roof, Smyrna has a 50-50 car/truck output, while Canton is focused on 25% cars and 75% trucks.
As it reaches for more production flexibility to meet demands for both segments, Smyrna is expanding the use of kits, or pre-assembled modules or systems, that help ease assembly and improve quality.
“We want people focusing, and if you’ve got to walk around (for a part) and think and pick, it diminishes that,” says Greg Daniels, senior vice president-U.S. manufacturing. “(As a worker), I don’t have to think about it. I just pick it up.”
Another motivation for simplifying quality in assembly is Smyrna’s shifting workforce. Greater numbers of veteran employees reached retirement last year, giving way to younger and less-experienced line workers.
Daniels, who helped launch the Smyrna plant 24 years ago, says the staffing mix is prompting a new wave of training. The plant employs 5,183 hourly and 1,416 salaried workers.
Meanwhile, production at NNA’s three plants has slowed in recent months due to sagging sales. The auto maker announced in April it would cut six days of planned vehicle production from the year to lower inventory levels as it readies ’07 models for showrooms this summer.
Nissan estimates the change will cut about 18,000 vehicles from its annual production schedule.
The auto maker’s year-to-date light-vehicle sales in the U.S. fell 4.5% through May, according to Ward’s data. May sales dropped 7.3% compared with prior-year.
About the Author
You May Also Like