Automotive Industry’s Answer to Climate Regulation: MaterialsAutomotive Industry’s Answer to Climate Regulation: Materials
“Materials” is a vast term in the EV world. And with that, expect the focus on maximizing material science to remain a priority over the next several years.
October 18, 2021
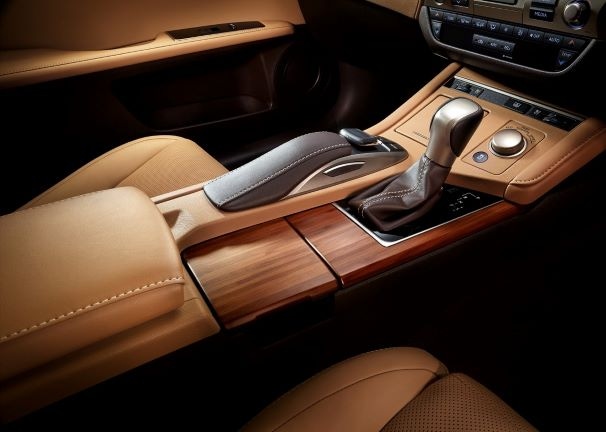
Ambitious climate goals are taking hold around the globe and are being welcomed on many fronts, including in the automotive sector. But with that, automakers also are having to quickly amp up their innovation and creativity so they can meet this new slate of ambitious climate targets.
Automakers naturally have begun to look at ways to boost EV range by way of improved motors and battery life. However, with many EVs available today still only offering between 200-250 miles (322-403 km) in range – with more budget-friendly models offering even less – there is still a huge amount of work to do to boost range in a way that is comparable to that of internal-combustion-engine vehicles.
And with that, many automakers are looking for ways to bridge the gap between the modest ranges of today and the longer ranges of tomorrow.
The answer is beginning to become clearer: materials.
From material science to the ways automakers use materials in vehicles, each component is going to be incredibly important in creating a more efficient vehicle. Here are a few ways that automakers can – and in some cases already are – leaning more heavily on material innovation to help them lay the groundwork for the vehicles of tomorrow.
The Fight for Lightweighting
The good news about the lightweighting revolution is that it already has been under way, at least somewhat earnestly, over the past decade and into the early 2000s. This has resulted in many sleepless nights for auto engineers but has resulted in innovative breakthroughs in terms of new uses such as aluminum, carbon fiber and new-age steel and other innovative building materials.
At the same time, as regulations and consumer preferences change, automakers are having to push the boat out even farther in their search for the next lightweight revolution. To meet this demand, engineers are leaving no stone unturned, from research into recycled plastics to automakers such as Lexus trading in traditional hardwood for the much more earth-friendly bamboo to make vehicles lighter. And this is only the tip of the iceberg, with new composites and plastics alternatives being ideated each day.
Rethinking Glass
From panoramic sunroofs to headrest TVs, arguably no component has been more visible in auto design or performance over the past decade than glass. That said, despite the growing appetite for more glass in vehicles, designers and engineers are still a bit hesitant when it comes to how and when they integrate glass into vehicles due to fears of overheating and glare.
Fortunately, as with other materials there have been significant gains made in the glass field, making glass not just a more viable design option but also a massive asset in improving vehicle efficiency.
For example, through advances in glass material science OEMs can now keep internal temperatures much more moderate. This results not only in a more comfortable and safer interior for occupants but also can reduce the need for air-conditioning use, resulting in EVs being able to allocate more “battery juice” toward actually driving the vehicle, thus extending its range.
Rare Earth Management
Just because EVs present a way for us to move away from fossil fuels, it does not mean they do not create issues for natural resources in other ways. EV batteries are heavily reliant on rare earth materials including cobalt, nickel, copper and many others. We already are seeing delays in accessing and sourcing these materials, bogging down progress in the EV space.
Therefore, we need to get creative in the ways that we can source these. It is not uncommon for fuel cells to meet production standards. But unfortunately, for years it was highly challenging for automakers to recover the materials that were in these rejected fuel cells, meaning if the unit was faulty a good amount of the materials in it would be wasted.
Joe_Harary (002)_0
However, innovations in recovering and recycling rare earth materials from rejected power units – for example, advances in pyrometallurgy and hydrometallurgy have made it possible to recover up to 98% of nickel, cobalt, graphite and other rare materials from rejected cells – enable automakers to replenish their reserves much more readily, furthering battery technology development and EV production.“Materials” is a vast term in the EV world. And with that, expect the focus on maximizing material science to remain a priority over the next several years. If we can get material science and management right, we not only will be able to make incredible short-term gains in the EV space but will begin to tackle the challenges of the future of the automotive space as well.
Joseph M. Harary (pictured above, left) is CEO of Research Frontiers, a publicly traded technology company and the developer of patented SPD-Smart light-control film technology.
About the Author
You May Also Like