Carbon Fiber Production Simple But Complex
The physical footprint of manufacturing lines is small. However, the carbon-fiber precursor material is delicate and must be handled with care and precision.
May 19, 2014
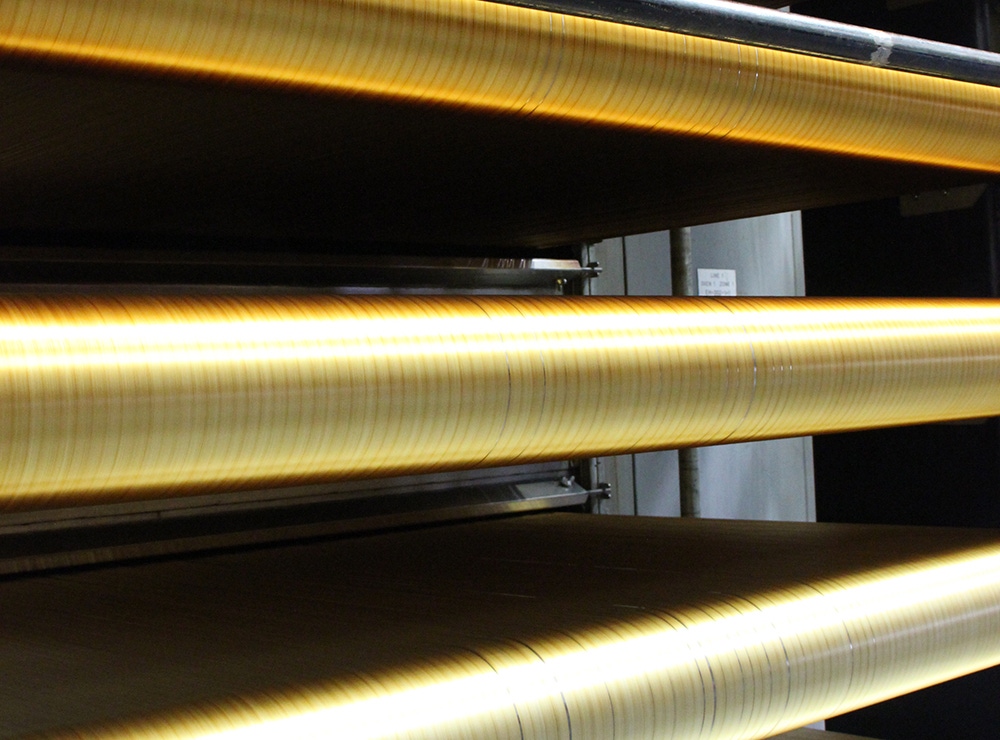
MOSES LAKE, WA – There are many steps needed for BMW’s i electrified vehicles to come to life, but perhaps the most critical, and talked-about one, happens here.
In this small town along the Columbia River three hours east of Seattle, BMW joint-venture partner SGL turns a stringy white plastic ribbon made of polyacrylonitrile, or PAN for short, into carbon fiber.
While it once was used only in race cars and ultra-expensive performance cars as a structural material, BMW is using rigid, but lightweight carbon fiber for major structural parts in its new family of electrified cars.
The i3 electric hatchback and i8 plug-in-hybrid sports car have passenger cabins, or lifecells in BMW-speak, made of carbon-fiber-reinforced plastics, which help offset the weight of the cars’ lithium-ion batteries.
The process BMW and SGL have created to make carbon fiber out of PAN is by turns simple and complex. The physical footprint of lines No.1 and No.2 at Moses Lake is small, with relatively few machines compared with other auto-parts manufacturing facilities. However, the material is delicate and must be handled with care and precision.
Paul Bolden, head of production at SGL Automotive Carbon Fiber in Moses Lake, recently gave media a guided tour of the facility, already undergoing an expansion.
In the first section of building No.1, ribbons of PAN, made at an SGL JV with Mitsubishi Rayon in Otake, Japan, are drawn up out of cardboard boxes onto creels and separated into fine strands in a humidity-controlled environment.
After separation, the PAN, chemically C3H3N, enters the second portion of the plant, where oxidation ovens live.
“There are four ovens per line,” Bolden says. “What’s happening in the oxidization (process) is stabilizing the material (for carbonization).”
Stabilization occurs by adding oxygen to the PAN, a 90-minute process performed at temperatures between 392° F and 500° F (200° C and 260° C). Once oxidized, the material cannot melt and is nonflammable. During oxidation the PAN changes color from white to shades of gold, then finally to black.
“We have a very defined process recipe, with time, temperature and speed that produces a very high-quality carbon fiber,” Steve Swanson, SGL plant manager, says in a production-process video.
After the PAN exits the fourth oven it is oxidized and stabilized, Bolden says. The material then makes a quick trip through low-temperature and high-temperature furnaces for the carbonization process.
Bolden says carbonization aligns the filaments with tension and heat, with furnace temperatures ranging from 392° F to 2,552° F (1,400° C).
After the material exits the high-temperature furnace it is 95% carbon and “we can refer to it as carbon fiber,” Bolden says.
A chemical then etches the outer surface of the carbon fiber so it can bond with resin, which is applied after in a later fabric-making process at SGL’s sister plant in Wackersdorf, Germany.
Winding Process Secret Ingredient
The carbon fiber then is sized and dried before it is spooled onto bobbins in a winding process, using what Bolden says is proprietary equipment.
The secretive nature of the equipment may be due to the fact twisted or folded carbon fiber would result in short lengths rather than long continuous pieces needed to bring the i model’s lifecells to fruition.
Some 1.7 miles (2.7 km) of carbon fiber are on each 20-lb. (9-kg) spool, which are individually wrapped, then placed with other spools in cardboard boxes that are shipped to Wackersdorf. It stitches the carbon fiber into a fabric, then cuts it into sheets that are then impregnated with resin.
These carbon-fiber-reinforced plastic sheets then go on to BMW plants in Landshut and Leipzig, Germany, where they are fabricated into 3-dimensional lifecells.
The weight of the resulting carbon fiber is 50% less than that of the PAN at the start of the process, SGL says, noting each strand of carbon fiber on a spool has 50,000 filaments, each approximately one-seventh the thickness of a human hair.
SGL has had two lines up and running here since September 2011, employing 80 workers. The second facility is weeks away from coming online, housing lines three and four. SGL announced last week it soon will begin construction on a third building set to open in early 2015 with lines five and six. At that point the complex will employ 200 workers.
Annual output of the two lines in each building is 3,000 tons (2,722 t). Lines 1 and 2 have been operating 24 hours per day, seven days a week, with downtime only for cleaning and repairs, Bolden says.
BMW says the addition of the fifth and sixth lines will support the proliferation of carbon fiber into additional models. The automaker is short on specifics for now, but suggests reports the next-generation 7-Series will utilize carbon-fiber parts are accurate.
A senior BMW official also tells WardsAuto the automaker would be willing to sell carbon fiber to other automakers, providing it has excess capacity. For now, BMW intends to use all 9,000 tons (8,165 t) of carbon fiber from Moses Lake for its own vehicles.
You May Also Like