Mass-Produced Carbon Fiber Around the Corner
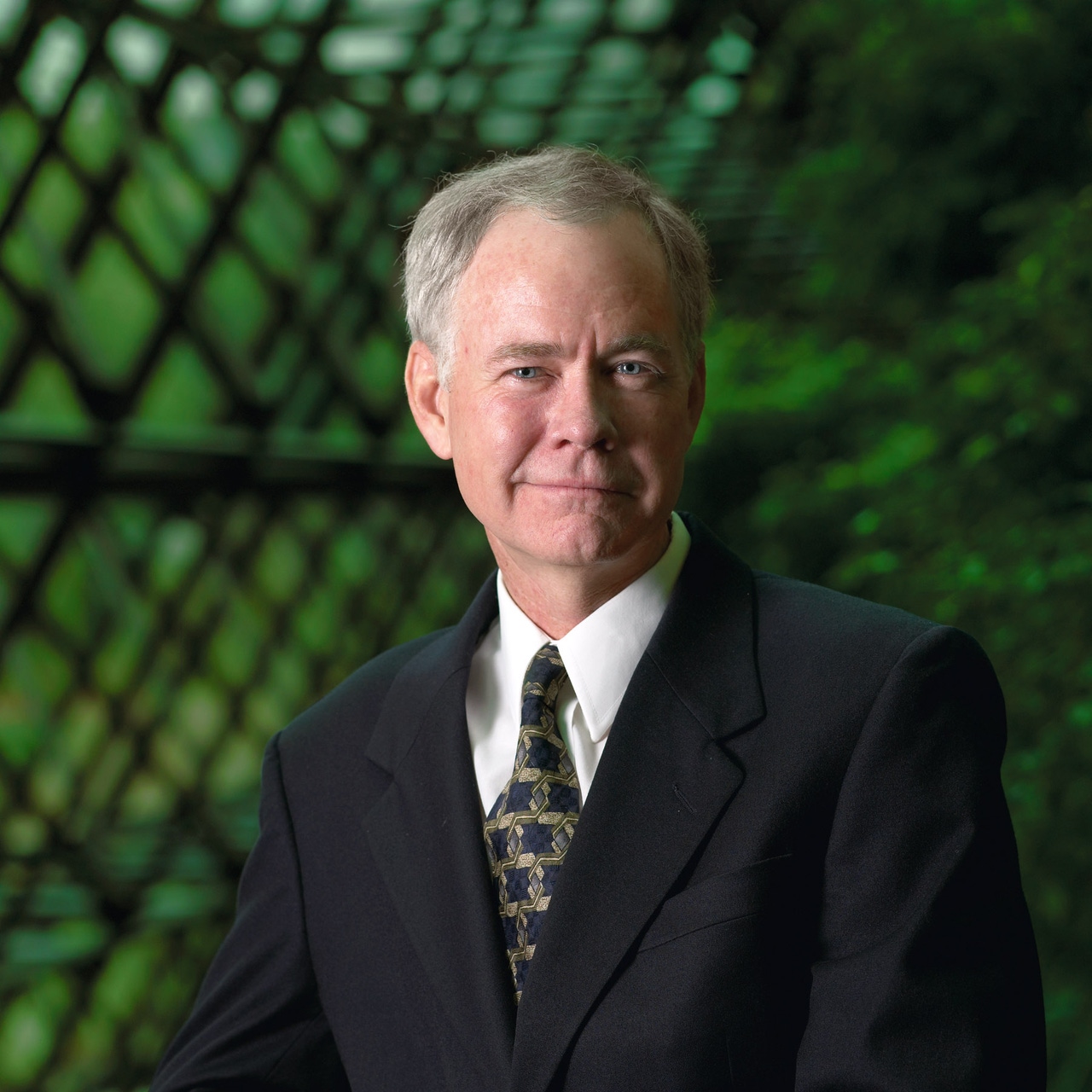
Race cars, exotic sports cars and aftermarket performance parts have been made from carbon fiber for years. But the super-light material is just too expensive to use in high-volume production. That soon could change. Auto makers are closing in on how to use it in mass production within the next five years.
Recently, a combination of raw material and process improvements have opened the door to using carbon fiber on everything from compact cars to pickup trucks. And this is coming just in time for auto makers to boost their average fuel economy to 54.5 mpg (4.3 L/100 km) by 2025.
Today the cycle time needed to mold a vehicle hood in an autoclave is 90 minutes, completely unacceptable for mass production. But molders have come up with an induction process using infrared heat, which eliminates the autoclave and cuts cycle times to only 17 minutes. That can boost volumes from 3,000 cars a year to 50,000, a big step forward.
Another production bottleneck is being eliminated by using robots instead of people to cut and place carbon fiber in molds and load and unload molding machines.
Researchers also are attacking the cost of the raw material itself. Presently, auto makers mostly use aerospace-grade carbon fiber called polyacrylonitrile. It greatly exceeds the engineering requirements auto makers need. At roughly $15 per lb. (0.45 k), it also is prohibitively expensive compared with steel, which is less than $0.40 per lb.
The Oak Ridge National Laboratory is experimenting with less-expensive materials such as polyethylene plastic and lignin, which offers the intriguing possibility of making carbon fiber from bio-mass.
Raw material suppliers are working on new resins that flow faster and at lower temperatures which could lead to cycle times of only five to seven minutes. But the goal is to get to just one or two minutes.
Oak Ridge also is developing computer-aided tools for engineers to predict how their carbon-fiber designs will perform. Other research efforts include the U.S. Council on Automotive Research, which is delving into how to make cost-effective floorpans and frame rails.
Designers and engineers will play a critical role in using carbon-fiber components for mass production. That’s because structural components will need to withstand the electro-coat and 400º F (204° C) bake ovens in assembly plants.
Structural adhesives will have to replace welding operations, and there won’t be any “metal finishing” to smooth out blemishes. The point is, you can’t just start using these pieces in a car without thinking through the entire manufacturing process.
And the race is on to lock in a supply source. Toyota, Daimler, Subaru and Nissan have agreements with the Japanese company Toray, the largest carbon-fiber supplier in the world.
Ford is teaming up with U.S.-based Dow, while General Motors signed up with Teijin, another Japanese company. BMW formed a joint venture with the German supplier SGL. BMW claims it will be the first major auto maker to sell an all-carbon-fiber car, its electric i3.
Volkswagen also bought part of SGL, which forced BMW to rush in and buy a larger share in the company simply to prevent VW from gaining any more control.
Susanne Klatten, a member of the Quandt family and the heiress to the BMW empire, owns another big chunk of SGL. VW may want to find another source quickly. New suppliers from China and South Korea are emerging, but there are few other large-scale vendors out there.
And no one wants to be left out. After 2015, carbon-fiber applications in the automotive industry are projected to grow 10% to 15% annually. It could become one of the greatest growth segments in the automotive industry in the second half of this decade.
John McElroy is editorial director of Blue Sky Productions and producer of “Autoline” for WTVS-Channel 56, Detroit, and “Autoline Daily,” the online video newscast.
About the Author
You May Also Like