Metaverse Production System Saving Millions for Renault
Renault’s Metaverse is designed to reduce vehicle delivery time 60% and halve the carbon footprint of the automaker’s vehicle manufacturing, as well as significantly reduce innovation cycles.
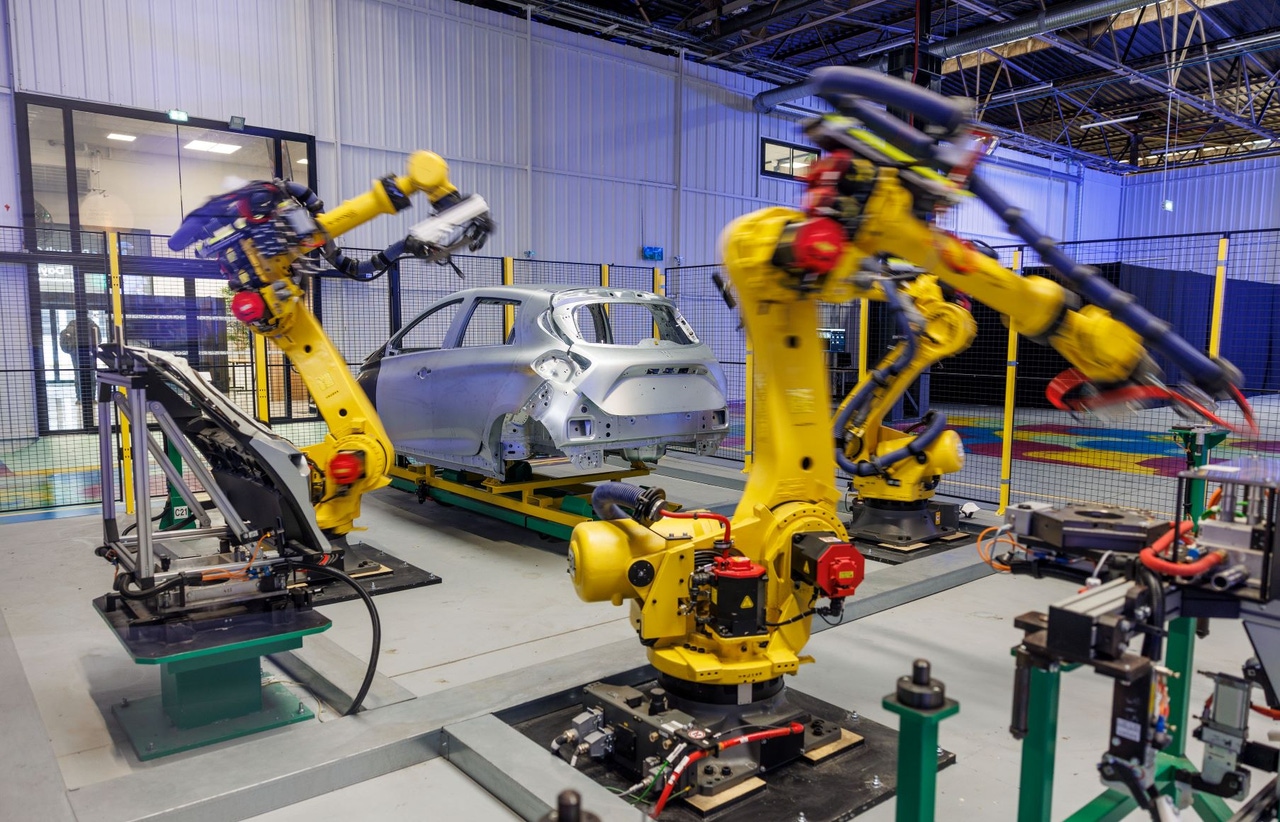
French automaker Renault claims to have created the world’s first industrial Metaverse designed to advance the production savings of its digitalized factories.
From this week all of Renault’s vehicle production lines are connected, a total of 8,500 pieces of equipment, and 90% of supply flows are constantly monitored with all supply-chain data hosted in its Metaverse, a digital twin of its entire production system controlled in real time. The task of digitalizing its production process began in 2016 and already has led to savings of €780 million ($805 million). By 2025, the automaker claims savings will rise by another €320 million ($330 million), which will be added to €260 million ($268 million) in savings on inventory.
This also will see a 60% reduction in vehicle delivery time and a 50% reduction in the carbon footprint of Renault’s vehicle manufacturing, as well as a significant reduction in innovation cycles and a contribution to the 60% reduction in warranty costs targeted by the Renault Group.
Renault says its Metaverse starts with data collection. It claims to have developed a unique data platform to collect mass data in real time. This solution is being marketed in partnership with ATOS to other industrial players under the name of the ID@Scale project.
Then digital twins of each of its factories have been created in the virtual world. Like the factories, the supply chain has its own digitized universe and is also controlled in real time by a control tower. The use of digital twins is enriched not only with supplier data, sales forecasts and quality information but also other relevant information such as the weather or road traffic, etc., as well as artificial intelligence allowing the development of predictive scenarios.
The automaker claims its Metaverse offers improved visibility of the work environment allowing decision-makers to gain agility and autonomy in their actions. Technologies from the world of gaming also help make user experiences more immersive. This is the case of painting training carried out in virtual reality. AI algorithms allow employees to anticipate, as do flow optimization and management functions for supply-chain experts.
Patrice Haettel, Renault vice president for industrial strategy and engineering, says: “This industrial Metaverse is unique and enables us to activate previously invisible efficiency and performance levers, to the benefit of people and the environment. The management of data at Group level allows us to monitor, for example, the energy consumption of all our industrial and non-industrial sites in detail, and above all to optimize them in real time when a plant is stopped.”
About the Author
You May Also Like