Cutting Out the MiddlemanCutting Out the Middleman
Composite Products Inc. (CPI) says it has developed a composite manufacturing process that allows it to sell its composite parts for 30% to 60% less than competitors that use the traditional composite material supply procedure. CPI's direct-feed thermoplastic (DFT) manufacturing process allows the Winona, MN-based composite molder to avoid buying composite pellets from a compounding company. The way
March 1, 2002
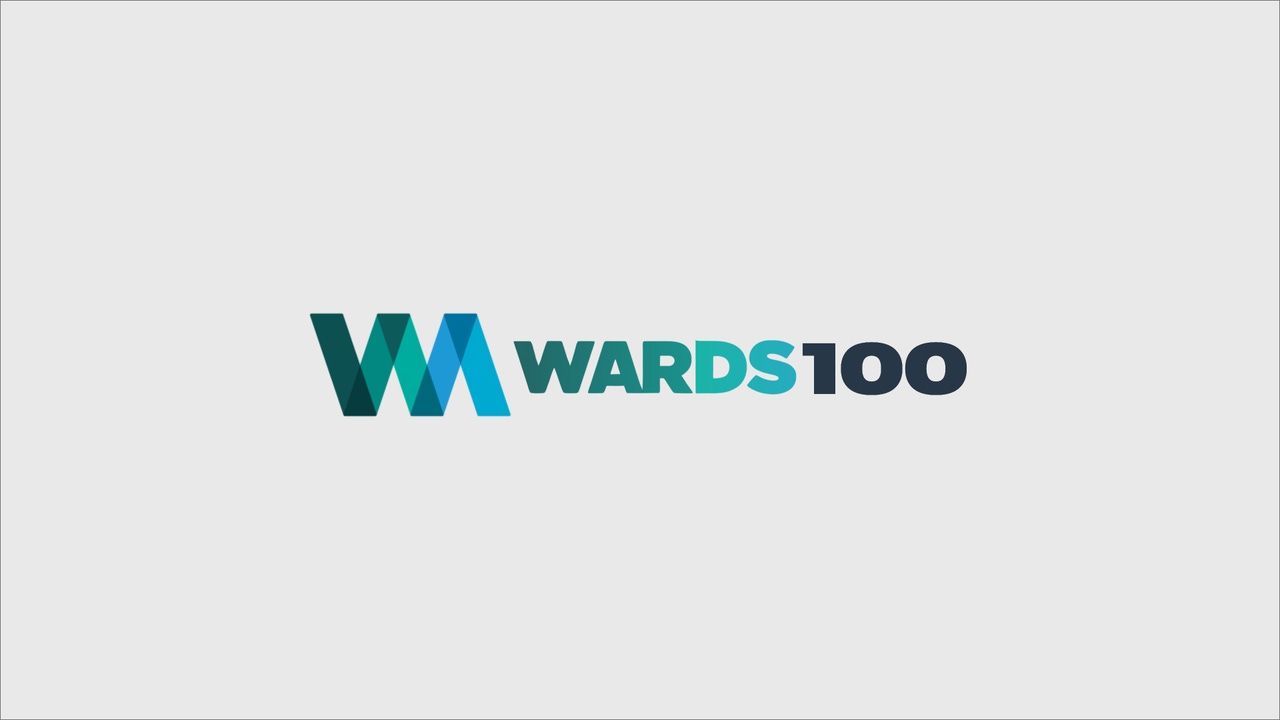
Composite Products Inc. (CPI) says it has developed a composite manufacturing process that allows it to sell its composite parts for 30% to 60% less than competitors that use the traditional composite material supply procedure.
CPI's direct-feed thermoplastic (DFT) manufacturing process allows the Winona, MN-based composite molder to avoid buying composite pellets from a compounding company. “The way we do that is by doing the compounding in line with the molding,” explains John Busch, CPI's director of business development. “It allows us to use the rawest and least expensive materials, and we cut out a middleman.”
CPI buys chopped glass in bulk from large fiberglass suppliers and mass purchases resin pellets, typically polypropylene, nylon or polyester, directly from one of the large plastics suppliers. Alternative long fiber thermoplastic (LFT) materials are sold as pre-compounded pellets or sheet. A separate compounding business is involved in their preparation. The compounder sells LFT pellets or sheet to a molder, which converts these materials into molded parts.
With CPI's process, called Advantage, the roles of the compounder and molder are combined. “Cutting out the middleman not only means we've cut out the compounder, but all the sales and marketing, packaging and shipping and inventory management,” Busch notes. “It's all been erased from the economic equation.”
CPI's Advantage process' first automotive application was the front-end module for Volvo Cars' S70/V70. The auto maker was able to combine four metal parts into one reinforced thermoplastic front-end module using CPI's technology.
Advantage features four major functions and pieces of equipment. Gravimetric feeder devices output a constant number of pounds of material per hour, Busch explains. For example, to produce 1,000 lbs. (454 kg) per hour of a 40% glass fiber reinforced polypropylene composite, one feeder is set to output 400 lbs. (182 kg) per hour of glass, the other feeder is set to output 600 lbs. (272 kg) per hour of polypropylene.
The melt extruder blends the resin and additives, if required. Busch says common additives include ultraviolet stabilizers, colorants, and coupling agents. The output of the melt extruder is a homogenous, low viscosity mixture of molten resin and additives.
The compounding extruder preheats the reinforcing fibers — bringing them from room temperature up to the temperature of the molten resin — and gently mixes the output of the melt extruder with the preheated reinforcing fibers, says Busch. The output of the compounding extruder is the LFT material. The accumulator stores the composite mixture between molding cycles.
You May Also Like