Expanding the Lap of Luxury Suppliers have leather for every purpose - andpurse
Say goodbye to the notion that leather upholstery is only for top-end luxury cars. The popularity of light trucks, leasing and changing buyer tastes is sending leather into interiors where it has seldom gone before. Pickup trucks, minivans, economy cars - and of course sport/utility vehicles (SUVs) - are swallowing up yards of the stuff like never before.In response to this broader usage, suppliers
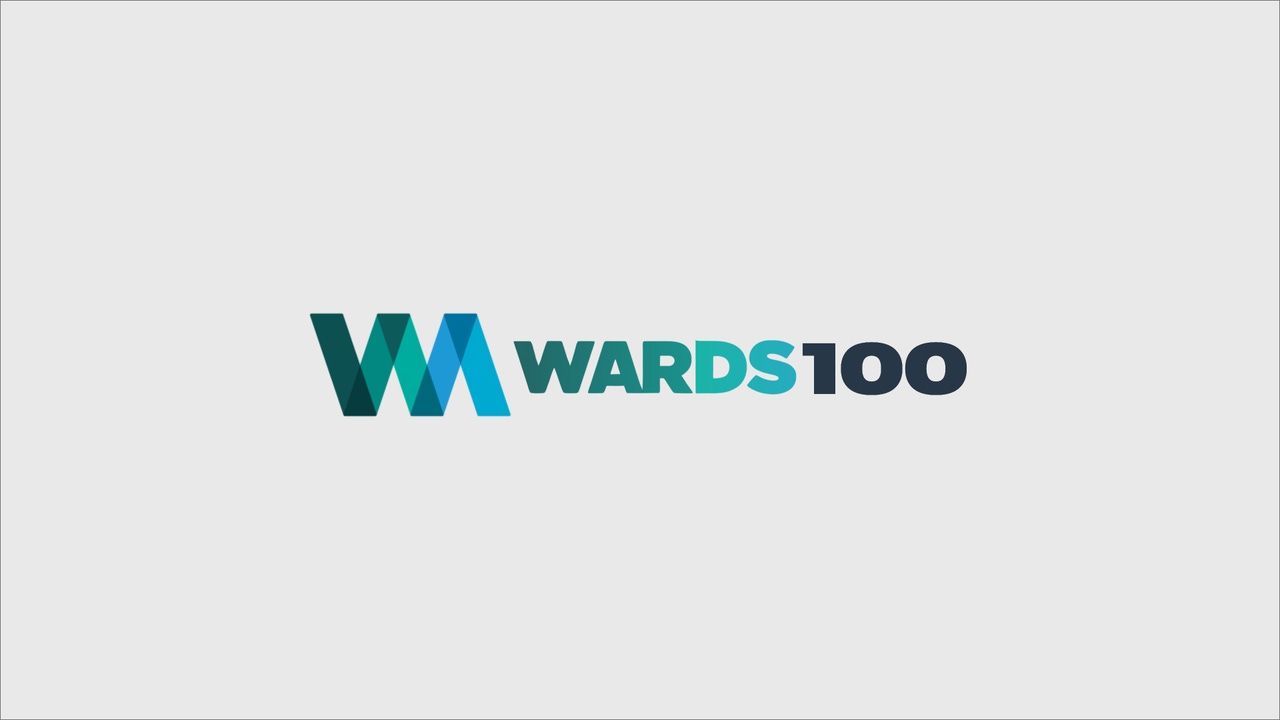
Say goodbye to the notion that leather upholstery is only for top-end luxury cars. The popularity of light trucks, leasing and changing buyer tastes is sending leather into interiors where it has seldom gone before. Pickup trucks, minivans, economy cars - and of course sport/utility vehicles (SUVs) - are swallowing up yards of the stuff like never before.
In response to this broader usage, suppliers are creating a greater variety of leather textures, finishes and colors than ever so they can better match a particular vehicle's personality and brand character. If they aren't available already, watch for rough-and-ready saddle-like leather finishes for SUVs, "naked" grades inspired by 16th century artisans and new high-tech designer patterns aimed at creating new interior aesthetics.
The legendary Alfred P. Sloan Jr. of General Motors Corp. coined the phrase "a car for every purse and purpose." Leather suppliers now appear to be making a type of leather for every purpose, and purse, too, so to speak.
"We have a crack design team in a studio in Florence, Italy, that studies home furnishings and watches for new trends and social themes," says Jeffrey R. Bonello, global marketing manager at Eagle Ottawa Leather Co., a major automotive leather supplier. One of the latest developments is more environmentally friendly leather processing techniques that eliminate the use of solvents and chromium, he says.
Eagle Ottawa supplies leather for about 80 vehicle models worldwide, including every major vehicle manufacturer in the U.S., Europe and Japan. Its Phoenix leather is the first of its kind to be tanned and treated completely with natural fruit extracts instead of chrome or other metals, Mr. Bonello says. It's available on the '98 Volkswagen Passat.
This new leather bonanza also appears to be driving changes in the leather supply community. For instance, the Ervins Group, a minority-owned supplier of interior trim components, has signed a joint venture with Connolly North America LLC, a division of Connolly Leather in Britain. The new company, Ervins/Connolly LLC, will produce cut leather for seats and interior trim for the 1999 Lincoln Continental, 1999 Pontiac Bonneville and a future redesign of the Ford Thunderbird.
The deal could even lead to a new headquarters in Detroit, company officials say.
Ward's Automotive Reports data shows 58% of '97 model Ford Expeditions were ordered with leather seats, as well as one in every four Chevy and GMC Suburbans. With their huge interior expanses and large bench seats, they easily use up as many leather hides as two or three cars. But even more surprisingly, leather interiors are being ordered on lots of lower-priced vehicles not synonymous with luxury. Orders for leather seats on GM's C/K 1500 full-size pickups doubled from the '96 to the '97 model year, to more than 8%. Leather wasn't even available on '96 model Ford F-150 pickups, but in '97, more than 9% (of 710,000 trucks) were ordered with the option.
An impressive 70% of Chrysler Corp.'s luxurious Town and Country minivans are ordered with leather, and 45% of Oldsmobile's Silhouette people movers.
Even relatively inexpensive cars such as the Ford Contour, Geo Prizm and Mercury Tracer now can be ordered with leather interiors.
The popularity of leasing, which makes pricier options such as leather interiors more affordable, certainly is a factor. Consumers also are increasingly concerned with residual values on lease cars and resale values of new cars. Leather usually props up both.
Eagle Ottawa's Mr. Bonello suggests many consumers are opting for leather because it is very durable and easier to clean and care for than most fabric interiors - in an era when vinyl upholstery no longer is available on most models. In essence, it's becoming sort of a rich man's vinyl to some.
Baby boomers' need to be coddled and Generation Xers' attraction to natural materials is another. "People have been surrounded by plastic all their lives," Mr. Bonello says, adding that drivers logging more and more hours commuting and sitting in traffic also add to leather's appeal.
Automakers like leather because it's a high-profit option and also because it provides a means of lending a sense of hand-worked craftsmanship to otherwise sterile, ho-hum interiors. New embossing and printing techniques, as well as a greater variety of colors and aromas, will provide automakers even more design options in the future.
"The biggest trend is going to be more leather with alternative textures and finishes, says Mr. Bonello. "There's a lot of interest in non-animal grain, technical-type looks, knurled, repetitive patterns, and designs that look a little different. We're also seeing some interest in alternative preparations and finishes, multi-colored finishes, even pearlescent looks."
Vehicle interiors are dominated by just two major plastic materials groups in the U.S.: polypropylene (PP) and acrylonitrile butadiene styrene (ABS), and they seem perpetually locked in a life-and-death struggle for market share. But lately a new, lightweight material has been making significant marketplace and technological gains.
Called low-density structural reaction-injection molded polyurethane (LD-SRIM), it is low-cost, very lightweight and it has won several dozen new applications during recent model years. The most significant is likely the interior door panels of General Motors Corp.'s new '99 GMT800 full-size pickups coming this fall.
Use of LD-SRIM materials for interior trim panels measured in pounds consumed in North American vehicles has been growing 10% to 20% annually, winning applications on 20 or more major vehicle programs through the '98 model year. In 1990, the material wasn't even used in the auto industry.
LD-SRIM got its foot in the door, so to speak, with door panels on heavy American luxury cars. Its ability to chop weight 40% to 60% won it applications for door panel substrates on GM's Oldsmobile 88 and the beefy Aurora/Riviera in the early '90s. Applications on other tubby models such as Ford Motor Co.'s Lincoln Town Car and Continental followed.
These successful applications, coupled with the material's low tooling costs, have led OEM engineers to specify LD-SRIM for numerous other interior trim substrates, including package trays, seat backs, sunshades and sun visors.
LD-SRIM also has expanded out of the luxury car niche and is being used for door panels on high-volume, mainstream vehicles. Besides GMT800 pickups, the list includes Chrysler Corp.'s LHS and GM's Astro/Safari minivans.
Major suppliers such as ICI Polyurethanes, Bayer Corp. and Dow Chemical Co. hope new processing technology will give the material another boost.
Conventional LD-SRIM parts are made by placing a continuous-strand glass fiber mat into a mold and then injecting two reactive polyurethane liquids. In a chemical reaction, the two polyurethane components harden into a foam that encapsulates the glass mat, resulting in a glass-reinforced structural composite.
Unlike thermoplastics or wood-fiber composites used to make interior trim panel substrates, the structural RIM process has the capability of yielding parts in a wide range of densities and physical properties, producers say.
By varying the density of the foam, the glass content and the thickness, a design engineer can create everything from a featherweight door panel to a tough, stiff structural part such as a bumper beam.
Now new processing technologies are being developed that promise to create even more opportunities for LD-SRIM. Essentially, the new technology chops and shoots glass fibers into the polyurethane stream as thepolymer exits the mixhead, eliminating all the cost and manufacturing steps required for glass mats.
The major benefit is cost reduction without reducing the structural RIM's physical properties. By eliminating the glass mat, the technology eliminates the manual labor required to insert and trim the mat, says Bill Worms, manager-advanced technology, sales and marketing at Hennecke Machinery. Spools of glass fibers are much less expensive than glass mat. The new process also significantly reduces waste and material inventory space.
Bayer's technology, called FipurTec, was developed by Hennecke GmbH and is being marketed in the U.S. by Hennecke Machinery, a unit of Bayer Corp.'s Polymers Div., a major polyurethane chemical supplier. ICI is using a similar technology it calls the long-fiber injection (LFI) process. It uses machines built by Krauss-Maffei.
Each process eliminates the need for a fiberglass mat in the molding process, promising significant cost savings and creates opportunities to use SRIM in new applications. Andreas H. Rothacker, a senior development specialist at ICI Polyurethanes, says applications for the process include door panels, package trays, quarter panels, seat pans/backs, spare tire covers and sun visors. "The technology is well-suited for any application where a strong, durable, lightweight substrate is required," he says.
Read more about:
1998About the Author
You May Also Like