ISI Looks Beyond Traditional Tier Structure with New GasketISI Looks Beyond Traditional Tier Structure with New Gasket
In January, Tier-2 supplier ISI launched a sister Tier-1 business named Interface Sealing Solutions aimed at getting involved earlier in the design cycle with key auto maker customers.
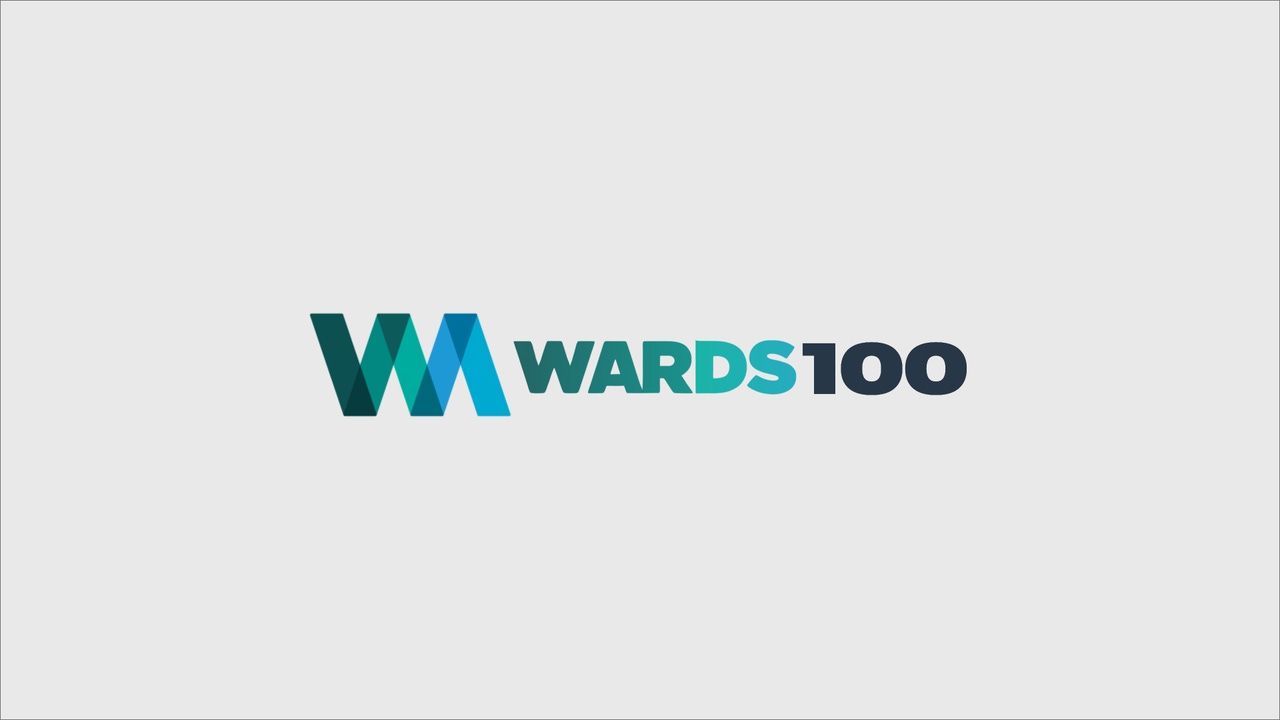
The secondary gasket market is not the first place you would look for supplier innovation, but the folks at Interface Solutions Inc. definitely are thinking outside the box.
Or, in this case, the Lancaster, PA-based supplier of gaskets for oil pans, water pumps, axles and other parts is thinking outside the highly stratified tier structure of the automotive supply base.
In January, the Tier-2 supplier of secondary gaskets (as opposed to “primary” head and exhaust gaskets) launched a sister Tier-1 business named Interface Sealing Solutions aimed at getting involved earlier in the design cycle with key auto maker customers.
Company officials say parent ISI has a long and successful history as a Tier 2 supplier, selling products to Tier 1s such as American Axle & Mfg. and Eaton Corp., and it has no interest in changing its overall status in the supply chain.
However, Louis D’Annibale, ISS executive vice president-sales and marketing, says the customizable nature of its Select-a-Seal Gen II gasket makes it necessary to create a new business with a more direct relationship with auto maker customers.
“As a Tier 2 we were sort of handcuffed in our ability to interact with the OEMs from a design standpoint,” D’Annibale says.
“The typical Tier-2 interaction is you get the ‘fix-it’ opportunities. You get a chance after things have been designed-in to either reduce cost or find some opportunity to correct a problem. Being a Tier 1 gives us an opportunity to have a seat at the design table,” D’Annibale says.
ISS can develop prototype gasket from scratch in two weeks.
A lot of gasketing solutions in the automotive industry are 10 years old, and some are 30 to 40 years old, D’Annibale says.
The new ISS is looking to shake up the status quo with new technologies such as the rubber-edged composite Select-a-Seal Gen II gasket, which is designed to compete with lower-performance fiber-based gaskets and high-performance (but more expensive) metal gaskets.
ISS’ polymer-based technology enables the supplier to use a standard gasket “structural carrier” that basically functions like a vehicle platform: It can be customized for many different applications with various specifically engineered polymers and edge geometries.
Depending on the application, several different polymers can be applied to different apertures of a single gasket.
The concept uses different types of polymers bonded to the critical edges of the fiber-reinforced structural carrier to provide a 3-part barrier against leaks. The polymer edges are formed into different profiles to serve various needs.
With this composite technology, ISS can develop a prototype gasket from scratch in as little as two weeks, and production tooling is relatively inexpensive. Comparable metal gaskets take much more time to develop, and production tooling can cost 10 to 20 times as much, D’Annibale says.
“We want to continue to be innovative in the development of technologies for the sealing market. To do that, you really have to have direct interaction with the OEM,” he adds.
In addition to being customizable and having fast development times, Select-a-Seal Gen II also touts stable bolt load retention at higher temperatures.
One major auto maker customer in particular equates bolt load retention stability with gasket durability, so ISS designed the second-generation product with this in mind. That enables the new Select-a-Seal to deliver the performance of a more expensive metal gasket at a lower cost, D’Annibale says.
ISS is launching first in the U.S., but it intends to take the Tier 1 concept to China and Europe as well.
Read more about:
2007About the Author
You May Also Like