Japanese Auto Industry Driving Toward RecoveryJapanese Auto Industry Driving Toward Recovery
Working around the clock, most auto makers and Tier 1 suppliers will be up and running at half capacity by the middle of April, just one month after the devastating March 11 earthquake and tsunami.
April 8, 2011
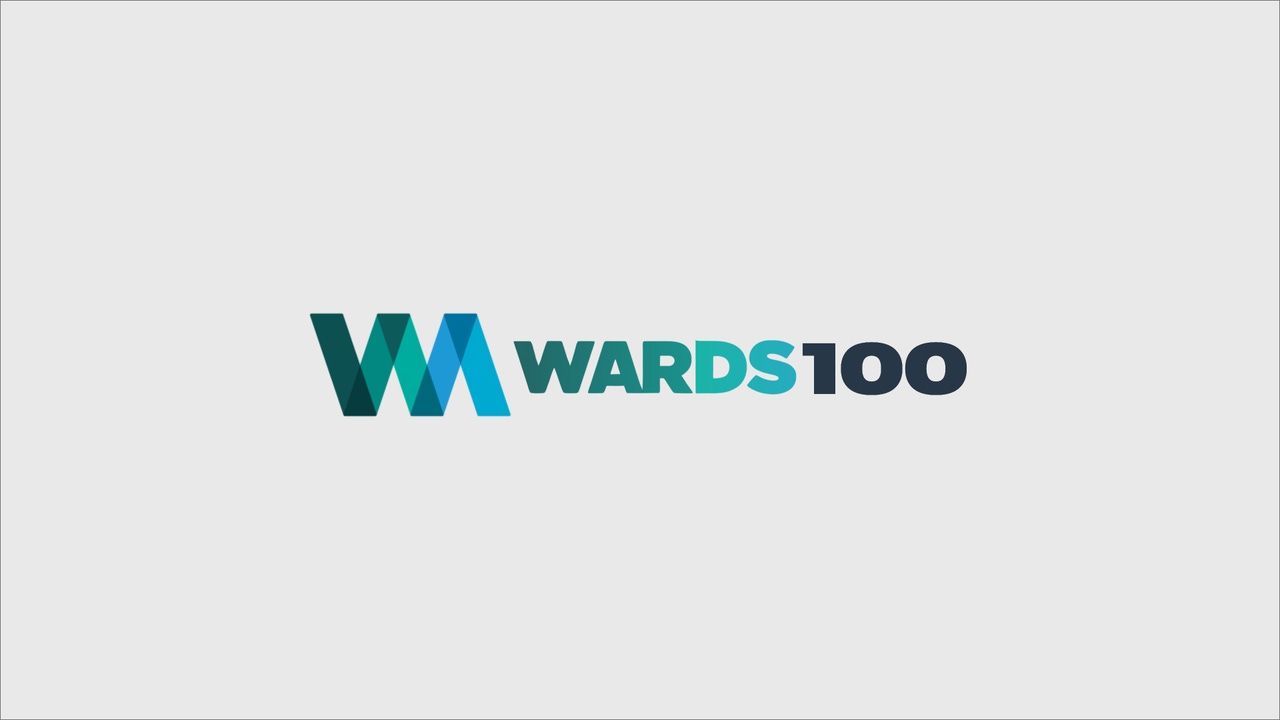
Japanese auto makers and their suppliers are quietly engineering one of the most dramatic recoveries in the history of the industry after two massive natural disasters have shaken them to their very foundation.
Working around the clock, most of the nation’s auto makers will be up and running at half capacity by the middle of April one month after a deadly earthquake and tsunami inflicted an estimated $300 billion in damage along 350 miles (563 km) of Japan’s northeastern coastline and brought the industry to a shuddering halt. And so will most of their suppliers.
Central Motor’s Ohira plant.
When full automotive production will be restored still is unknown. But the consensus among analysts is it will take six months. It may be longer, but could be shorter depending on supply- chain problems in the materials sector, especially resins, solvents and various additives, all centered in northern and northeastern Japan.
“Their progress to date has been faster than expected," Kohei Takahashi, a senior analyst at JP Morgan Securities Japan, says of the domestic auto makers and suppliers. "Time will tell whether they can continue at this pace.”
Kota Yuzawa, auto analyst at Goldman Sachs Japan, expects auto makers’ losses to approach ¥250 billion ($3 billion) in the first quarter of the current fiscal year ending June 30. But he foresees a strong recovery from July onward and a full-year profit exceeding ¥1.3 trillion ($15 billion).
“We expect most companies to post operating losses in the first quarter, but thereafter we expect them to recover in line with a recovery in production,” he says.
So far, Nissan and Honda are resuming one-shift operations starting Monday, April 11, while Mitsubishi, Suzuki and Daihatsu already have begun running single shifts this week.
Industry-leader Toyota said today it will resume operations at all of its 18 plants for eight days, from April 18 until the start of Japan’s ‘Gold Week’ holiday on April 28. Included will be the damaged Miyagi factory of its subsidiary Central Motor, which produces the North American Yaris.
Ford working with ASEAN suppliers to provide parts for regional plants.
Management will make a decision during the 2-week holiday, after reassessing the parts situation, about restarting operations on May 10, the first day back.
Meantime, the auto maker will begin Corolla Axio and Raum production on April 11 as scheduled at its 50-year-old Central Motor west of Tokyo that had been targeted for an April closure prior to March 11 earthquake and will continue making three hybrid cars – the Prius and Lexus HS 250h and CT 200h – at its Tsutsumi and Miyata facilities, where output resumed March 28.
Toyota suppliers Toyota Motor Tohoku, Toyota Boshoku and Primearth EV Energy have resumed or will soon resume operations in Miyagi prefecture.
Primearth EV Energy’s Miyagi plant, which produces nickel-metal-hydride batteries for Toyota hybrids, will be in operation by the Golden Week holiday, a company spokesman tells Ward’s.
The ¥30 billion ($352 million) factory, located north of Sendai and one of three Primearth battery plants in Japan, was damaged by the earthquake.
Yet, nothing is certain in this volatile region, where it’s prudent to expect the unexpected.
“It only takes one part to hold up the whole production system,” warns Clive Wiggins, senior analyst at Macquarie Capital Securities (Japan). “There’s a possibility we will all be pleasantly surprised, but the fact is we anticipate setbacks over the next quarter.”
One inescapable new fact of life is ongoing power shortages this summer, forcing all manufacturers in eastern and northeastern Japan to scale back operations. The regions’ two main electric utilities, Tokyo Electric Power and Tohoku Electric Power, both have lost half their generating capacity.
These power shortages directly will affect only 20% of vehicle-production capacity and, by extension, 20% of materials and component output. Manufacturing operations west of the Fuji River in Shizuoka prefecture, part of the industrial heartland that includes Osaka and Aichi, remain untouched.
No Suzuki, Mitsubishi, Mazda and Daihatsu plants will be affected, nor will most Toyota and Honda plants, along with their home-base suppliers. Not so for Subaru and Nissan, both with their main operations east of the Fuji River in Kanagawa, Tochigi and Gumma, although Nissan’s Kyushu plants will be all right.
The most serious problem may prove to be damage to scores of chemical and resin suppliers along the northern and northeastern seaboard, mostly at the Tier 3, 4, and 5 levels, whose special products cannot easily or quickly be replaced.
Makoto Kurosawa, senior materials analyst at CLSA Asia-Pacific Markets, warns this problem could hit Toyota the hardest, given the auto maker’s extensive model lineup and use of high-grade, specialized materials from plastics and paint to synthetic rubber and steel.
“They’re just finding out now,” he says, which may be one reason why the auto maker has lagged in committing to full resumption of operations at its domestic plants.
But no one can be sure about what will happen in the months ahead. Tokyo-based Deutsche Bank Group analyst Kurt Sanger says the firm’s recent report foresaw Japanese global automotive production down about 15% from original predictions of 23 million units.
But he adds candidly, “Given the level of uncertainty over the depth and duration of any disruption, we will surely be wrong in our absolute figures.”
Even so, Ward’s survey of Japanese suppliers has found much that is encouraging. All but one of Japan’s 44 domestic vehicle plants is ready to resume operations, and that one, Central Motor’s Miyagi plant, will start up April 18. All major in-house component factories are back on stream, while almost all Tier 1 suppliers have resumed operations or are ready to do so.
Tier 1 suppliers, such as Japan Brake System, with plants needing repairs, have generally been able to shift production to other sites.
Among other examples, when Nippon Steel’s Kashima Works was overrun by the tsunami, the company shifted wire-rod production used for automotive shafts and gears to other facilities. JSR, Japan’s leading supplier of synthetic rubber, also shifted output away from the region.
Renesas Electronics, the world’s leading manufacturer of automotive microcontrollers used in everything from windshield wipers and lighting to braking and steering systems, suffered extensive damage to its Naka plant in Hatchinaka, Ibaraki prefecture.
But while Renesas President Yasushi Akao announced March 28 that operations would not resume until early July, company spokeswoman Kyoko Okamoto tells Ward’s the supplier will meet all customers’ orders on time from existing stocks and by shifting production to two other facilities in Japan.
It should be noted the Naka plant only accounts for one-fourth of Renesas’ microcontroller production for auto makers and their suppliers. Okamoto reports the Thursday April 7 7.4- magnitude earthquake did not damage the facility and renovations are on schedule.
Although four Fujitsu Semiconductor plants were damaged by the March 11 event, partial operations resumed on March 23 and 28 and on April 3.
The damaged Kitakami plant of Iwate Toshiba Electronics, a subsidiary of Toshiba, also resumed limited operations on March 28. Until full output is possible, part of production has been shifted to factories in Oita, Hyogo and Ishikawa prefectures.
Toshiba Mobile Display, a supplier of liquid crystal displays for car navigation systems, expects its Fukaya plant in Saitama prefecture to be down until the end of April. The company provides displays to Alpine Electronics, which makes navigation systems for Honda and several prominent European car makers.
Alpine, itself, with five plants in Iwate, Fukushima prefecture, resumed operations in late March. However, Jennifer Quon, a spokeswoman for Alpine Electronics of America, reports the company is experiencing problems with its Japanese suppliers. “This is obviously not just an Alpine issue. It’s industry-wide,” she says.
Information about paint shortages remains sketchy but appears to be less dire than reported, despite significant damage to the Tochigi plant of Nippon Paint, a leading Toyota supplier. Although the facility may be down for three months or more, a spokesman in Osaka says company plants in Takahama and Hiroshima can cover the shortfall.
Potentially more serious is damage to a Merck KgaA facility in Onahama, 35 miles (56 km) south of the damaged Fukushima Dai-ichi nuclear power plant. The plant produces pigments including Xirallic, used in certain metallic paints.
A Merck KGaA spokesman at Darmstadt headquarters in Germany says it’s possible to supply pigments, all but Xirallic, from other plants in China, the U.S. and Germany.
There is some good news regarding transport in the quake-stricken region, as well. Yoshiaki Higuchi, planning director for the Ports and Harbors Assn. of Japan, says after debris was removed from 15 severely damaged ports (in northeastern Japan), at least one berth in each port, including Sendai and Onahama, can accommodate ships again.
The breadth and depth of infrastructure damage along this Japanese coastline was graphically illustrated at these two ports, which were flooded by 30-ft. (9-m) waves crashing over breakwaters, and later burned in the case of Sendai.
Gasoline shortages, which has hampered the inflow of relief suppliers and outflow of food and other daily necessities to buyers in Tokyo and Yokohama, have began to ease during the week of March 21, as two area refineries, shut down after the March 11 quake, came back on stream.
Three other refineries, representing 12% of the nation’s gasoline and diesel supply, were lost: a 145,000 barrels-a-day refinery in Sendai, a 189,000 bbl/day unit in Kashima, Fukushima prefecture and 200,000 bbl/day unit in Chiba.
In addition to the Kawasaki and Negishi refineries coming back on stream, refineries located in Central and Western Japan, many with excess capacity, have begun diverting fuel to areas experiencing shortages.
With 40% of electric-generating capacity gone in eastern and northeastern Japan and no timetable set yet to restore it, power shortages are expected to hurt industrial output, especially this summer, although the impact will vary.
A review of some 30 steelmaking facilities shows only four: Nippon Steel’s Kamaishi Works in Iwate prefecture, JFE Steel’s Chiba Works and Nisshin Steels Ichikawa Works in Chiba prefecture and Sumitomo Metal Industries’ Kashima Works in Ibaraki prefecture, are served by Tokyo Electric Power.
All four have indicated they will shift production as necessary to other facilities in Japan.But auto makers will not get off so easily and are discussing ways and means of conserving power.
“Toyota, Honda, Nissan and other auto makers are talking about sharing electric power and partial solutions to shortages,” says Koji Endo, Managing Director, Advanced Research Japan.
“I suspect many will take very long summer vacations. And to conserve electricity, they may only run night shifts, when it’s cooler, instead of day shifts, and perhaps operate on weekends and shut down production during two weekdays.”
Because Nissan’s Iwaki V-6 engine plant, 40 miles (64 km) south of the Fukushima Dai-ichi power plant, will be out of commission and under repair until April 18, the auto maker will source cylinder blocks, cylinder heads and crankshafts from its Decherd, TN, plant beginning this month.
Transit time from Nashville to Yokohama is about 19 days and to Fukuoka about 20-22 days.
Dave Reuter, Nissan Americas vice president-corporate communications, says this is a temporary arrangement, but could be extended.
Unstated, other U.S. suppliers of Japanese auto makers could follow suit, if necessary. More generally, Reuter says Nissan would not resume operations at its Japanese plants “if we couldn’t assure a steady supply of parts.”
However, reports of troubled production outside of Japan appear overblown. For example, a check with industry experts offers a clearer picture of the situation in Southeast Asia.
Says Neal McCarthy, ASEAN Communications Director for Ford in Bangkok: “We are working with our suppliers on a daily basis as we monitor the fast-changing events in Japan. We have not experienced any production disruptions at our plants (in Thailand, the Philippines and Vietnam).”
Honda has assembly plants in four of the 10-member Association of Southeast Asian Nations countries that produce vehicles: Thailand, Indonesia, Malaysia and the Philippines. Spokesman Keitaro Yamamoto says local content is about 90%. “Some parts come from Japan, but currently our ASEAN plants still have parts stock and are continuing production.”
Yamamoto also says the number of problem suppliers in Japan has fallen from more than 20 several days after the March 11th earthquake to fewer than 10 today.
Toyota resumed production of parts for overseas assembly on March 21, and “we are hoping that any large disruptions in overseas production have been forestalled,” says Toyota spokesman Paul Nolasco in Tokyo.
“Such parts production is taking place mainly at directly owned and operated Toyota non-vehicle plants in the Aichi (Japan) area. For the time being, our overseas operations are being adjusted through no overtime and no work on scheduled days off.”
Tetsuji Inoue, a spokesman for Mitsubishi, tells Ward’s, “There will be no immediate effect on shipments of completely built-up units.” Stock in Japan for producing CKD kits for export are sufficient to prevent any immediate impact on overseas assembly.
Says Senior Market Analyst Ammar Master, with J.D. Power Asia Pacific in Bangkok: “Immediately after the earthquake, Toyota shut down production in Thailand for about a week. Nissan and other auto makers eliminated overtime and slowed production to mitigate the ripple effect of a components shortage.
“But most vehicle manufacturers I’ve talked with say they have enough imported components inventoried to maintain production until mid-April.”
Hajime Yamamoto, a director of IHS Automotive in Bangkok, says all auto makers in ASEAN still are operating but are reducing working hours. “We expect slower production will last until the middle or end of April. By the end of April, auto makers could run out of stock on hand.”
In the U.S., component shortages at Toyota and Honda plants could lead to lower sales. Yet on April 1, Toyota reported a 55-day stock of Toyota vehicles and 35-day stock of Lexus models. At the end of March, Honda had a 47 days’ supply of Honda and Acura brands. The industry standard is 60 days.
Toyota Motor Sales U.S.A. spokesman Steve Curtis says, “Our North American plants, which build nearly 70% of the vehicles we sell here, continue to operate on a normal 2-shift schedule. And we continue to build replacement parts in Japan, along with parts for overseas production, so we’re doing all we can to minimize any disruptions to our operations.”
Although the exact timing of full recovery remains uncertain, no one questions the ability of Japanese assemblers and suppliers, wherever they may be, to regain full competitive strength before too long.
Japanese Auto Plants Affected by Electric Power Shortages:
1. Nissan Oppama
2. Nissan Tochigi
12. Hino Hamura
13. Hino Hino
14. Isuzu Kawasaki
15. Isuzu Fujisawa
16. UD Trucks/Nissan Diesel Ageo
3. Nissan Shatai Hiratsuka
4. Honda Sayama
5. Subaru Ota
6. Subaru Yajima (main)
7. Toyota/Kanto Auto Works Susono
8/9. Toyota/Kanto Auto Iwate x2
10. Toyota/Central Motor Miyagi
11. Daimler/Mitsubishi Fuso Kawasaki
Plants Not Affected:
1. Toyota Tahara
2. Toyota Tstsumi
11. Toyota/Gifu Auto Body Kakamigahara
12. Daihatsu Ikeda
13. Daihatsu Kyoto
14. Daihatsu Shiga
15/16. Daihatsu Oita x2
17. Honda Suzuka
18. Honda/Yachiyo Yokkaichi
19. Mazda Hiroshima
20. Mazda Hofu
21. Mitsubishi Okazaki
3. Toyota Takaoka
22. Mitsubishi Mizushima
23. Mitsubishi/Pajero Mfg. Sakahogi
24. Nissan Kyushu
25. Nissan Shatai (Kyushu)
26. Suzuki Kosai
27. Suzuki Hamamatsu
28. Suzuki Iwata
4. Toyota Motomachi
5. Toyota Miyata (Kyushu)
6. Toyota Shatai Kariya
7. Toyota Shatai Inabe
8. Toyota Shatai Fujimatsu
9. Toyota Shatai Toyota City
10. Toyota Industries Nagakusa
Status of Select Japanese Suppliers That Suffered Earthquake & Tsunami Damage:
Akebono Brake Industry – Sagae and Koori plants, Guuma & Fukushima prefectures (brake pads and linings) and Tatebayashi Foundry, Gumma prefecture: operational from March 18.
Bridgestone – Nasu, Kuroiso and Nasushiobara plants, Tochigi prefecture (tires and steel cord): operational from March 25.
JX Nippon Oil & Energy – Kawasaki plant, Kanagawa prefecture (naphtha): operational from March 29.
Kansai Paint – Kanuma plant, Tochigi prefecture (paint): no details about resuming production; presumably will shift production to other Japanese plants.
Keihin – Kakuda plant, Miyagi prefecture (engine control units and air-conditioner compressors for Honda): operational from March 28.
Kobe Steel – Mooka plant, Tochigi prefecture (aluminum sheet & plate for body panels): operational from March 22.
Kureha – Iwaki plant, Fukushima prefecture (inorganic & organic chemicals, PPS resins, battery anode materials and specialty polymers for lithium-ion batteries): to be fully operational by late-April.
Maruzen Petrochemical – Ichihara plant, Chiba prefecture (ethylene): operational from April.
Mitsubishi Chemical – Kashima plants, Ibaraki prefecture (ethylene): both plants to be operational from late May according to Reuters.
Mitsui Mining & Smelting – Hachinohei plant, Aomori prefecture (refined zinc for galvanized steel): operational from late March but concerned about future power shortages
Nippon Piston Ring – Ichinoseki, Kawamata andNogi plants, Iwate, Fukushima and Tochigi prefectures (piston rings and cylinder liners for Honda, Nissan, Toyota and Isuzu): operational from March 31.
Nippon Steel – Kashima Works, Ibaraki prefecture(wire rod): production shifted to other plants.
Calsonic Kansei – Nihonmatsu plant, Fukushima prefecture (instrument clusters and sensors): operational from March 28.
Nippon Paint – Utsunomiya plant, Tochigi prefecture: undergoing repairs which will take a minimum of three months; able to cover capacity shortfalls from its Takahama and Hiroshima plants in Aichi and Hiroshima prefectures.
Nissan – Iaki plant, Fukushima prefecture (V-6 engines): to be operational from April 18.
NOK – Fkushima, Nihonmatsu & KitaIbaraki plants, Fukushima and Ibaraki prefectures (oil seals, piston seals, gaskets, resins & urethane products): fully operational from late March.
Primearth EV Energy – Kitagami plant, Miyagi prefecture (hybrid batteries): to be operational by late April.
Renesas Electronics – Hitachinaka plant, Ibaraki prefecture (microcomputers): to be partially operational from early July.
Sakai Chemical Industry – Onahama, Otsuguro and Yumoto plants, Iwaki and Fukushima prefecture (titanium dioxide, zinc oxide, dielectric materials and fluorescent materials for flat-panel displays): operational from early and mid-April.
Sumitomo Metal Industries – Kashima Steel Works, Ibaraki prefecture (steel plate): operational from mid- to late-March.
Sumitomo Rubber Industries – Shirakawa plant, Fukushima prefecture plant (tires): operational from March 22.
Toyota Boshoku – Kitagami, Kakuda andOhira plants, Iwate & Miyagi prefectures (seats, center liners & engine covers): operational but can’t procure needed materials, a problem for all Toyota Boshoku plants in Japan.
Toyota Motor Tohoku – Kitagami plant, Miyagi prefecture (hybrid brake systems, electronic suspension systems & torque converters): operational from March 28.
Dowa Metals & Mining – Akita, Akita prefecture (electrolytic zinc): operational from April but concerned about future power shortages.
Toyo Tire & Rubber – Sendai plant, Miyagi prefecture (tires): operational from March 23.
Fujitsu Semiconductor – Isawa, Murata and two Wakamatsu plants, Iwate, Miyagi and Fukushima prefectures (semiconductors): Murata and both Wakamatsu partially operational from March 28; Isawa partially operational from April 3.
Hitachi Automotive Systems – Fukushima and Hitachinaka (Sawa) plants, Fukushima and Ibaraki prefectures (electronic control units, sensors & suspension systems): partially operational from March 25; air-flow sensor production fully operational from April 4.
Honda – Mooka plant, Tochigi prefecture (engine, suspension and transmission parts): repairs completed as of March 24.
Iwate Toshiba Electronics – a Kitakami plant, Iwate prefecture (semiconductors): operational from April 1.
©Japan Brake Industrial – Namie plant, Fukushima prefecture (disc pads and brake linings for Honda and other automakers plus Tier 1 suppliers like Akebono Brake, Hitachi Automotive Systems and Nissin Kogyo): operations suspended indefinitely because the plant is located within 19-mile (31-km) evacuation zone of the damaged Fukushima Dai-ichi nuclear power plant; the company will shift production to other facilities.
JSR – Kashima plant, Ibaraki prefecture (synthetic rubber): partially operational from mid-April; in the interim, production shifted to JSR’s Chiba plant although no prospect for securing EP rubber raw materials.
About the Author
You May Also Like