Japanese Auto Makers Stalled by Supply-Chain Bottle NecksJapanese Auto Makers Stalled by Supply-Chain Bottle Necks
Toyota may lose 500,000 units of production if the auto maker can't supply key materials and components to its plants, one analyst estimates, noting Nissan and Honda will suffer serious losses, as well.
March 25, 2011
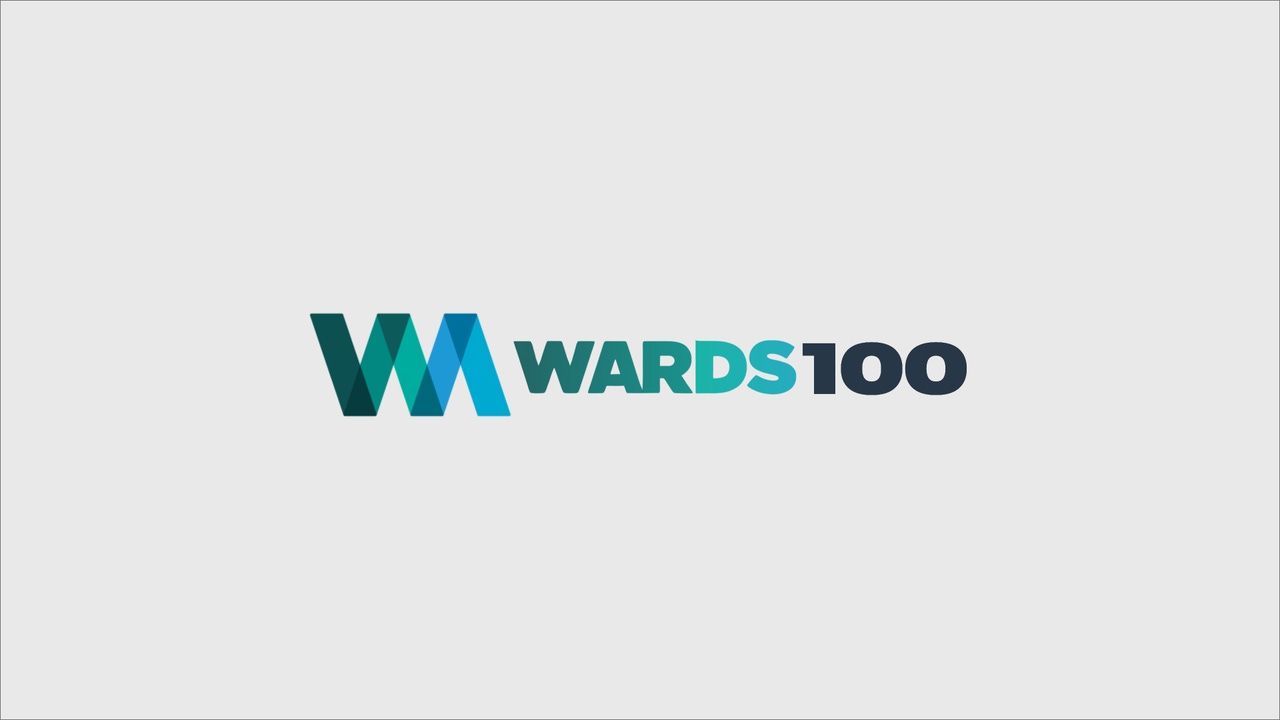
Nearly two weeks after northeastern Japan was hit by a deadly earthquake and tsunami, damaging nuclear reactors and resulting in power shortages, Japanese auto makers have determined most of their vehicle plants are intact but still find domestic production stalled as they struggle with supply-chain bottlenecks.
“Japan’s automobile industry was hard hit,” says Koji Endo, managing director of Advanced Research Japan.
“Many car plants, including some of Toyota’s, Honda’s and Nissan’s, could be shut down for more than a month, until late April.”
Indeed, Nissan has taken the unusual step of going against some governmental advisories in asking 550 workers, who were on standby, to return to their jobs and offer assistance in repairing its damaged Iwaki engine plant in Fukushima prefecture, despite radiation leaks at Tokyo Electric Power’s crippled Fukushima Dai-ichi nuclear facility 40 miles (64 km) north.
IHS Global Insight said on Thursday a prolonged disruption of Japanese parts lasting 12 weeks could halt global vehicle production as much as 35%, for an estimated loss of 5 million light vehicles.
Endo calculates Toyota may lose a half million units of production if the auto maker can’t supply key materials and components to its plants. He also believes Nissan and Honda will suffer serious losses, as well.
Unstated but implied, the domestic industry’s widespread production losses will cost manufacturers billions of dollars in revenues.
Goldman Sachs Japan estimates the impact on industry profits of stopping production for a single day at more than ¥16 billion ($200 million), including ¥6 billion ($75 million) for Toyota and ¥2 billion ($25 million) each for Honda, Nissan and Suzuki.
More than 95% of Infiniti cars sold in U.S. last year fitted with engines made at Iwaki plant.
Multiply that by 21 days, one month's downtime, and the total could exceed nearly ¥350 billion ($4 billion). Goldman Sachs Japan does not include Japanese truck makers in its estimate. What Japanese auto makers face now more than anything is the herculean task of bringing components and materials from the stricken northeast region to their plants at home and abroad.
Kohei Takahashi, auto analyst at J.P. Morgan Securities Japan, warns their plight may be more serious than originally reported.
He estimates upwards of 100 automotive suppliers, including many in second and third tiers, are facing problems that will cause their customers serious headaches or worse. “Not only have plants that make electronic components, specialty steel and brakes been damaged by the earthquake and tsunami, so too have plants that produce materials including semiconductors, plastics and rubber,” he says. “This is not like the Riken situation in 2007. This is more systemic.”
In July 2007, Riken’s main piston-ring plant in Kashiwazaki on Japan’s west coast suffered extensive damage from the Niigata earthquake, forcing as many as four auto makers, including Toyota and Honda, to suspend vehicle production. With assistance from customers including Toyota that reportedly dispatched 200 engineers, Riken, with 50% of the Japanese piston-ring market, was able to resume operations in less than a week. Downtime for the auto makers was two weeks.
Today, the damage to suppliers and infrastructure from Japan’s latest disaster spans more than 350 miles (563 km) of Japan’s eastern seaboard, from Aomori in the north to Chiba east of Tokyo.
Tokyo Electric Power, for instance, has lost more than half its power-generating capacity. The nation's largest electric utility, which serves more than 40 million customers in eight prefectures and Tokyo – including literally thousands of manufacturing plants, big and small – anticipates power shortages through the end of the year.
Toyota to resume Prius hybrid production at Tsutsumi plant March 28.
Meanwhile, the ports of Sendai, Kamaishi and more than a half dozen others have suffered major structural damage and will take months, rather than weeks, to reopen. And three oil refineries, accounting for 10% of Japan’s gas and diesel fuel supply, were destroyed.
Preliminary estimates put the cost of rebuilding the earthquake and tsunami-stricken areas as high as ¥23 trillion ($280 billion).
Honda spokesman Keitaro Yamamoto reports 10 key suppliers still are unable to deliver components to the auto maker’s main assembly plants in Saitama, Suzuka and Yokkaichi. While declining to disclose names, Yamamoto advises these include makers of engine electronics and brake parts.
Earlier, he reported Honda’s Mooka facility, which makes engine, suspension and transmission parts, was “severely hit.”
Honda's latest update on Thursday says repairs to the plant located in Tochigi prefecture, 50 miles (81 km) north of Tokyo and 200 miles (322 km) south of the earthquake’s epicenter, are almost complete. But more time will be needed to fix damage at Honda’s Tochigi R&D Center near Utsunomiya.
Other reports vary from discouraging to encouraging.
Keihin, Honda’s main electronics supplier, reports its Kakudashi plant in Miyagi prefecture has completed production trials and could begin full operation when electricity and other infrastructure-related issues are resolved. The factory builds engine-control units and air-conditioner compressors.
Akebono Brake Industry, which supplies brake components to Honda and other domestic auto makers, reported on March 21 its Sagae and Date-gun plants, where it makes brake pads and linings, were ready to resume operations.
Nippon Piston Ring, with three facilities in Iwate, Fukushima and Tochigi prefectures, said on March 24 all were back up and running. The supplier provides piston rings and cylinder liners to Honda, Nissan, Toyota and Isuzu.
Toyota now says it will resume production of the Prius hybrid at its Tsutsumi plant starting March 28, as well as the Lexus HS 250h and CT 200h hybrids at its Toyota Motor Kyushu facility. It also will begin making components for overseas operations at seven Toyota parts plants.
These include engines at Kamigo; engines, turbochargers and catalytic converters at Shimoyama; suspension parts at Myochi; transmission parts at Miyoshi and Kinura; electronics at Hiyoshi; and forged and hybrid-system components at Honsha.
Toyota spokesman Keisuke Kirimoto declines to comment on when the auto maker might be ready to resume full production at all 16 domestic vehicle plants, including those of affiliated-manufacturers Daihatsu, Hino, Kanto Auto Works, Central Motor, Toyota Auto Body and Toyota Industries.
Toyota earlier reported minor damage to three affiliated factories run by Kanto and Central in earthquake-affected areas. And Kirimoto confirms the auto maker is experiencing problems with suppliers of electronic parts, resins and synthetic rubber, but offers no details.
However, Toyota Motor Tohoku 's Kurokawa plant in Miyagi prefecture is back up and running, though not at capacity. The factory suffered only minor damage, as it is located 80 miles (129 km) west of the earthquake's epicenter.
The facility makes electronically controlled brake systems for Toyota and Lexus hybrids, as well as electronic modulated suspension systems, active-height-control devices and torque converters. JSR, Japan’s leading manufacturer of synthetic rubber, reported damage to a warehouse and loading berth at its Kamisu chemical plant in Ibaraki prefecture. As of March 22, the supplier had not resumed operations.
Nippon Steel’s Kashima Works, which makes wire rods for automotive shafts and gears, reported significant damage including flooding. And the plant's main port, Kamaishi, remains closed. The leading Japanese steelmaker said on March 23 it was in the process of shifting orders to other Japanese facilities and group companies.
Japan's two leading original equipment tire makers, Bridgestone and Sumitomo Rubber Industries, both have reported their plants are back up and running. Bridgestone, with three facilities in Tochigi prefecture, had two facilities back in operation by March 16.
There is no word on the third as of yet. Sumitomo Rubber, which makes Dunlop tires, reopened its Shirakawa plant on March 22.
Toyota disclosed Wednesday it would delay the late-April launch of the new Prius station wagon in the Japanese market until the auto maker's domestic dealer network is fully back in service.
Nissan spokesman Mitsuru Yonekawa declines to name the suppliers creating bottlenecks in the auto maker’s supply chain, but reaffirms Nissan’s intention to begin limited production at its Oppama, Kyushu, Hiratsuka and Tochigi auto plants this week. “We will make cars until we run out of parts,” he says.
However, Nissan’s decision to ask the Iwaki engine plant workers to return to their jobs could be controversial. Damage to the nuclear plant has kept the nation on uneasy alert for the last 12 days, when first reports of structural damage to the reactors were disclosed.
As recently as March 23, the French Embassy in Tokyo was recommending French nationals ‘leave the Tokyo area to the south or France.’ Tokyo is 150 miles (241 km) away from the crippled reactor. Nissan’s largest shareholder, Renault, is French.
The American Embassy in Tokyo also has issued travel advisories. The U.S. Centers for Disease Control and U.S. Nuclear Regulatory Commission on March 20 urged American citizens “within 50 miles (81 km) of the Fukushima reactors (to) evacuate the area.”
A follow-up advisory on March 22 recommended U.S. citizens residing within 50 miles of the Fukushima plant, “leave the area or remain indoors as much as possible if departure is not possible.” No subsequent advisories had been issued as of Friday, Tokyo time.
Nissan spokesman Toshitake Inoshita says the auto maker “follows what the Japanese government advises and they've advised that over 30 km (19 miles) is safe."
For Nissan, closure of the Iwaki plant for any extended period would present serious problems, as it is the auto maker’s only domestic production base for VQ V-6 engines, installed in almost all Infiniti vehicles, as well as the 370Z, Murano and Elgrand models.
Nissan sold 103,411 Infinitis in the U.S. last year, Ward’s data shows. More than 95% were fitted with engines produced at the Iwaki plant.
Fortunately, the auto maker need not make an immediate decision regarding alternate sourcing, with an estimated 4-month supply of Infiniti cars in the pipeline, including nearly 50 days of stock on the ground in the U.S. However, Nissan has begun feasibility studies on producing the VQ engines for Japan at its Decherd plant in Tennessee.
Decherd currently operates two 10-hour shifts four days a week and should be able to boost production 25%-50% simply by introducing a 5- or 6-day workweek.
“We are considering all options,” says Dave Reuter, vice president-corporate communications for Nissan North America. “But we're not yet at the point we must make any decisions.” The U.S. manufacturing arm already supplies Decherd V-8s to Japan for the Infiniti M56, and so has some experience with the auto maker's Japanese supply chain.
Other Nissan suppliers reporting damage include Hitachi Automotive Systems’ Hitachinaka (Sawa) and Fukushima plants, which supply electronic control units, sensors and suspension systems; and Calsonic Kansei’s Nihonmatsu factory in Fukushima prefecture, which, among other things, produces instrument clusters and sensors.
Most other Calsonic plants, including those in Tochigi, Gumma, Kodama, Yoshimi and Oppama, report little or no damage, according to the company's website. Hitachi Automotive has not updated its website since March 17, when it reported damage to both buildings and equipment.
IHS Global Insight reports Hitachi Automotive’s Hitachinaka plant supplies 60% of airflow sensors to General Motors, Ford, Renault, Nissan, Volkswagen and Toyota.
Renesas Electronics, a joint venture between NEC, Hitachi and Mitsubishi Electric and a leading supplier of automotive-use semiconductors, reportedly has reopened several plants.
Still closed, however, is the Naka semiconductor facility in Ibaraki prefecture, which makes microcontrollers for cars and supplies 40% of the global market, according to Kota Yuzawa, auto analyst at Goldman Sachs Japan.
Yuzawa reports the plant “suffered relatively major damage and is unlikely to restart operations until late April or early May.”
However, he believes the damage is less severe at Fujitsu’s Iwate plant, which also fabricates microcontrollers and could open in several weeks. Toyota and its affiliated suppliers are the main customers for Fujitsu microprocessors, he says.
Despite the near-term problems involved in restoring the supply chain, Yuzawa estimates the impact on earnings will be short term.
“Low capacity utilization levels at Japanese auto plants globally of around 80% means that once the supply chain stabilizes any production shortfall in the first quarter of fiscal 2011 (April 1-June 30) can be made up in the July-September period by raising plant utilization,” he says.
That, at least, is the hope.
About the Author
You May Also Like