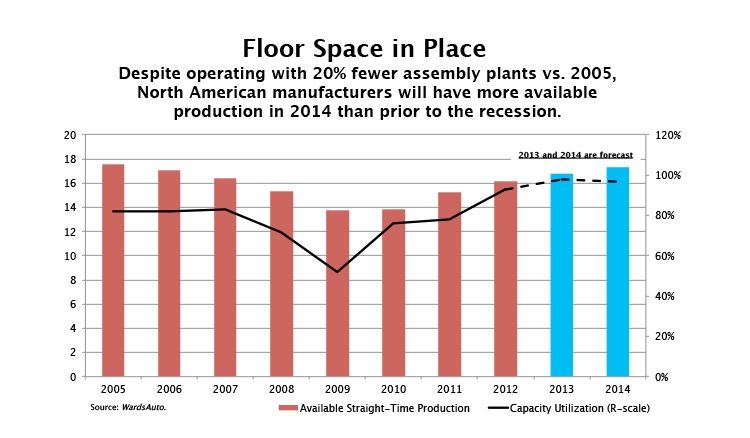
The Great Recession that gripped the North American auto industry in 2008 and 2009 has ended, so it’s time to crack open the corporate pocketbook and invest in the future, right?
If only it were that easy.
Even before the downturn, automakers and suppliers at all levels knew the industry had too much manufacturing capacity and took steps to rationalize. Dozens of bankruptcies, including those of General Motors and Chrysler, were resolved with plant closings and headcount reductions, and that has left the industry in a tight spot.
Despite realizations that another downturn is inevitable at some point, the time has come for suppliers to expand their operations and build new plants if necessary to meet anticipated growth.
WardsAuto/AutomotiveCompass forecasts North American production will rise from 16.1 million light vehicles this year to more than 16.6 million in 2014, and several analysts expect production to exceed 18 million units by 2018. If there are capacity shortages along the way, it will not be at the assembly-line level, WardsAuto data shows.
Excluding supply-chain constraints, labor issues, bad weather and other outside factors, North American auto assembly plants are geared to take on expected demand, and more.
Suppliers are working hard to keep pace, but pinch points remain in the delivery of electronics, tires and powertrain components such as large castings, forgings and precision machined components, says Dave Andrea, senior vice president-industry analysis and economics at the Original Equipment Suppliers Assn.
Recently, GM had to slow production of its all-new fullsize pickup trucks due to a shortage of axles.
Supplier American Axle & Mfg. tells WardsAuto the short-term strain on axle output should be resolved soon as additional installed capacity will come online with the launch of new fullsize SUVs and heavy-duty pickups from GM’s K2XX architecture in the first quarter of 2014.
Even with current constraints, AAM spokesman Chris Son says, “Our daily production schedules have been running significantly higher than our contractual capacity requirements for certain high-volume models in the K2XX program.” He says AAM is working with GM to make appropriate capacity adjustments both in volume and mix.
The OESA has 450 member companies, and Andrea says some suppliers are investing in additional capacity because they are confident current production levels will be sustained.
With North American production volumes climbing the past several years, parts makers have exhausted most of their avenues to stretch available capacity, Andrea says.
“That’s running plants at three shifts and really pushing the people, and at that point we know we need to start expanding a bit,” he says. “But we don’t want to lose that sense of discipline that’s giving us the return on investment and the profitability we have today.”
In recent months, dozens of suppliers have announced plans to expand:
Composites specialist Continental Structural Plastics will add a new $18.3 million paint facility in Carey, OH, to support growing needs of the auto industry. CSP plans to employ 50 workers at the new plant when it is operational by summer 2015.
Kiekert, a German producer of automotive door locks and components, is investing $2 million to expand its U.S. headquarters and production facilities in Wixom, MI. The operation, which manufactures door latches for Ford, employs 80 people currently and headcount is expected to reach 120 within a year.
Denso plans to spend $2.2 million for a new shipping plant warehouse in Montgomery, AL, employing 45 people working three shifts. Expected to be operational in April, the facility will support movement of climate-control systems for North American customers.
German painting technology supplier Dürr opens a new plant in Querétaro in central Mexico with 280 employees to accommodate a growing volume of business. From 2009 to 2012, Dürr sales more than doubled to E2.4 billion ($3.3 billion). Growth continues this year.
Halla Visteon Climate Control this year adds 30,000 sq.-ft. (2,787 sq.-m) of floor space at its climate-control plant in Shorter, AL. The facility opened in 2003 and was expanded in 2007.
Among automakers, new plants, 3-crew/third-shift schedules and expansions have lifted North American assembly plants to above their pre-recession available production levels.
There will be 71 plants assembling vehicles in 2014, up from 68 at the beginning of 2013. That’s down from 88 in 2005, when light-vehicle production totaled 15.8 million units.
Clearly, much of the industry has found a way to do more with less, but certain supply-chain segments wrestle with shortages that only will worsen with time.
Tooling Shortage Coming
Consulting firm Harbour Results recently released a study that predicts a massive shortage of vendor tooling will occur within five years.
Vendor tooling is purchased by automakers for Tier 1 and Tier 2 suppliers to use in manufacturing vehicle parts. Every car requires as many as 3,000 vendor tools to make unique parts, such as a bumper fascia. Without these tools, assembly lines screech to a halt.
There are about 750 vendor tool suppliers supporting the North American auto industry, and many of them are smaller companies, most in the upper Midwest, with average revenues of $15 million annually, according to Harbour Results.
In North America, the auto industry currently spends about $9.2 billion a year on vendor tools, an amount expected to reach $15.2 billion by 2018 as auto makers launch record numbers of new models (42 in 2014) requiring more customization.
“We’re telling you we don’t even have enough capacity to go out to 2018,” says Laurie Harbour, president and CEO of Harbour Results. “Each year, the problem gets worse and worse. We definitely have a pinch point here.”
Over the past 15 years, the North American industry has lost about 250 tool shops, and those that remain have become more selective in choosing customers agreeing to more favorable payment terms. Still, profit margins remain slim for struggling tool makers.
It appears overseas companies are more eager to step in and fill the $6 billion capacity gap for vendor tools in North America.
“In the last six months, we have talked to German tool makers – people in Germany and mainland Europe – who say, ‘Maybe I will come and build a plant in the U.S.,” Harbour says. Likewise, Chinese investors are shopping for tooling companies in North America.
“There’s no stopping these guys from coming here, buying (tooling companies) and putting in new plants,” she says, adding that German companies are considering bringing their own skilled workers to run facilities here.
“Somebody’s going to fill this,” Harbour says. “We are not going to stop launching vehicles in North America, so we’re going to get tools from somewhere. If the North American base or the Tier 1s don’t want to step up, the OEMs will go to China or India or Indonesia or wherever is appropriate to find tools.”
Another hot market with potential for tool shops is Mexico, which is expected to add capacity to manufacture an additional 2 million vehicles by 2020.
Three new plants are coming on line, including a new Nissan facility in Aguascalientes that just began production. Two other plants also are opening in Mexico in 2014: Honda in Celaya and Mazda in Salamanca.
Mazda’s new plant will build the currently imported Mazda2 and Mazda3, as well as a small car for Toyota, presumably to replace the French-built Yaris.
Honda in Celaya will replace imported Fits and assemble a new Fit-based CUV.
Honda also has announced it is moving the entire platform development for the ’16 Civic from Japan to the U.S. Harbour says Honda typically would rely on tool shops in Japan but now will need them in North America, intensifying the shortage.
The OESA’s Andrea says about 25% of parts suppliers generally are operating at 90% capacity utilization rates or higher. These are the companies investing in new facilities or thinking seriously about it.
“And there’s 25% of the industry still operating at 60% utilization. That’s the piece we still see in this period of rationalization,” he says.
Andrea says the remaining 50% of suppliers is keeping up with customer demand, operating profitably and still seeing a solid return on assets.
“Those are the guys who are really focused on better productivity, the guys who don’t want to build anymore brick and mortar,” he says. “They think about how to get more throughput with existing plants and equipment.”
This 50% remains reluctant to invest in new facilities, fearful the next downturn will leave them burdened with expensive new under-used assets.
Harbour says the time is right for suppliers to invest in new North American facilities, and she believes Detroit automakers will need to as well.
“This market is going to 20 million production units,” she says. “I can only do so much 3-crew, 3-shift, 4-shifts, weekend shifts. When is my maintenance going to break down?”
Harbour doubts a Detroit automaker would open a new plant in the Midwest, but she sees the Southern U.S. or Mexico as a possibility. “As we go into the next five years, I think they will have to think about at least one (new plant),” he says.
Read more about:
2013About the Author
You May Also Like