Quality questions: industry looking for new ways to evaluate suppliersQuality questions: industry looking for new ways to evaluate suppliers
What is the true measure of supplier quality? Is it the number of defective parts that elude inspection and make it all the way to customer plants?Or is it the total number of defective parts the supplier generates? Many in the industry are talking about scrapping the measurement of defects -- commonly known as ppm, or parts per million -- altogether.Consider also that parts that appear to be defect-free
August 1, 1996
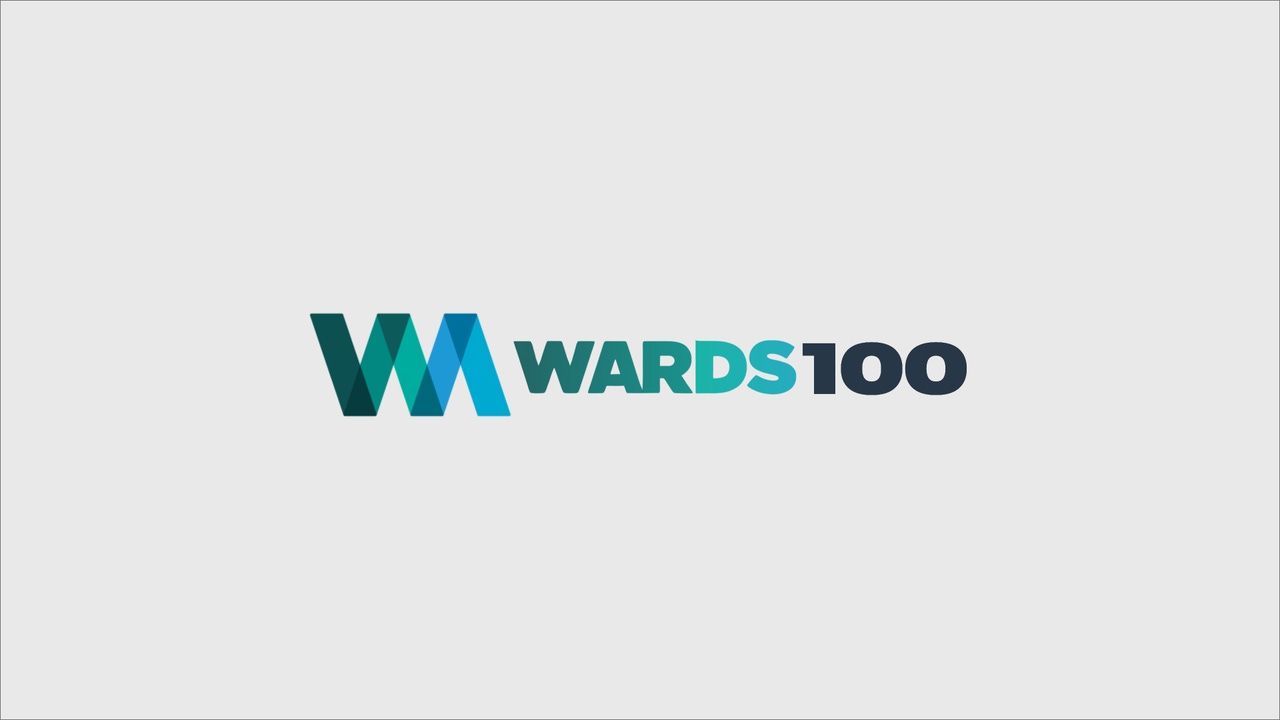
What is the true measure of supplier quality? Is it the number of defective parts that elude inspection and make it all the way to customer plants?
Or is it the total number of defective parts the supplier generates? Many in the industry are talking about scrapping the measurement of defects -- commonly known as ppm, or parts per million -- altogether.
Consider also that parts that appear to be defect-free can still fail in the field, and automakers argue that that also should be part of the quality equation.
As industry sages wrestle with the next method of measurement, the automakers' dream of 100% perfect supplier quality is locking horns with their other goal of low-cost components and systems.
Suppliers, on the other hand, are starting to understand the extent to which defects have an adverse effect on the bottom line.
Harold R. Kutner, General Motors Corp. vice president of worldwide purchasing, is among the most vocal advocates for change. "Ppm is not an acceptable measurement," he says, pounding his first on a conference table for emphasis. "Defects are not acceptable anymore. We contract for perfect parts."
In media interviews and on the banquet speaker circuit, Mr. Kutner proclaims the need for a "pharmaceutical mentality" in the supply base. "When you buy a bottle of aspirin, you expect every pill in the bottle to work," he says. "It doesn't cost more to give us perfect parts."
Mr. Kutner's counterpart at Chrysler Corp., Thomas T. Stallkamp, agrees and says his organization is currently working on ways to measure supplier quality, other than the ppm scale. Other quality experts and supplier analysts concur that a "pharmaceutical mentality" would be helpful, but that it's almost like comparing apples to oranges.
"The high-quality, high-technology, semi-conductor-like equipment used in the pharmaceutical industry can't compare with a 6,000-pound stamping press," says Marc Santucci, a supplier analyst with ELM International Inc. "Having the mentality of the pharmaceutical industry is great, but the reality is that there are other competing forces that prevent you from reaching these goals."
Mr. Santucci notes that continuing pressure on costs often deter suppliers from using the highest-quality raw materials and the most precise manufacturing processes.
Yet there are a few companies delivering parts with zero or near-zero defects. One, Magna International Corp.'s Decoma Exterior Group, has several zero-ppm facilities and has won GM's top Supplier of the Year award for the last two years.
"Companies that have low ppms today are either very, very diligent or have a robust design that is easy to make and a manufacturing process that is consistent," says Ivan Chambers, a quality expert with Monro & Associates Inc., a consulting company.
If suppliers are diligent in confining defective parts, says Mr. Chambers, they "need a test behind a test behind a test." Not to mention a repair facility in the plant that he refers to as "the hidden factory."
"It gets very, very frustrating doing it that way," he continues. "Companies are putting their best and brightest on defect containment and they're burning out and having nervous breakdowns. They should be using the best and the brightest to drive out the root causes of defects."
Mr. Chambers says a company delivering 6,000 ppm (what he calls a Four Sigma condition) wastes 25% of each sales dollar on extra labor, inspections, tests, equipment, repair, excessive cycle time, floor-space and inventory.
"Most organizations aren't even aware of all of these costs," he explains. "They haven't begun to recognize all of the non-value-added containment activity resulting from defects in design and manufacturing. These represent a huge bank account that can be used to invest in design and process improvements and win back lost markets, profits and jobs."
The statistical equivalent to zero defects, says Mr. Chambers, is a Six Sigma condition, which is equal to 3 or 4 ppm. And even if a company delivers near-zero defects to its customers but still actually produces defects, there is a lot of waste in containment that directly effects the bottom line.
Mr. Chambers lists four basic steps that lead to Six Sigma. The first is to get the customer to define the part's absolute functional requirements. Step two is determining the true manufacturing capability of the company's manufacturing processes. The third step is teamwork and negotiation between the supplier's own manufacturing and design departments and the customer. Step four is coming up with new thinking on how to accomplish the functionality required by the customer. "When you get the customer involved in the activity, it's easier to produce zero defects," he says.
ELM International's Mr. Santucci agrees that designing parts to overcome the weaknesses of less-costly raw materials and manufacturing processes is critical, but stresses that inspection also is vital to improved quality.
"You have to inspect," says Mr. Santucci. "You start losing tolerances when tools start to wear out -- not when they wear out.
"Yes, you can operate with the pharmaceutical mentality," concludes Mr. Santucci, "understanding the real-world situation and the prices the industry is willing to pay."
About the Author
You May Also Like