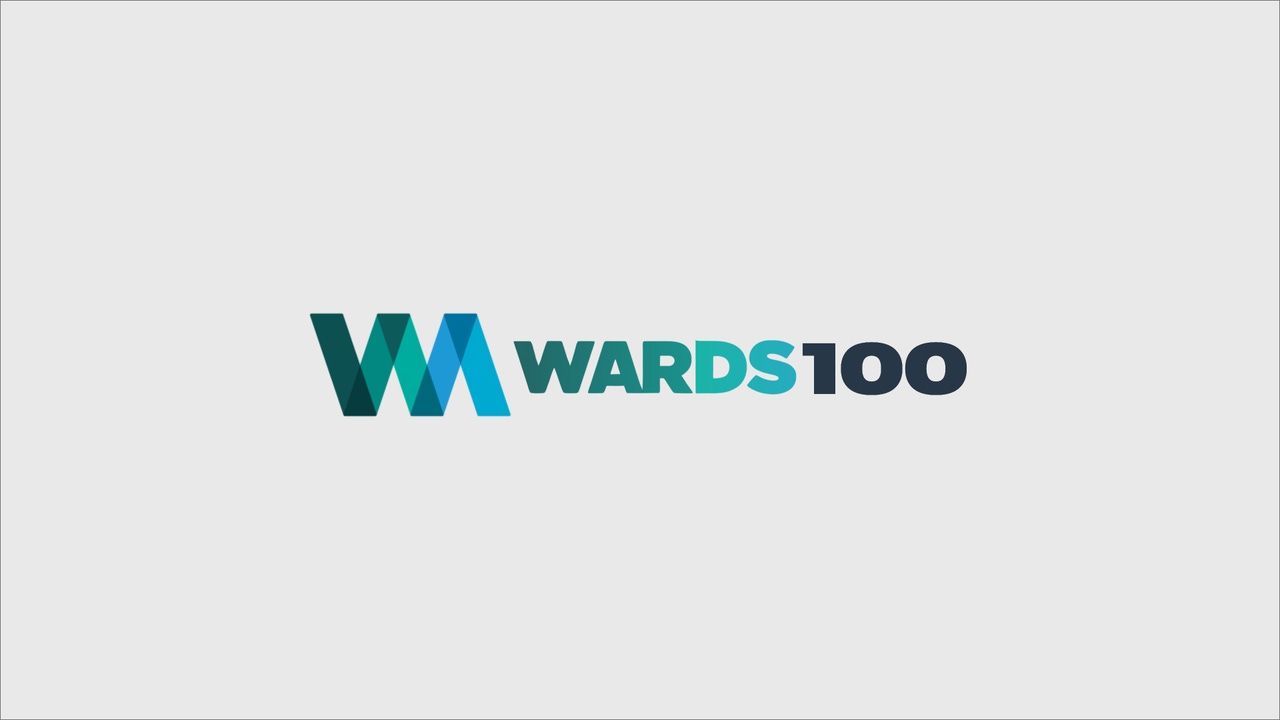
Germany's ZF Group's new axle assembly plant in Edinburgh Parks, Australia — a suburb of Adelaide — demonstrates precisely how global the automotive supply chain has become.
ZF officials say the Lemforder chassis division won the contract in 2003 to produce front- and rear-axle assemblies in Australia for the next-generation GM Holden Ltd. Commodore sedan platform largely because it could source components more cheaply from China, the U.S., Japan, South Korea and the U.K. than could competitor Dana Corp.
Dana, now bankrupt, supplied axles for the last-generation Commodore program, relying primarily on components manufactured domestically in Australia. GM Holden began producing the all-new Commodore last July at its Adelaide plant.
“We have a global sourcing strategy for this facility,” ZF Lemforder Vice President Peter Holdmann says. “We were completely responsible for purchasing. By far, this is the most extended responsibility we have had in a chassis systems program.”
ZF Lemforder announced at the 2005 North American International Auto Show in Detroit that it had won its first axle-manufacturing contract with General Motors Corp., supporting its Australian subsidiary.
Customers, suppliers and ZF employees recently gathered to dedicate the greenfield plant, which started production last summer of front- and rear-axle modules for the Holden VE Commodore lineup.
The program has been filled with both challenges and rewards, executives say. Coordinating a worldwide logistical supply chain for a complete axle module that would include all suspension, drive and wheel-end components was daunting.
To keep costs down, components arrive by ship — generally taking weeks to reach this remote part of the world. Nevertheless, GM Holden requires a fully dressed axle assembly to arrive at its plant's loading dock within a mere two hours of its broadcast order.
Because the Commodore's Zeta platform supports multiple vehicles, there are more than 140 rear-axle and 30 front-axle configurations. GM Holden offers 11 differentials, seven suspensions, three wheel sizes, five brake packages and four stabilizer bars on the vehicles.
This requires ZF Lemforder to be flexible enough to build every axle set to order and to deliver it “just in sequence” to Holden.
The Commodore platform also will spawn the U.S.-bound Pontiac G8, which will be produced in Adelaide beginning this September (likely between 30,000 and 50,000 units a year), and the Chevrolet Camaro, which will come from GM's plant in Oshawa, ON, Canada, in 2008.
ZF content makes up about 35% of the value of each Commodore axle set. Parts come from ZF plants in Shanghai (control arms, lateral arms); Dingley, Australia (rubber bushings); and Darlaston, U.K. (stabilizer links); and in the U.S. from Brewer, ME (suspension ball joints); and Gainesville, GA (differentials).
For the Commodore axles, components are shipped to Australia monthly from China (52 containers), the U.S. (45), Japan (25), South Korea (6) and the U.K. (1).
Once each axle set is completed, it is transported by truck to Holden via a private access road. The distance from supplier to OEM is a mere 2,600 ft. (800 m).
ZF's Holdmann says the supplier identified early on in the bidding process that it needed to source components globally because certain technologies were not available in Australia.
“Plus, the price of components (in Australia) was too high,” he says.
GM Holden also wanted a differential with a lighter aluminum housing. ZF Lemforder obliged, setting up delivery from its plant in Gainesville, GA.
Holdmann says ZF engineers and suppliers in Australia also are key to the success of the program, as they interact with the finished product and with Holden.
“You can't just do this program from the U.S. or from Germany,” he says. “You need local resources and capabilities.”
As with any all-new plant opening, launch bugs hampered the start of assembly, but Production Manager Manuel Karakulak says quality has been outstanding and that no defective axle set has left ZF's plant.
GM has been criticized by suppliers in other parts of the world for failing to achieve projected production volumes, leaving parts makers in a financial pickle.
But for the first six months of the Commodore program, Holdmann says GM Holden built exactly to plan.
The build rate has been 620 vehicles (and axle sets) per day, but that number went down last month to 520 per day.
Holden recently announced it will cut 600 jobs and slow output at Adelaide as Australian consumers migrate toward smaller cars and because additional automation for the new Commodore program has made many jobs redundant.
During a plant tour of the Holden assembly plant, Rodney Keane, executive director-manufacturing, says production will return to 620 units per day in September, when the G8 program begins.
The Commodore lineup at Adelaide consists of large, rear-wheel-drive cars, many of them with powerful V-8s.
Keane, at the ZF Lemforder plant dedication earlier, refers to alarmist local media reports as overblown and says the Commodore is finding success in the marketplace as a car that is fun to drive.
“Despite what you hear, this is an encouraging time for Holden and its suppliers,” Keane says. “The VE Commodore remains the best-selling car in Australia.”
The Commodore easily was Australia's best-selling model in February with 5,544 sales. The country's four domestic auto makers, combined, sold 18,362 Australian-built vehicles in the month, fractionally up from prior-year's 18,312.
Holdmann says ZF Lemforder's plant is not achieving “a high level of production,” and he doubts the facility will need to add a third shift, even when the daily build rate climbs back up to 620 units.
Should volumes go higher, employment at the plant could rise to about 177 from 150 currently. Many plant workers came to ZF Lemforder from Dana as that facility ramped down output for the previous-generation Commodore.
“This plant was planned for three shifts,” Holdmann says of the ZF Lemforder facility, but he also notes it is flexible enough to adapt. He says the ZF plant is profitable at current production levels.
Although there is a fair amount of unused space, Holdmann says ZF is talking with potential customers about new business for the facility. A new full axle program is not likely, but ZF officials say smaller corner modules could be delivered.
Production of a new Holden Ute (similar to the 1970s Chevy El Camino) in the Commodore lineup is due later this year, and a wagon version also is due in early 2008, with potential to boost volumes.
Holdmann says he is pleased with the vehicle, itself, and is confident it will retain its sales leadership in Australia. “There is no fundamental reason why we should not succeed here,” he says.
Reinhard Buhl, group executive and member of ZF's board of management, says the supplier is comfortable with the level of risk associated with the Zeta program, a global architecture that could yield additional opportunities in other parts of the world. “I see more chances than risk at this time,” he says.
ZF has invested about $30 million in its new Australian facility, which is quiet, air conditioned and brightly lit with multiple rows of polycarbonate skylights.
The facility is one of 10 ZF Lemforder axle-system plants worldwide. The division has 1,500 employees and delivers more than 800,000 axle sets per year to auto makers.
Glenn Paine, ZF sales manager and a native Australian, says his company won the Commodore business with an extremely competitive bid and by leveraging ZF's extensive drivetrain expertise.
He says ZF hosted GM Holden officials at its axle systems plant in Duncan, SC, and that the auto maker left extremely confident in ZF's capabilities.
In his comments to journalists, Holdmann does not sugarcoat this facility's mission: It is a long, long way from ZF's Lemforder's technical centers in North America, Europe and Asia and, as a result, must stand on its own.
“We were clear from the beginning. This is a greenfield operation, and it must be completely independent and not depend on support from Germany, Shanghai or the U.S. (operations),” he says. “They have to manage their challenges on their own.”
Australians pride themselves as a fiercely independent lot. It looks like ZF Lemforder's new plant will be a chance for them to prove it.
About the Author
You May Also Like