October 1, 2018
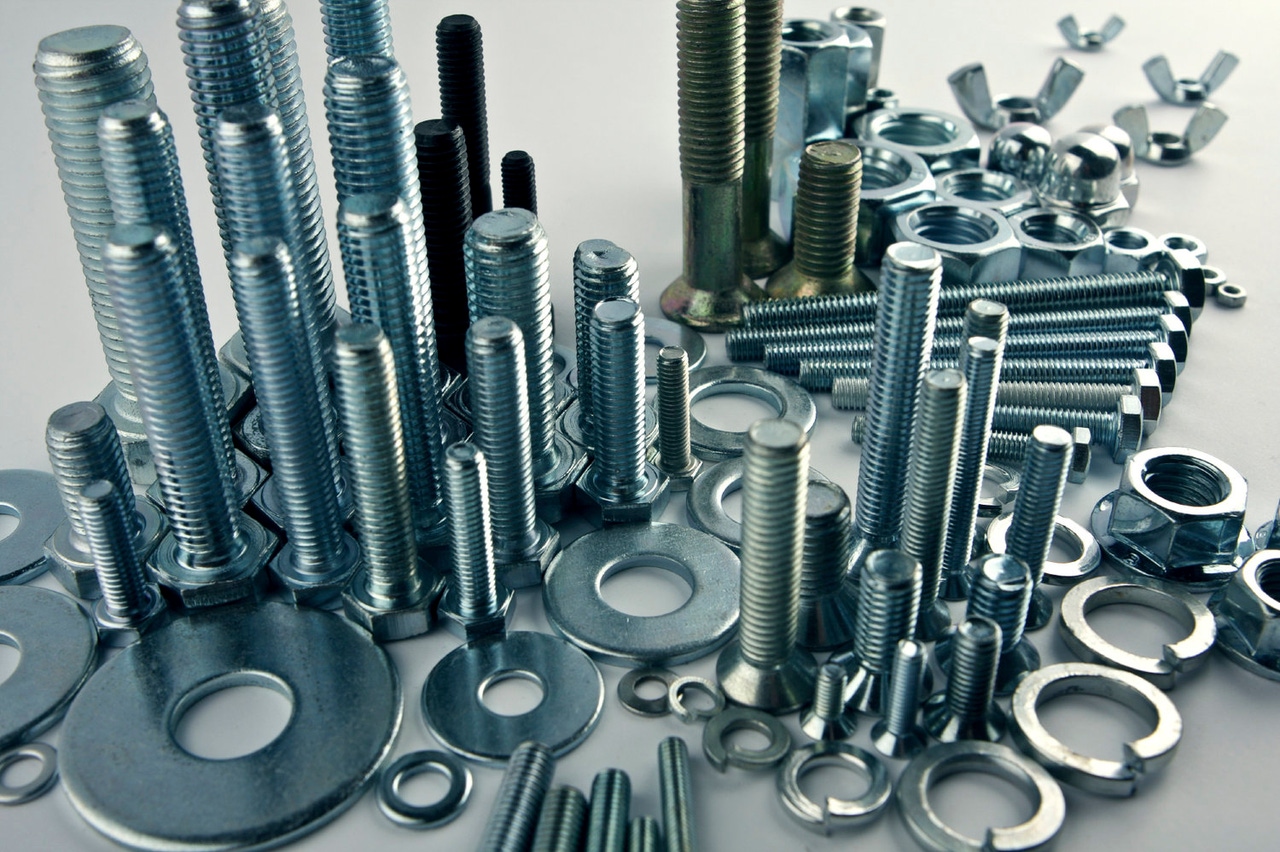
Automotive industry executives are well aware of the importance of a robust and efficient supply chain. Unfortunately, while those decision-makers and supply-chain experts spend a lot of time and energy enhancing the external components of their supply chains (lead times, scheduling, packing and shipping details), a significant missed optimization opportunity often is right under their noses.
The supply chain doesn’t end after parts or products arrive at a plant. Those critical internal links in the supply chain – where and how those parts and products are moved and used on site – are as important as any external logistics. The consequences of neglecting them can be just as costly.
In an industry with tight timelines, complex supply chains and an interdependent network of suppliers, shutting down a production line because you run out of a part can be enormously costly. Consider the startling and sobering fact that up to 11% of organizational waste and inefficiency is the result of intrafacility logistics and structural production issues.
The good news is that an impressive array of new tools and technologies have emerged to fill that gap. Together with customized smart inventory-management systems and supply-chain mapping capabilities, these new solutions can dramatically improve automotive supply-chain optimization.
Smart vending machines, such as Crib Boss, can dispense and monitor MRO items to employees. Weight-based scales can track inventory levels and automatically reorder items well before they run out, making costly disruptions a thing of the past.
The most sophisticated management systems provide an attractive combination of automatic resupply and full transparency throughout the supply chain. The result not only is increased efficiency and streamlined workflows, but also detailed data and new insights that can help lead to additional opportunities to further optimize internal logistics.
Tools and Technologies
Today, an emerging suite of inventory management solutions is helping OEMs and other automotive industry operators achieve right-size and right-time delivery. This ensures that needed parts are in stock and improves parts distribution and utilization within plants.
The range of sophisticated tools, technology and tactics that has been developed to help automotive manufacturers and suppliers make those things happen includes industrial vending machines and lockers, and weight-based bins. The latter use integrated sensing technology to monitor inventory levels by SKU and deliver automated alerts and reordering functionality that not only makes manual bin checks a thing of the past, but also eliminates the need for often-expensive “safety” stock.
In addition to ensuring that users will never run out of needed parts, the compact and customizable nature of this equipment allows configurations designed to minimize unnecessary travel time and deliver point-of-use efficiency. In other words: The parts you need can be stored and procured where they are needed.
Abandoning a central storage setup and keeping inventory close to workspaces and manufacturing lines is especially beneficial for the automotive industry, where specialization typically means only a handful of parts are being used in any one specific section of the plant.
Insights and Innovations
The hardware is only half of the equation, however. Perhaps the most exciting aspect of this new generation of smart inventory management is the vast amount of extraordinarily detailed data that these new tools produce – and, more importantly, what that data reveals about the people, parts and processes in and around manufacturing environments.
Data gathered by department or machine makes it possible for companies such as Motor City Industrial to reveal a kind of three-dimensional supply-chain map across the facility and the enterprise. This granular breakdown provides constant visibility throughout the supply chain. Consequently, users literally can see where slowdowns (and opportunities) exist. Information is available in real time, and reporting and analytics can be delivered daily, weekly or monthly.
Sophisticated analyses can identify consumption disparities, interdepartmental inconsistencies and other signs of correctable issues. Eliminating parts redundancies allows operators to use far fewer parts – streamlining, simplifying and saving money.
Every manufacturer is different, with their own issues and operational mechanics and organizational priorities. Therefore, customized process mapping – analyzing a manufacturer’s operations, inventory flow and parts need – is important. The right provider can determine not only what a manufacturer needs but also where their inefficiencies lie, and design an inventory-management strategy to address them.
Pre-deployment planning is particularly valuable at Tier One automotive suppliers, where larger facilities and higher volume introduce new complexities. The right plan can lead to right-sized inventory, reduced waste, new operational efficiencies and ultimately, greater productivity – with a meaningful bottom-line impact.
The best systems can reduce average parts consumption by 20% or more and decrease waste an additional 10%. A recent like-parts analysis for a Motor City Industrial customer identified redundancies that reduced 25 different parts down to just five.
Even better, the cost of designing and deploying these systems continues to drop, making this technology increasingly accessible. It’s a logical extension of the supply-chain optimization efforts that have been so impactful in recent years. By extending those gains into the factories and facilities themselves, the automotive industry can reach impressive new heights.
Joe Stephens is CEO of Motor City Industrial, a wholesale industrial supplier of fasteners, bearings and consumable products. Contact Joe at [email protected].
About the Author
You May Also Like