Suppliers on board: new roles, relationships chop costsSuppliers on board: new roles, relationships chop costs
Picture this: You're a big chemical company supplying thousands of gallons of paint to an auto assembly plant daily. One of the giant holding tanks has a leak. Do you care?Five years ago the answer was easy: "Heck no. That means I sell more paint!"But today is different. Now you care. At Chrysler Corp.'s St. Louis minivan plant and General Motors Corp.'s Moraine, OH, facility, you care an awful lot
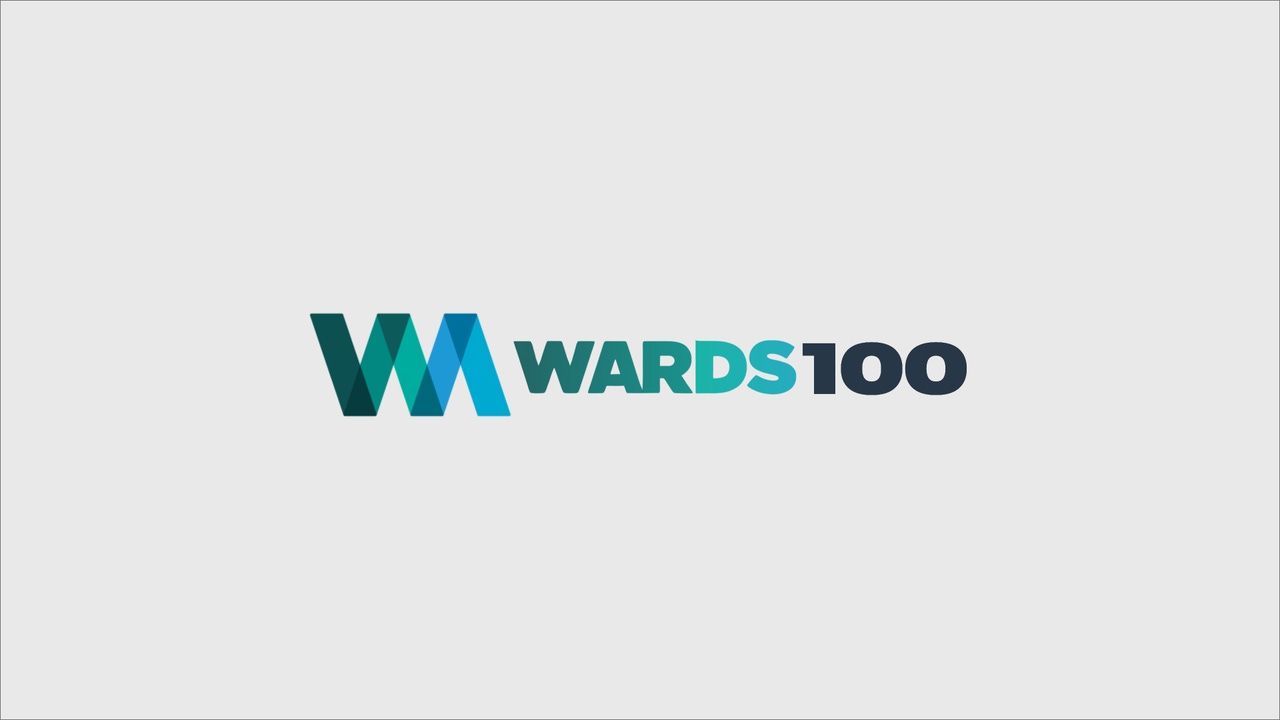
Picture this: You're a big chemical company supplying thousands of gallons of paint to an auto assembly plant daily. One of the giant holding tanks has a leak. Do you care?
Five years ago the answer was easy: "Heck no. That means I sell more paint!"
But today is different. Now you care. At Chrysler Corp.'s St. Louis minivan plant and General Motors Corp.'s Moraine, OH, facility, you care an awful lot -- not only about leaks, but waste of all kinds.
The difference is a concept called pay-per-build, and it's only one of several new innovations in OEM/supplier relationships that are pulling costs out of the supply chain without doing major damage to supplier profit margins. It's that "win/win" situation so often talked about but seldom achieved.
If you're a supplier of paint, tires, seats, instrument panels, interior trim parts or numerous other components, you get paid only for what goes on the car and out the factory door, not the parts that get dropped and ruined on the loading dock, not the screws that fall into a worker's pant cuffs, not the paint that leaks out of that holding tank. Typically a monitoring device is triggered after a vehicle passes a specific location on the assembly line (such as exiting the paint shop) and an electronic message is sent to the assembly plant's finance office and the supplier's account is credited with a sale.
"Now if somebody from PPG (Industries Inc.) sees a leaky paint line, they're the first ones to holler," Chrysler Corp. manufacturing chief Dennis Pawley joked last year during the launch of the new NS minivans at St. Louis. That's a bit of an exaggeration, but it shows how far traditionally adversarial relationships between the two sides have come in a very short time.
Who would think that in today's brutal economic environment, where vendors whine about being bludgeoned with price-cut demands and OEMs complain about being held "hostage" by suppliers who refuse to ship crucial raw materials if they don't get a price hike, that the two are happily exchanging workers?
In yet another surprising example of how traditional barriers have broken down between automakers and their suppliers, thousands of vendor employees go to work at automaker offices and factories every day. They have permanent desks, or they stand side-by-side with engineers and hourly employees on the plant floor.
Thomas T. Stallkamp, Chrysler executive vice president-procurement and supply, says about 600 supplier employees go to work every day at the Chrysler technical center in Auburn Hills, MI. Hundreds of others show up regularly, but don't have desks.
These are not "liaison" officers stationed on-site to hold hands with the customer and relay complaints to the home office. Most often they are engineers working shoulder-to-shoulder with Chrysler engineers and product managers, developing components and systems for new Chrysler vehicles.
The opposite is true, too: 75 GM engineers park their cars every day at Megatech Engineering Inc. in Warren, MI, where they work jointly with Megatech engineers on future versions of GM's midsize sedans. And a number of Ford Motor Co. engineers are located permanently at Siemens Automotive in Auburn Hills, where they are working on components for Ford's electric vehicle program.
In some cases, where watchful union locals agree, suppliers are even taking over the management of major assembly plant operations such as paint facilities. PPG employees are running the paint line at GM's Lordstown, OH, J-car plant, and DuPont engineers are running the GM Moraine paint shop.
"I think the (PPG/Lordstown deal) was a breakthrough," says GM purchasing chief Harold K. Kutner. "Not only did PPG come in and put a (paint) mix facility on our property, they participated in the investment of improving the paint facility. They manage our people and they have a productivity relationship with us in painting per cars. I think the cost of painting cars has gone down. The quality of the paint coming out of that plant has gone up. We need to drive more and more of these types of relationships."
Paint suppliers usually staff assembly plant paint shops with two to four experts to manage specific processes, points out John R. (Jack) Lewis, DuPont Automotive's worldwide director for OEM finishes. What makes Moraine's paint shop and a few others different is that there are about eight full-time DuPont staffers overseeing many other aspects of the process. High-volume automotive painting is so complex and requires such specialized knowledge that automakers increasingly are asking suppliers to take on more management responsibility rather than trying to train personnel themselves, Mr. Lewis says.
Because they are so steeped in the chemistry and technology of the painting process, supplier paint-shop managers also are better equipped to handle tricky model changeovers as well as switches from solvent- to water-base paint systems, Mr. Lewis adds.
Although the concept of supplier-run paint shops is catching on, the less-encompassing pay-per-build concept is taking off like a rocket. Ford already has implemented pay-per-build at most of its European paint plants, and North American facilities should be converted by mid-1997. Chrysler has converted about six paint plants and about six more are on the way. GM and transplant automakers also are in various stages of adopting the concept for paint and numerous other components.
The U.S. Big Three, Nissan Motor Mfg. Corp. and 15 Tier 1 suppliers currently are working with the Automotive Industry Action Group (AIAG), an industry trade group, to develop an electronic communications standard for pay-per-build setups. If all goes well, a data communications standard should be ready by the end of 1996. That should boost implementation, especially among smaller suppliers that currently cannot afford dedicated electronic communication links for each of their customers.
Despite the lack of standardization, the pay-per-build concept already is yielding huge benefits. "We've saved as much as a million dollars at one plant per year," says Don Venable, Chrysler sales manager for PPG Coatings and Resins.
"The most exciting thing about this program is they are really, truly interested in partnership programs. Our people in the plant have become like a team with Chrysler. They're not going after each other," he explains.
Instead, Mr. Venable says, both PPG and assembly plant employees are focused on wringing waste out of the entire painting process and getting the best possible finish at the lowest possible cost. Paint usage targets are set each year based on last year's figures. Any year-to-year cost savings are split evenly by PPG and the plant.
Some savings are achieved by tweaking the spraying process and using less paint per vehicle, but most of the big savings come from attacking waste, Mr. Venable says. For instance, Chrysler now tries to paint vehicles in big blocks of one color, instead of ad hoc. This limits the number of robot spray gun purging operations that have to be performed and the amount of paint and solvent wasted during the purging.
Another cost-saver: Red is by far the most expensive paint, and by assigning a specific part number to each paint color, an automaker will be charged extra for the exact number of red cars it produces. If red is less popular than predicted, the automaker saves money and the supplier at least breaks even. Before pay-per-build, the higher cost of the red paint was averaged into the cost of all the other colors, based on often unreliable sales forecasts.
But the biggest cost saver of all was when PPG found the leak. PPG engineers now routinely analyze and benchmark paint usage against other plants, and they found one facility using more than it should. A thorough investigation led them from the paint booths all the way back to the holding tank. A small leak turned into a big cost savings -- and money in the pockets of both OEM and supplier.
What's the next step? Already PPG is including the cost of sheet-metal cleaning chemicals and primers used to prepare the vehicle body for painting as part of the paint pay-per-build part number.
But DuPont's Mr. Lewis adds yet another twist. He says other materials applied in bulk form -- such as adhesives, sealants and sound deadeners -- might also be added to the pay-per-build concept, and perhaps to the same part number as the paint job -- even if they are produced by competitors.
"We used to make paint and leave it in the drum and come around once a month and collect our money," Mr. Lewis says. "Now, if we can manage this, by taking cost out of the system, we have helped ourselves."
Read more about:
2000About the Author
You May Also Like