December 11, 2013
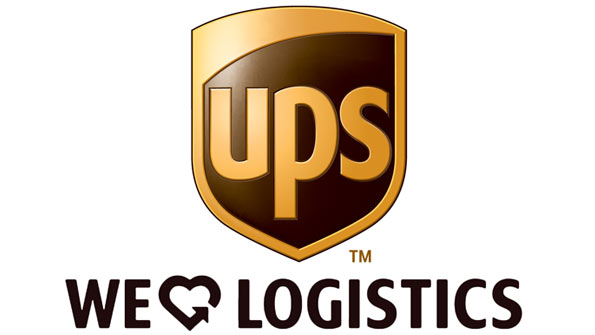
The Japanese earthquake and subsequent tsunami of May 2011 underscored the fragility of the worldwide automotive supply chain. The disasters temporarily closed plants that produced 17 of the top 20 models of Japanese vehicles sold in the U.S. and prompted General Motors to close a plant in Louisiana and a Peugeot plant in Europe, according to a Congressional Research Service study.
What makes the automotive supply chain so vulnerable to disruptions compared to other industries is its complexity. A typical motor vehicle has more than 15,000 parts, many of them coming to the U.S. from countries on the other side of the world. An outage, shortage or delay of any essential component can cause a production slowdown or a complete stoppage of assembly lines.
Currently, the global automotive supply chain is stretched tightly—brought on by a recovering economy that is fueling consumer demand, and an increasing number of new models slated for production.According to the Detroit Free Press, 2013 car sales are expected to exceed 15 million in the U.S. and as much as 85 million worldwide. A record 500 vehicle launches are expected by 2016. Adding to the problem is the fact that, during the 2008 downturn, many smaller suppliers closed or laid-off workers and reduced capacity.
Many are now reluctant to increase production capacity while they enjoy rising profits. Others, fearing a second downturn, are hesitant to increase capital expenditures. As the auto industry snaps back, the remaining suppliers struggle to fill orders.
All of this leaves little room for supply chain disruptions. The automotive supply chain is more delicate than it has been in recent memory. Preventing or mitigating disruptions has become even more crucial to the industry's well-being.
An APQC (American Productivity and Quality Center) study conducted in April 2013 revealed that 196 large companies surveyed were hit by an unexpected supply disruption during the last two years. The survey showed that the most common causes were natural disasters, such as tsunamis and floods, extreme weather such as droughts, and social turmoil such as riots and civil wars. While companies can prepare for such situations, other disruptors may not fall so neatly into the 'expected' category but can be just as devastating.
NEXT: Five out-of-the-ordinary scenarios and what can be done to prepare for them when possible or mitigate their effects after the event. Download the full white paper after answering the brief questions below.
You May Also Like