June 1, 2015
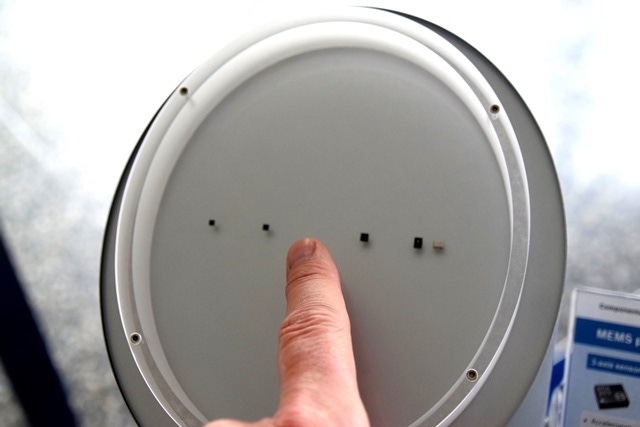
REUTLINGEN, Germany – Five years ago, Robert Bosch invested €600 million ($652 million) in a second electronics plant to fabricate wafers of microchips, arrayed edge to edge and then cut with a saw and used in vehicles, smartphones, laptops and other electronic devices.
It was the largest single investment in Bosch’s history.
When Bosch opens a new R&D lab in Renningen, Germany, later this year, the pricetag is expected to fall short of the 5-year-old “wafer fab” plant. The capital investment there was massive but justified because it has helped cement Bosch’s place in the booming semiconductor market.
Consider this: The state-of-the-art complex has manufactured 5 billion highly intelligent micro-mechanical systems sensors since 1995, and every single chip on every wafer undergoes rigorous and redundant quality checks 24 hours a day seven days a week, to ensure a bad one never leaves the plant.
The defect rate is impressive – fewer than five for every 1 million produced – but the staggering volume explains why air in the temperature-controlled plant and testing labs is constantly filtered and recycled and why employees practically wear Hazmat suits to contain stray hairs and ensure a static-free and dustless environment.
A contaminated microchip is good to no one.
Defective chips are identified with the help of 125 automated test cells, each one costing €700,000 ($761,505), and Bosch is expanding the testing operations here, which will cost even more money.
This may sound like a wildly expensive process for production and testing that must struggle to break even from quarter to quarter.
Bosch declines to discuss profitability of specific products, but it’s worth noting every single chip and sensor produced here has a customer waiting to install it in a vehicle stability-control system, video game or a hand-held device, among other applications. Those customers will pay between €0.20 and €10 ($0.22 and $10.87) for each one.
The average price paid for a MEMS sensor is €0.92 ($1), so the arithmetic is fairly simple given the plant’s output in 2014 of more than 1.3 billion MEMS sensors. That’s close to €1.19 billion ($1.3 billion) in annual revenue from one plant for one product.
The real money is spent on automotive-grade MEMS sensors, which have stricter specifications, used as airbag accelerometers and to monitor or facilitate functions such as tire pressure, cabin temperature and navigation.
Every one of those automotive sensors fetches between €6.43 and €9.19 ($7 and $10). The sizable investments, it seems, pay for themselves.
Every time you rotate your smartphone for a widescreen view of a photo, it’s a MEMS sensor that does the job. These sensors have become ubiquitous in today’s electronics-driven world.
50 MEMS Sensors Per Vehicle
Installation rates of MEMS sensors in vehicles only will rise as tailpipe-emission requirements ratchet up globally and intensify the need for powertrain sensors designed to measure variables such as airflow, oxygen levels, atmospheric pressure and knock.
Vehicles today have at least 50 MEMS sensors, which also can act as microphones and measure rotational yaw rate. The chip often is smaller than the head of a match, but the circuitry etched inside is so finely structured it is as wide as five or six human hairs. One chip can inflate up to 16 airbags.
Bosch makes 4 million of these sensors every day, and 75% of output is for consumer electronics.
These “sensory organs” are becoming even more intelligent. This year, Bosch unveiled the world’s first environmental sensor capable of measuring air pressure, moisture levels, ambient temperature and air quality, all in a single housing. Soon, these sensors will be communicating with each other.
French market research company Yole Développement predicts the global market for MEMS, across multiple industries, will grow from $12 billion this year to $21 billion by 2020.
Yole pegs Bosch as the No.1 MEMS producer worldwide. With its sector revenues up 20%, Bosch is considered a “titan with momentum,” according to a recent Yole report.
The complex here employs 7,000 people (up from 6,400 four years ago), including 800 people in the new wafer-fab plant.
Another innovation is in the works here. Bosch’s first electronics plant, beginning in 1994, produced chips on 150-mm (6-in.) silicon wafers. The second plant migrated to 200-mm (8-in. wafers) with room for more and larger chips.
Today, the complex is testing the feasibility of fabricating 300-mm (12-in.) wafers for application-specific integrated circuits to process information passed along by the MEMS sensors.
Handling a wafer the size of a small pizza requires a delicate touch and unique tools because it is prone to warp or bow. If the challenges can be overcome, plant engineers expect production of 300-mm wafers to begin within two years.
Read more about:
BoschYou May Also Like