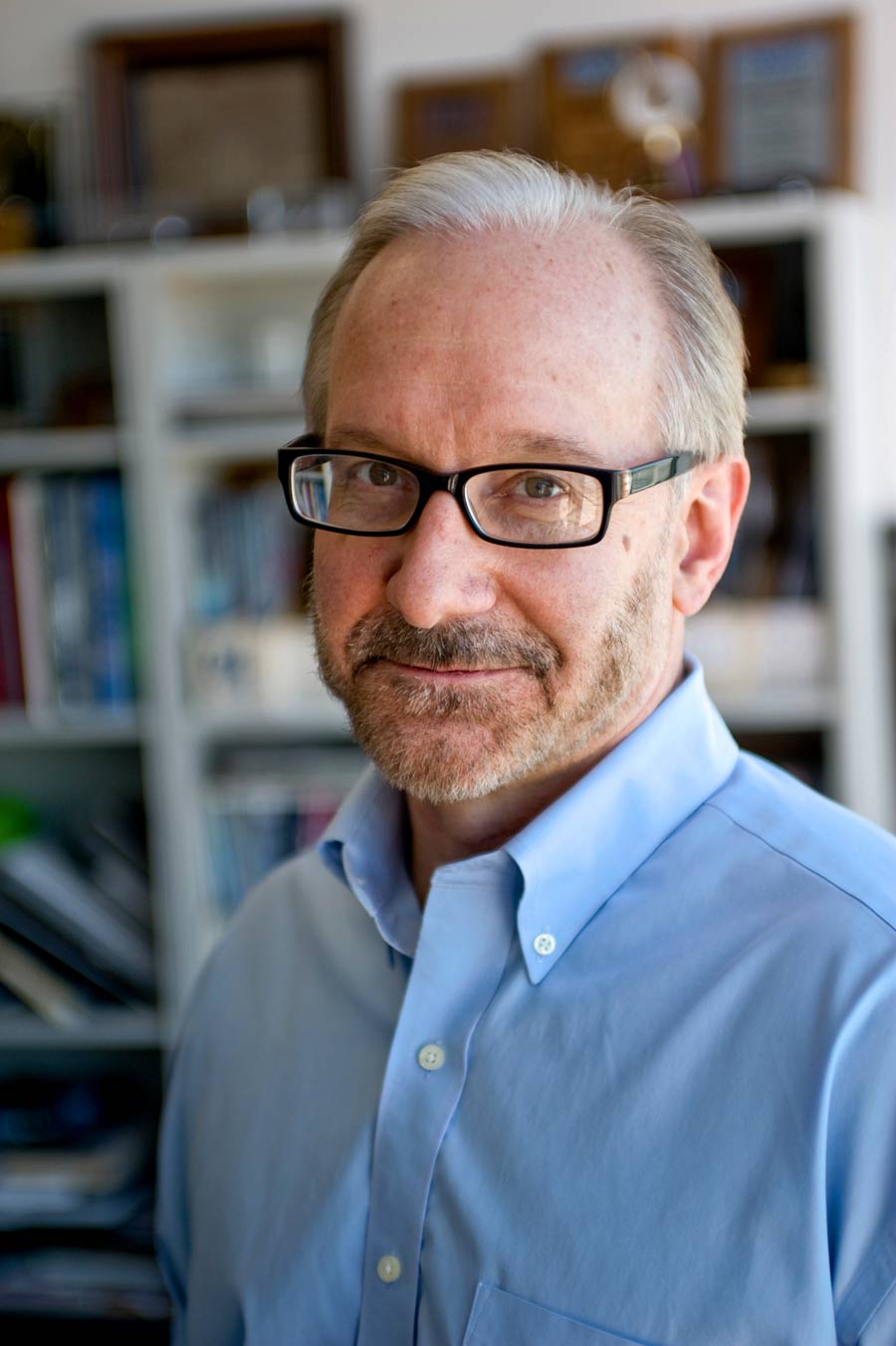
Surprisingly strong new-vehicle sales in August, the best since 2003, have renewed speculation about whether suppliers finally will start an expansion binge to keep up with ever-increasing vehicle production.
According to WardsAuto’s latest forecast, 2014 North American car and truck production is likely to near 17 million units for only the third time in history, just five years after falling to its lowest level in the past 29 years. Light-vehicle production is expected to gradually increase to 18 million units during the next several years.
Anecdotally, it appears ever-cautious suppliers finally have decided to loosen the purse strings and increase capacity, spending tens of millions of dollars on new factories, tech centers and headquarters buildings.
In the last several months, numerous suppliers have announced new expansions in suburban Detroit and elsewhere in the U.S. aimed at serving the growing North American vehicle market.
But a closer look reveals most are investing in new products and technological capabilities, not new bricks and mortar to keep up with increasing vehicle production.
To name a few, Robert Bosch just broke ground on a $40 million tech center expansion in Plymouth Township, MI. Faurecia opened a $30 million headquarters in Auburn Hills, MI. Continental announced a $150 million expansion of its facility in Newport News, VA.
With its tech center project, Bosch is aiming to beef up its presence in key technology areas such as stop/start systems, cyber security and self-driving vehicles. The new facility also will consolidate operations currently in separate locations.
Faurecia’s new building also is designed to pull together activities, such as seating operations, that had been taking place in several locations.
In addition to administrative space and specialized training areas, the building includes a prototype metal shop; trim development lab; just-in-time manufacturing lab; structural testing lab; environmental testing chambers; noise, vibration and harshness and electrical labs; and a semi-anechoic chamber for sound testing.
Continental is expanding its manufacturing operations in Virginia to launch production of a new turbocharger and increase production of its gasoline high-pressure injector, fuel-rail and -pump assembly lines.
But aside from these kinds of tech and administrative expansions, suppliers seem content to run most of their everyday manufacturing operations seven days a week on three shifts if necessary to meet growing customer volume demands, remaining reluctant to build new plants.
They have good reason to be wary. While the U.S. sales outlook is sunnier now than it has been in a decade, pessimists already are saying recent growth is being driven too much by incentives and cheap credit.
What’s more, history tells us that global political unrest or a sudden spike in fuel prices can put the brakes on sales momentum in a heartbeat.
More than 60 of the industry’s biggest suppliers went bankrupt during the last downturn, taking countless smaller suppliers down with them, in large part because they were stuck with too much capacity when NA light-vehicle production bottomed out at a horrific 8.7 million units.
Even when running near 100% capacity, auto supplier margins are razor thin, so investing millions in new construction based on OEM sales projections and economic forecasts takes a major leap of faith.
And if a capacity expansion should turn into a big money maker, a supplier can only count on a few good quarters before automaker customers start suggesting it “share the wealth” and ask for price cuts, a direction recently hinted at by Fiat Chrysler Automobiles CEO Sergio Marchionne.
No wonder, then, that suppliers are choosing to invest more in new technologies than in general capacity expansion. They are not being overly cautious, they are just being wise.
Read more about:
2014About the Author
You May Also Like