Desktop 3D Printers Streamlining Auto ProductionDesktop 3D Printers Streamlining Auto Production
Take Volkswagen Autoeuropa as an example. The company turned to desktop 3D printers to create custom tools, jigs and fixtures used in the auto-manufacturing process in just one plant – and reports cost savings in the 90% range.
November 3, 2017
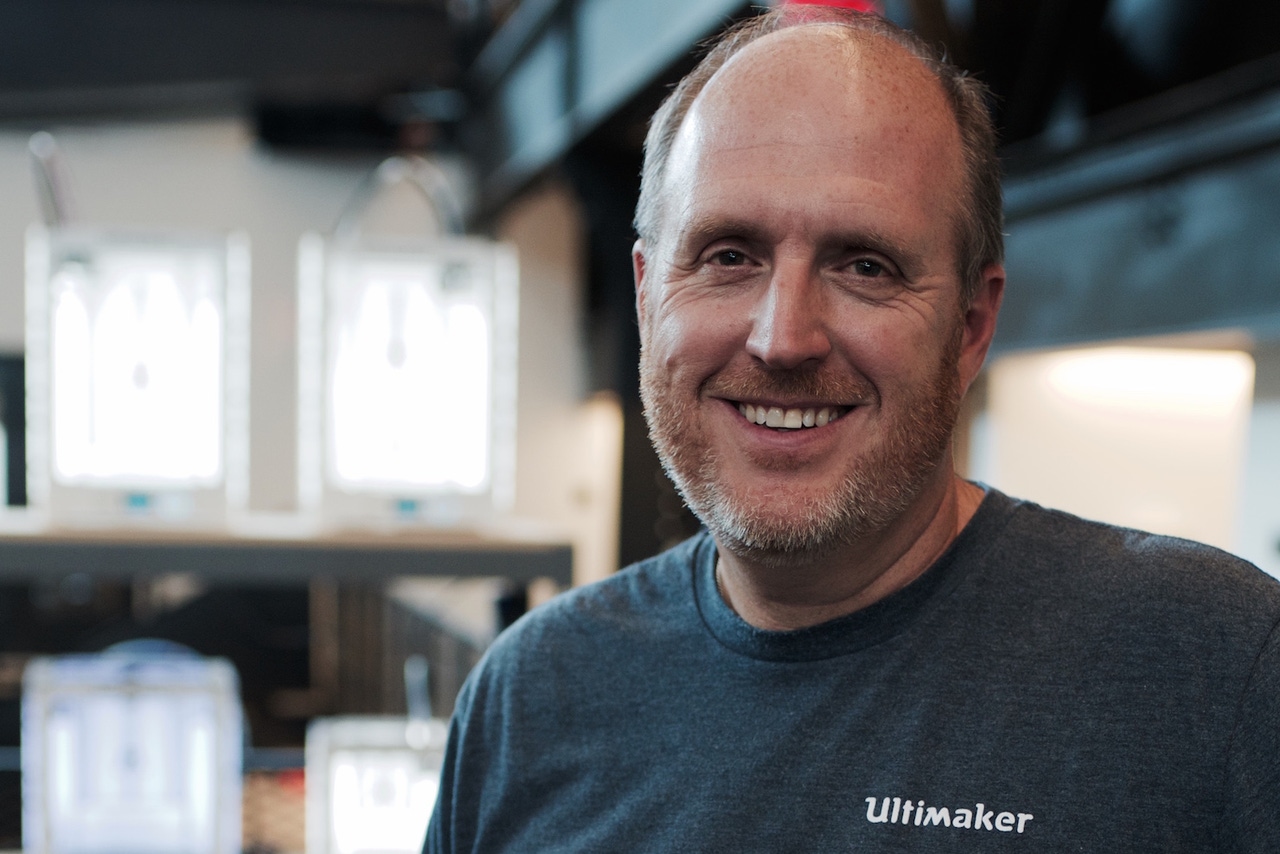
3D printing has been making waves in the automotive manufacturing industry for years, but innovation has gone into overdrive in recent months.
New printers are being announced left and right. 3D printing is reportedly entrenched at Ford. Hyundai recently announced a new design center fully equipped with 3D printers and meant to cut design cycles in half. A top official with the U.S. Department of Energy’s Oak Ridge National Laboratory recently predicted 3D printing’s potential to reduce the price tag of developing an entirely new vehicle from $600 million today to just $60 million.
Most of the hype, however, continues to center on industrial-sized machines and their promise of producing fully functional car parts, or even complete cars. But there’s another piece to the 3D printing puzzle that’s far less talked about, yet equally impactful: desktop printers.
Desktop 3D printers streamline the production process and introduce a whole new level of accessibility and efficiency to auto manufacturing that’s saving companies significant time and money. Take Volkswagen Autoeuropa as an example. The company turned to desktop printers to create custom tools, jigs and fixtures used in the auto-manufacturing process in just one plant – and reports cost savings in the 90% range.
So what is it about these printers – often costing no more than $5,000 – that is making such an impact on the manufacturing process?
One main reason is the general nature of automotive manufacturing. Hundreds of engineers design one car and they are all very specialized. A few engineers might work solely on a wiper blade, for instance. In a traditional setting, manufacturers had a centralized 3D printing room often located away from where the actual product or design process happened. Access was limited and therefore, so was the experimentation needed for efficient, innovative design.
Now, as desktop 3D printers become more advanced and precise, offering professional-grade print quality and a variety of cutting-edge materials, the technology has become a staple in most automotive manufacturing and design settings. Instead of 250 engineers using a centralized location as in the past, now there might be 25 desktop printers that are ready at an engineer’s beck and call. People are printing more, collaborating more effectively and turning around designs faster.
To understand the potential financial impact of these newfound efficiencies, my team at Ultimaker recently sought to answer: What exactly is an automotive minute worth? After crunching numbers from public data sets available from the U.S. Bureau of Labor Statistics, we found that the cost of automotive manufacturing in the U.S. is $460,706 per minute or $1,110,663,840 per week.
This means even the slightest improvements in efficiency can introduce major savings for the manufacturer – in regard to both time and cost – that greatly influence the company’s bottom line. It’s exactly what we saw with the Volkswagen Autoeuropa example.
Whether used standalone or in tandem with industrial-sized machines, desktop 3D printing has become the quiet driver of innovation in the automotive world for tooling, prototyping and even functional parts. Automakers benefit from the efficiency and accessibility provided by desktop printers, and with advancements being made every year, only time will tell just how much of a long-term effect the technology will have on the industry.
John Kawola is president of Ultimaker North America. He is a passionate 3D printing evangelist with over 10 years of experience in the industry. Prior to his role at Ultimaker, John served as CEO and president of Z Corporation, CEO of Harvest Automation and Board Director at SpaceClaim.
About the Author
You May Also Like