GDI, Zero-Emission Tanks Drive Growth
Freshly reorganized, nearly debt-free and sporting a new brand identity, Britain's TI Automotive is emerging as an auto supplier well positioned to cultivate its core sectors of fuel tanks and tubing, while exploring new opportunities in products such as gasoline direct injection. TI previously had been organized into two groups dedicated to plastic blow-molded fuel tanks and rubber and steel tubes
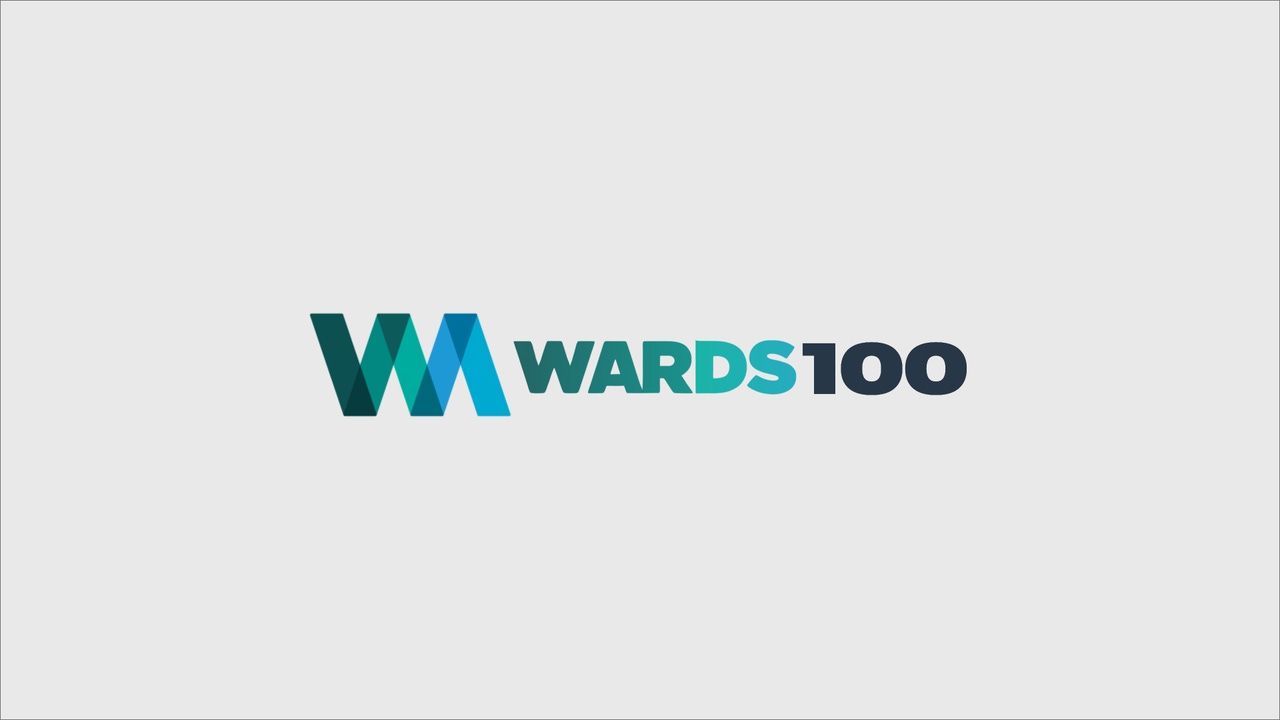
Freshly reorganized, nearly debt-free and sporting a new brand identity, Britain's TI Automotive is emerging as an auto supplier well positioned to cultivate its core sectors of fuel tanks and tubing, while exploring new opportunities in products such as gasoline direct injection.
TI previously had been organized into two groups dedicated to plastic blow-molded fuel tanks and rubber and steel tubes to transport brake fluids to the wheels and fuel from the tank to the engine.
In December, the supplier completed a restructuring that creates five divisions: fuel tanks; fuel pumps and modules; heating, ventilation and air-conditioning components and systems; powertrain; and brake and fuel lines.
Chairman, President and CEO Bill Kozyra is confident the new company, focused on innovative new lightweight technologies to boost fuel efficiency, will prosper in an industry coping with lower production volumes.
The U.K.-based TI in November entered into the process known as the scheme of arrangement to change its legal structure. It's not the same as bankruptcy in the U.S.
“It's a sort of consensual restructuring of your balance sheet, where your lenders agree in advance of filing with the court to convert your debt to equity,” Kozyra tells Ward's.
“It requires more than 75% of your lenders by value or 50% by number. We had actually both when we filed,” he says. “Usually the judge gives 30 to 45 days for a minority to voice concerns about this activity. In our case, we had no objections from any lenders.”
As part of the restructuring, the privately held TI successfully converted more than 90% of its debt to equity.
“So our lenders are now shareholders in the company,” Kozyra says. Two shareholders controlled the old company. Today, about 20 shareholders are in charge.
Since arriving at TI (from the U.S. arm of Continental AG) in June 2008, Kozyra has been working to cut the company's cost structure. At one point, the supplier had 17,000 employees; today it has about 14,000. It also has 123 facilities worldwide, down from 130.
“We will likely be in a position to make some consolidation activities in North America, but those plans are still in the review stage,” he says.
Downsizing allowed TI in 2009 to post a modest profit. “We went from basically burning cash at the old industry volumes to today not burning cash at the reduced industry volumes,” Kozyra says.
TI does 55% of its business in Europe, 25% in Asia/Pacific and 20% in North America. “I'd like to grow North America back to a stronger position, where roots of the company are,” he says.
In the 1990s, TI purchased Bundy Tubing, a U.S. company founded in 1919 by Harry Bunding. It then went on to acquire plastic-tank producer Walbro Corp. in 1999.
Walbro helped advance the trend of plastic fuel tanks, which were supposed to completely replace steel tanks years ago. But steel tanks got lighter and more efficient and became relevant once again to accommodate the higher pressures required in gas-electric hybrids.
“We've now introduced a pressurized plastic tank that ‘obsoletes’ steel once again,” Kozyra says of TI's zero-emission gas tank, an industry first.
The tank is intended to minimize hydrocarbon emissions that result from the vaporization of fuel. A decade ago, fuel tanks were allowed to emit 2,500 mg of hydrocarbons in a 24-hour period. Five years ago, the limit was about 250 mg. Today's Partial Zero Emission Vehicle mandate is 54 mg.
TI's new tank emits less than 10 mg of hydrocarbons, thanks to the company's Tank Advanced Process Technology to create a nearly air-tight seal.
The tank is blow-molded, then cut open while the material remains pliable. A carrier with several components normally located outside is inserted into the fuel tank.
The mold is then closed again, and the seam is hermetically sealed with a process patented by TI, mechanically fusing the carrier to the tank. The entire process takes less than a minute.
In the past, a plastic tank could be made as two halves and the components placed inside before it was sealed. “But you can't get a perfect seal,” Kozyra says. “You still had a huge leak path for hydrocarbons.”
The new tank also limits emissions by having only one opening, rather than four or five as in the past.
TI is the world's third-largest tank producer, with about 15% of the market, behind the Kautex division of Textron Inc. and Inergy Automotive Systems.
TI has the No.1 position in brake and fuel lines, with about 40% of the global market, Kozyra says. “We've been able to maintain that leading position for the life of the company,” he says.
As part of a new powertrain strategy, TI has targeted gasoline direct injection with a new lightweight fuel-delivery system that includes the high-pressure rail to the injectors.
“Right now that business is exploding,” he says. In the past, TI only delivered fuel from the tank to the high-pressure pump. TI's approach is to produce the rail from coated steel, instead of stainless steel, saving weight and cost.
The first contract is in South Korea for Hyundai Motor Co. Ltd.'s all-new 2.4L Theta II DI 4-cyl. in the '11 Sonata sedan. TI is at the application stage with three other prospects and has quoted GDI programs for six other customers in Korea and the U.S.
TI's outlook for GDI business is “significant enough that we have more opportunities for new programs to design and develop them than we have engineers to work on them,” Kozyra says.
TI's only plant for these high-pressure rails is in Korea, but he expects one also in North America and another in Europe. He expects to be producing rails for up to 10 vehicle platforms within five years.
“This could be a major source of additional new revenue for TI Automotive,” adding about £200 million ($300 million) annually to the company's revenue stream, which now totals £1.2 billion ($1.8 billion) annually, he says.
Kozyra is banking on GDI as a technology with a bright future long term.
“In this country, GDI is going to be huge in a majority part of the market,” he says. “Diesels will only go so far; hybrids and EVs will only go so far. Gasoline powertrains will still be the primary mode of propulsion in this country. We're excited to be able to support that growing technology.”
TI is not producing high-pressure pumps at this time, “but that's a possibility as we look at the entire portfolio,” Kozyra says.
Read more about:
2010About the Author
You May Also Like