SPE Names WinnersSPE Names Winners
Paint is both the most important vehicle and the bane of the auto industry's existence. A great paint job sells vehicles, but the painting process is the most expensive and difficult aspect of building a car. Eliminating paint and its attendant environmental issues, from controlling hazardous paint-plant emissions to disposing of used paint sludge is the holy grail of automotive manufacturing. If
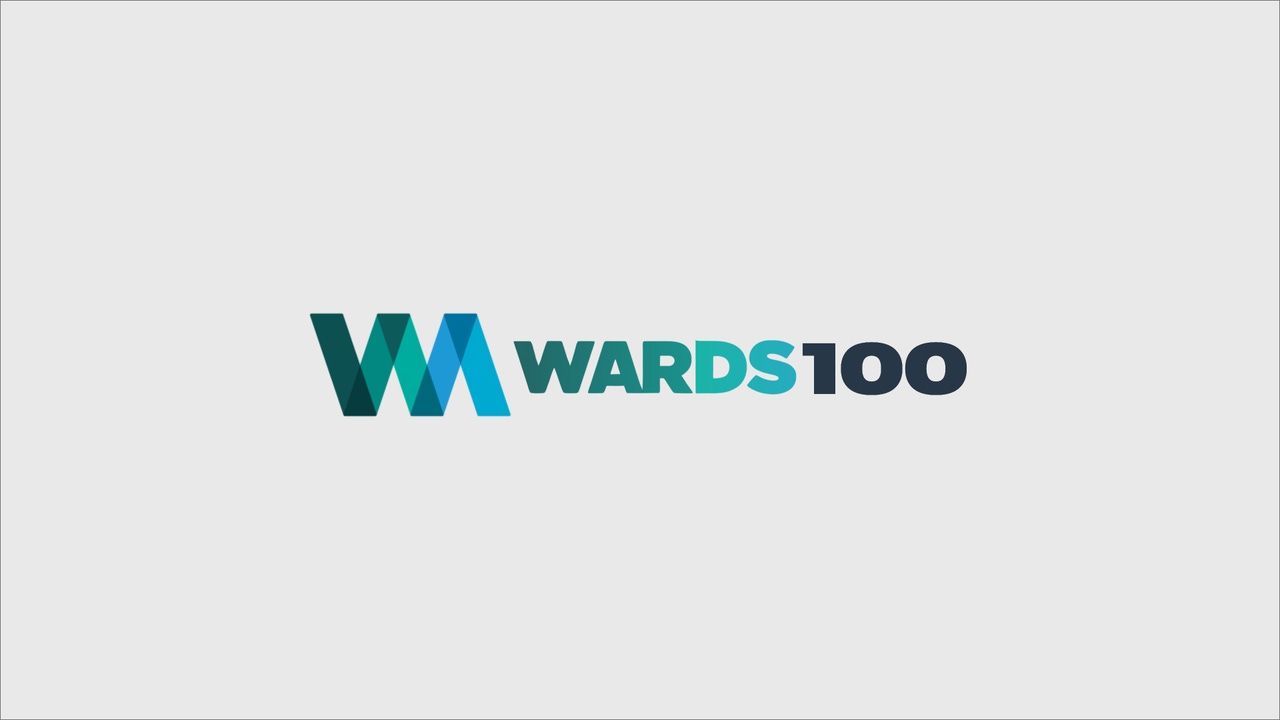
Paint is both the most important vehicle “component” and the bane of the auto industry's existence. A great paint job sells vehicles, but the painting process is the most expensive and difficult aspect of building a car.
Eliminating paint — and its attendant environmental issues, from controlling hazardous paint-plant emissions to disposing of used paint sludge — is the holy grail of automotive manufacturing. If it ever is accomplished on a major scale, it has the potential to save auto makers billions and untold benefits for the environment.
Working with suppliers ArvinMeritor Inc. and GE Plastics, DaimlerChrysler AG's Smart brand is taking the industry one step closer with the development of a glossy, beautiful — and unpainted — roof module on the '03 Smart Roadster.
The component won the prestigious Grand Award from the Automotive Division of the Society of Plastics Engineers (SPE) International at the recent 33rd annual SPE Innovations Awards Program in Livonia, MI, in addition to winning the Body Exterior category.
Each year, a panel of judges comprised of independent automotive and plastics industry experts, journalists and analysts (including a Ward's editor) select the winners from 35 entries in five different vehicle categories.
The Smart Roadster roof module also is more than 50% lighter than a painted steel roof system, but it was the perfect, high-gloss finish that most impresses judges. Produced using a polycarbonate copolymer film, it has a top-quality, Class A finish that will stand up to the elements for 10 years without losing its shine. That makes it truly competitive with conventional painted steel.
Other winners:
Body Interior: Instrument panel lower carrier on General Motors Corp.'s '04 fullsize trucks. Component supplier: Delphi Corp.; materials supplier: Spartech Corp.'s Spartech-Polycom. The substitution of a resin that costs 43% less, while still using existing tooling and equipment highlighted this innovation. Engineers found a much less expensive material, namely a low-cost filled homopolymer polypropylene plastic, to do the job of the plastic traditionally used in this application, called a filled SMA.
Materials (2-way tie): Underbody shield on '04 BMW 5-Series sedan; component supplier: Seeber KG; Materials supplier: Quadrant Plastic Composites AG; And the load floor on the '03 Renault Megane; component supplier: InoPlastic Omnium; Materials supplier: MCR Composites.
The big underbody panel on the new 5-Series won kudos because it demonstrated variable stiffness and density values within the panel, when needed, without added mass or volume. It also produced a weight savings of 30% compared with a similar glass reinforced polypropylene compression-molded or injection-molded part.
Judges liked the BMW underbody shield, but they also were so impressed with the load floor on the Renault Megane that they couldn't pick between the two, even after several re-votes, ending in a dead heat. The Megane part distinguished itself by being large, strong and light — and offering part-to-part cycle times of 60 seconds.
Powertrain: Continuously variable intake manifold for the BMW 4.4L V-8; component supplier: Pierburg GmbH; materials supplier: Vyncolit NV. The world's first continuously variable intake manifold using a glass-fiber-reinforced phenolic plastic to mold complex geometries of the functioning elements. It also is 20% to 25% lighter than a comparable aluminum intake manifold.
Process/Enabling Technologies: instrument panel on '03 Mazda6. Component supplier: Intertec Systems; Materials supplier: Basell (retainer)/PolyOne (skin). The new IP on the Mazda6 sedan features an extrusion process for an automotive trim strip that enables in-line forming for both ends of molding. The process yielded a cost savings of over 10% compared with an extruded/injection-molded part.
SPE also recognized Robert Schad, CEO of Husky Injection Molding Systems Ltd., as the 2003 Executive Leadership Achievement Award winner for his contributions to the automotive and plastics industry. Schad founded Husky and led its emergence as the world's largest brand-name supplier of injection-molding equipment to the plastics industry.
Read more about:
2004About the Author
You May Also Like