Toyoda: We Couldn't Keep Up With Growth
The speed at which Toyota’s volume grew last decade exceeded its hiring and training of workers, the auto maker's top official says.
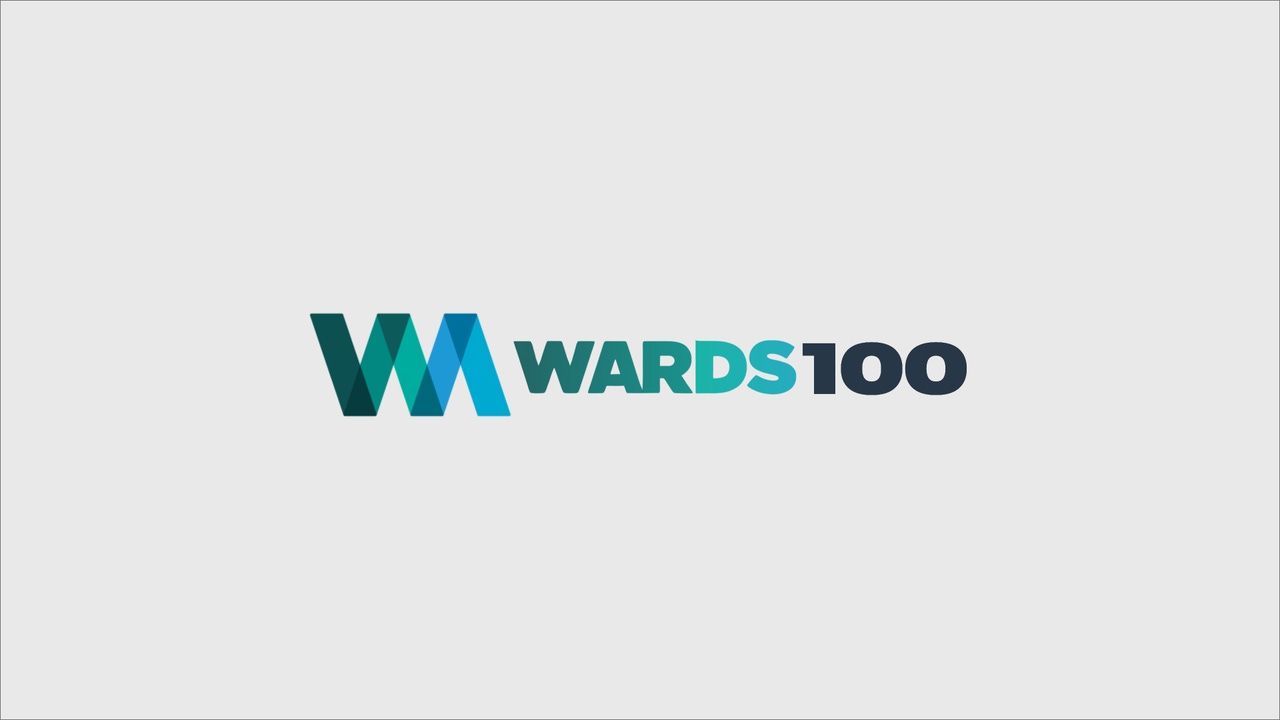
Special Coverage
North American Int’l Auto Show

DETROIT – Toyota Motor Corp. CEO Akio Toyoda says understaffing was a key reason why the auto maker has experienced a raft of quality issues in recent years.
Speaking to select media on the sidelines of the North American International Auto Show here, Toyoda says the speed at which Toyota's volume grew in the last decade exceeded its hiring and training of workers.
Now Toyota is making "very focused efforts" to nurture the human-resources side of its business, the son of the company founder says on his first visit to the Detroit auto show.
Jim Lentz, president-Toyota Motor Sales U.S.A. Inc., admits Toyota didn't listen as well as it could have to its customers, who were bringing quality issues to its attention before the auto maker recalled millions of vehicles last year amid allegations of unintended acceleration.
Also lacking was communication between American and Japanese officials, he says.
Now Toyota's system is "more robust" to identify and remedy quality issues, thanks largely to a greater number of high-ranking Americans within the company. "We are now involved in the recall decision process," Lentz says of the change.
Additionally, Toyota today has three American chief engineers and all but one of its U.S. plants have an American at the helm, Steve St. Angelo, Toyota's chief quality officer for North America, says of the Americanization of the auto maker’s ranks.
Toyota CEO Akio Toyoda
Toyota also has the ability to monitor blogs to look for quality issues customers are having.
Perhaps most importantly, recalls now are a "consensus decision" between American and Japanese officials.
Toyota last weekend announced it was establishing a Collaborative Research Safety Center at its Toyota Technical Center campus in Ann Arbor, MI.
Working in step with outside firms, Toyota engineers from the U.S. and Japan will tackles a variety of issues, including reducing the risk of driver distraction and how to better protect children, teenagers and senior citizens in crashes.
St. Angelo also addressed unionization of Toyota's plants, as the United Auto Workers union continues to make known its intentions to try to organize Toyota's U.S. plants.
"I've not personally seen their principles, but Toyota has its own set of principles that have worked well for us," St. Angelo says. "We live by them."
He notes life is good for Toyota's hourly U.S. manufacturing workers.
For example, during the recession, when Toyota had to idle its Princeton, IN, and San Antonio, TX, light-truck plants for three months, it continued to pay workers instead of laying them off. “(That) cost hundreds of millions (of dollars)," St. Angelo says.
Read more about:
2011About the Author
You May Also Like