Motomachi marvel: RAV4 utilizes new Toyota production systemMotomachi marvel: RAV4 utilizes new Toyota production system
NAGOYA, Japan--Just when its gasping competitors think they're catching up with Toyota Motor Corp., the world's leanest automaker gets its second wind, kicks out and sets a new pace.Kaizen, the Japanese term for continuous improvement, is the guiding principle in Toyota's tireless chase to make better vehicles--and better conditions for workers.Nowhere is that philosophy more evident than at Toyota's
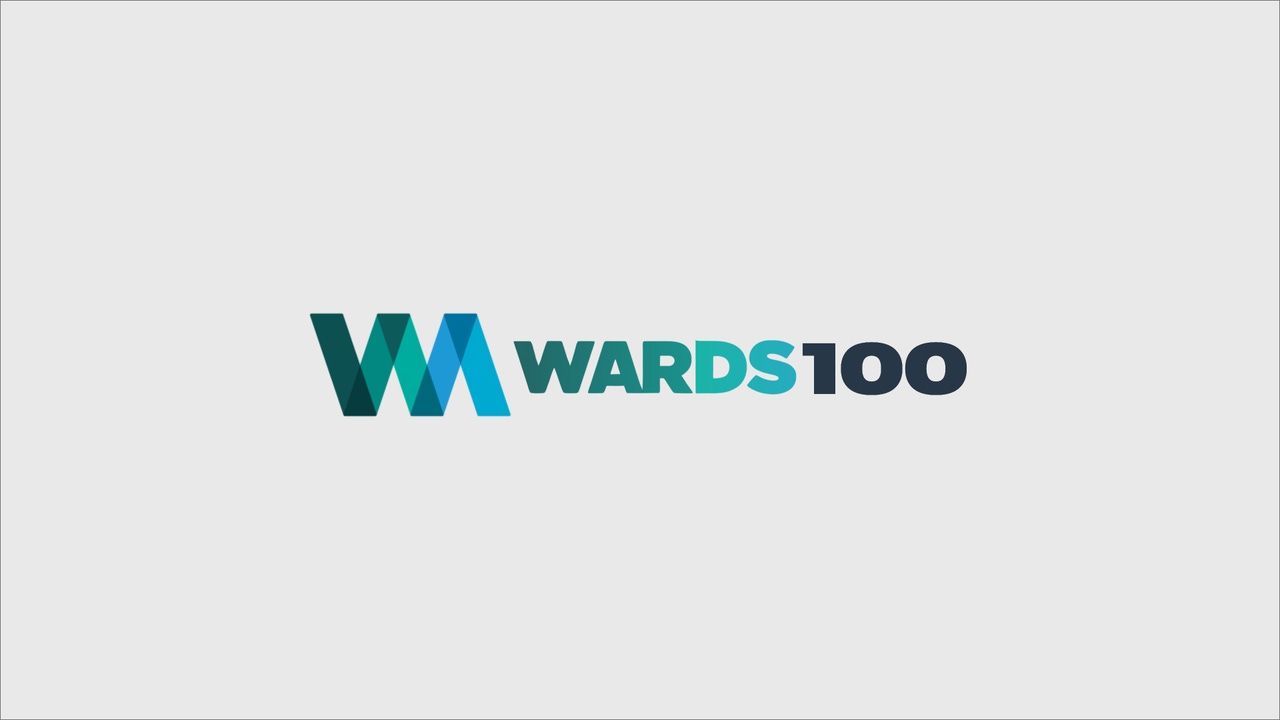
NAGOYA, Japan--Just when its gasping competitors think they're catching up with Toyota Motor Corp., the world's leanest automaker gets its second wind, kicks out and sets a new pace.
Kaizen, the Japanese term for continuous improvement, is the guiding principle in Toyota's tireless chase to make better vehicles--and better conditions for workers.
Nowhere is that philosophy more evident than at Toyota's Motomachi plant, where its RAV4 sport/utility vehicle (SUV) has been produced since April 1994. RAV4, which stands for "recreational active-vehicle with 4-wheel-drive," has since become a big hit here and in the U.S., where it was introduced in February (see main story).
Although the little SUV is getting rave reviews, far less is known about the new twists to Toyota's vaunted production system that were adopted at Motomachi No. 2 Assembly Line before the RAV4 launch.
To start with, RAV4 borrows about 40% of its components from existing Toyota models, chiefly cars. That not only saves money by expanding component volumes, it also reduces assembly complexity.
But there's more to the story than that. The Motomachi complex dates to 1959. When it came time to convert the No. 2 line to RAV4 production in the early '90s, kaizen kicked in bigtime.
Under the guidance of Executive Vice President Toshimi Onishi, Toyota's worldwide production chief, the No. 2 line's layout was divided into five segments, each with small buffers--yes inventories--so that work can be stopped in any of the five without impacting the work-flow elsewhere. "In other words, we can resolve problems on one segment without shutting down the whole line," says Mr. Onishi.
Next, work was consolidated within specific areas such as wiring harnesses, with workers empowered to seek improvements. To improve the plant's ambience, Toyota moved "noisy work" such as water and dynomometer testing to an adjacent building, making the assembly plant quieter and roomier.
The plant's key enhancement, however, comes from refinements in the so-called "Toyota Verification of Assembly Line," or TVAL, says Mr. Onishi. TVAL measures the burden of each assembly task and helps identify elements within those burdens. "For example, a big factor on the trim line is the awkward posture an employee assumes to install items in the car," he says, while the weight of components is a major consideration for folks working on the chassis line.
Toyota concluded that workers work better with simple processes and equipment that they actually can see and maintain themselves. That meant putting the equipment "right into the flow of the line where the employees are working," says Mr. Onishi. "In place of complex automation, we have equipped our systems with simple mechanical actuators and sequential control features."
Not that the No. 2 line is old-fashioned. All manner of simple, yet common-sense, systems are employed including: automatic engine-mount tightening; component-delivery via trolleys; workers and necessary tools ride with the vehicles on conveyors as they move down the line automatic loading of fully built-: up front suspension systems; gravity-feed of certain parts to the line; and installation of seats, instrument panels and steering wheel / column and headliner modules without having to bend over or into the vehicles.
There's much more, such as automatic: attachment of the wheel/tire assemblies to the hubs and automatic filling of the engine coolant and HVAC systems. Summed up`: the TVAL enhancements reduced assembly line space by 40% and lowered Toyota's investment in the new line by 40% vs. what it would have required for heavy automation, says Mr. Onishi.
Don't be surprised if Toyota duplicates its success at Motomachi No. 2 when its new pickup truck plant begins production up in Princeton, IN, in 1998 (see Auto Talk, p. 21). Mr. Onishi acknowledges that that's a strong possibility.
About the Author
You May Also Like