Toyota Mixing Materials for Strength, StiffnessToyota Mixing Materials for Strength, Stiffness
Using ultra-high-strength steel can save 88 lbs. on a typical body, and adding aluminum can double that to 187 lbs. But the last improvement comes from the carbon-fiber panels, the automaker finds.
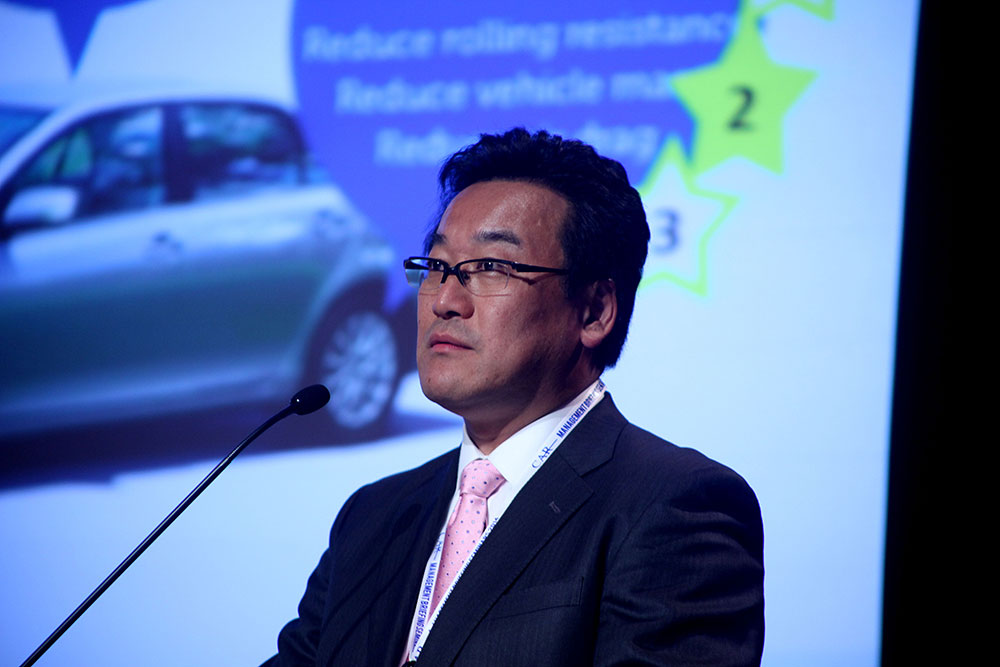
TRAVERSE CITY, MI – Mixing materials is the only way to save 220 lbs. (100 kg) on a body-in-white, says Toyota’s Takefumi Shiga, division general manager of the No.1 Body Engineering Div.
Using ultra-high-strength steel can save 88 lbs. (40 kg) on a typical body, and adding aluminum can double that to 187 lbs. (85 kg). But the last improvement comes from the carbon-fiber panels.
Shiga says Toyota studied materials for strength and stiffness and found that for frame parts, carbon fiber is a clear leader for strength. However, there is no runaway favorite for stiffness.
For closure panels, carbon fiber and aluminum stand out for both stiffness and strength.
The Lexus RC F coupe, introduced at the North American International Auto Show in January, uses a mixture of different materials, including carbon-fiber panels on the hood, roof and rear wing.

Lexus RC F coupe uses a mixture of materials, including carbon fiber on hood, roof and rear wing.
Toyota has developed different processes to handle the material mix. Some RC F buyers want the external look of carbon fiber, and that outer skin is made with a resin transfer-molding method developed by Toyota.
Shiga does not say how fast it is, but the process allows higher production speeds than that used for the first Toyota employing carbon fiber, the Lexus LFA.
Toyota also has developed a laser screw-welding process that works with steel on steel or aluminum on aluminum. The RC F is made with two laser screw-welds between each pair of spot welds.
The screw-welds are made much faster, at a half-second each. In the body shop, the robot moves along the welding row like a machine gun. Spot welds take two to three seconds each.
About the Author
You May Also Like