Toyota Will Look to Georgetown to Train Mississippi Workers
The site of Camry Hybrid production in the U.S. will be the “mother plant” for the auto maker’s newest assembly facility, which will build the Prius in 2010.
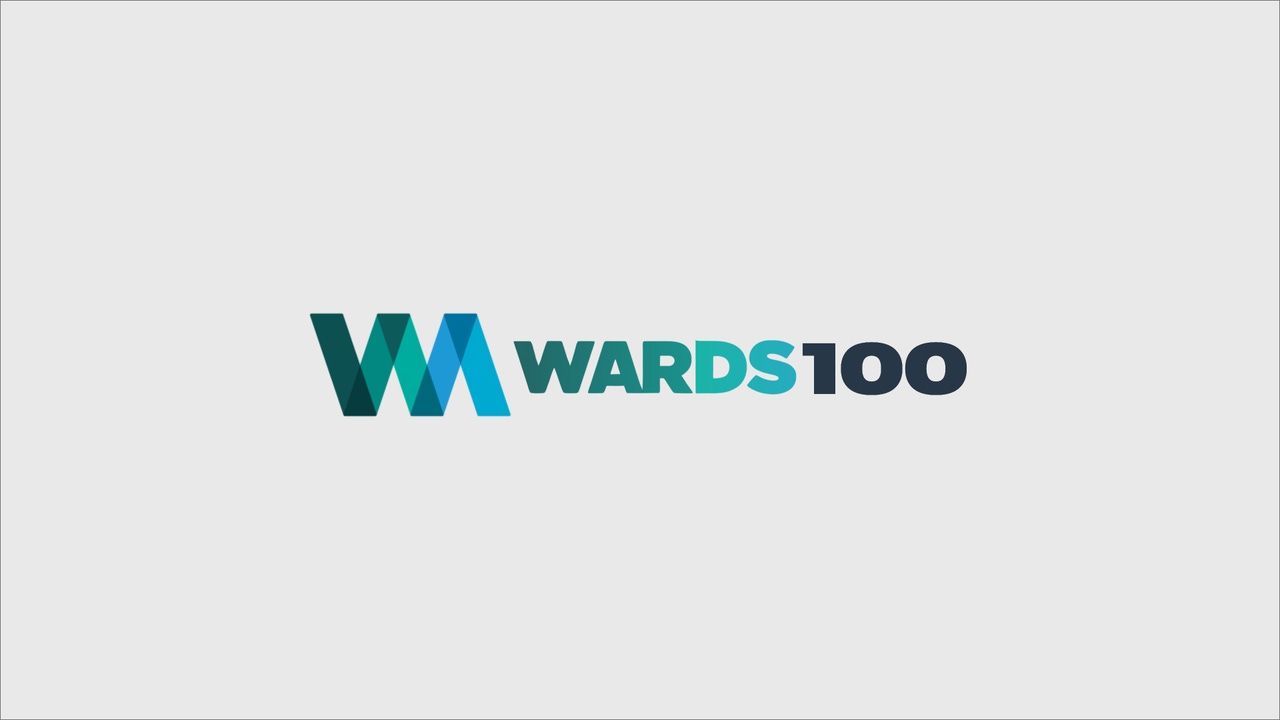
Special Coverage
Management Briefing Seminars

TRAVERSE CITY, MI – One of Toyota Motor Corp.’s top U.S. manufacturing officials expects all of the training coordination, and a fair amount of the actual training, for its future Blue Springs, MS, workforce to be handled in the U.S.
The plant near Tupelo, slated to open in 2010, will be the first Toyota plant in North America to build the Prius hybrid-electric vehicle.
Up to now, Toyota has confined the vast majority of Prius production to Japan, except for a joint-venture plant with FAW Group in China that makes units for the domestic market there.
While the auto maker’s North American manufacturing arm has made strides in recent years to become more autonomous – Toyota’s Princeton, IN, plant was the first U.S. “mother plant” for Toyota’s Tundra truck plant in San Antonio – many industry watchers have wondered if TMC would take a hands-on approach when it came to the Prius, its best-selling HEV and the car most responsible for giving it a reputation as one of the top environmentally minded auto makers in the world.
“(With Toyota Motor Mfg. Kentucky) being the mother plant, we will coordinate all (training) and make sure all the right elements are being taught and at the proper level,” Steve St. Angelo, senior vice president-Toyota Motor Engineering and Mfg. North America Inc. (TEMA), tells Ward’s in an interview at the 2008 Management Briefing Seminars here last week.
“As far as the hybrid technology, TMMK has as much experience as anyone, and we feel confident we can teach the members in Mississippi to handle it,” he says.
Blue Springs to be first Toyota plant in North America to build Prius.
St. Angelo also is president of TMMK, which has been building the HEV version of the Camry midsize sedan since 2006. It was the first Toyota HEV to be built in North America.
In keeping with a long-standing Toyota practice of genchi genbutsu, or “go-and-see,” some Mississippi employees may travel to Toyota’s Tsutsumi plant in Japan to witness the Prius being assembled there. TMMK likely will pluck the job-element sheets from Tsutsumi for workers to learn from in Mississippi, St. Angelo says.
Toyota spokesman Mike Goss says Blue Springs’ line workers will be well compensated, compared with other manufacturing workers in the region, but they will not earn a higher salary than other Toyota assembly workers in North America.
“They’ll be paid at least 150% of the average manufacturing wage in that state,” he says, noting workers in Mississippi will start out at $14 or $15 per hour, with wages rising to about $20 an hour after a certain period.
Toyota has hired some hourly workers for the Blue Springs plant already, St. Angelo says, including maintenance and skilled-trades.
However, the bulk of line workers will not be hired until spring 2010, he says, just ahead of the start of Prius output in late 2010.
In a document leaked last year to the media, Toyota stressed the need to bring the wages of its U.S. manufacturing workers in line with manufacturing-wage rates in regions where its plants are located and not have parity with what other auto makers pay their line workers.
Also in the document, which St. Angelo characterizes as TEMA “brainstorming,” was an idea to shift more health-care costs to its employees as a way for Toyota to slash North American production costs by $300 million in the next three years.
In a speech given here last week, St. Angelo said Toyota’s health-care costs have more than doubled over the past seven years.
In an effort to keep those costs down, Toyota has established a fitness center in Georgetown, KY, to help employees stay in shape, as well as an on-site pharmacy that currently fills up to 650 prescriptions each day for workers and their families.
Georgetown employees also have the option of joining the health networks, Focus Health and Gordian, whose staffs address aches and pains and answer questions about medications, St. Angelo says.
“I belong to both of them and usually once a quarter, I get a phone call: ‘OK, Steve, since our last meeting, you agreed to lose 10 lbs. (4.5 kg); you agreed to go to the gym three times a week; you agreed not to drink beer. How are you doing toward your goals?’ And I go, ‘Well, I have all this stress,’” he laughs. “But it’s just another way of controlling costs.”
Additionally, Toyota is considering in-sourcing some larger vehicle components, such as fuel-line pipes, to control costs, St. Angelo says.
About the Author
You May Also Like