Tracking Toyota's Tundra How rising stars at GM came to lead an army ofhand-picked HoosiersTracking Toyota's Tundra How rising stars at GM came to lead an army ofhand-picked Hoosiers
PRINCETON, IN - Seizo Okamoto dances around the question of which competitor Toyota Motor Manufacturing Indiana Inc. benchmarked in developing its new Tundra full-size pickup truck."It is very difficult to tell which is best," says the president and chief executive officer of Toyota's newest U.S. plant just south of this southwestern Indiana city."In size, our Tundra is smaller than Ford's F-150,
October 1, 1998
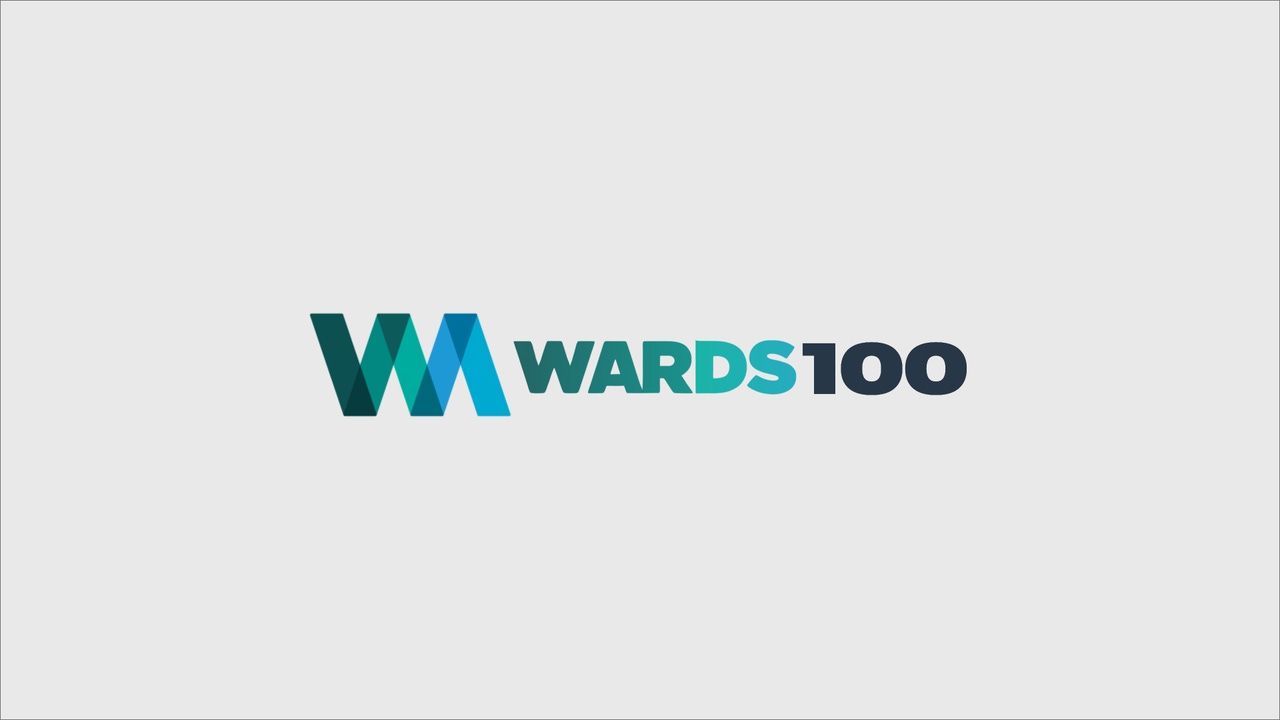
PRINCETON, IN - Seizo Okamoto dances around the question of which competitor Toyota Motor Manufacturing Indiana Inc. benchmarked in developing its new Tundra full-size pickup truck.
"It is very difficult to tell which is best," says the president and chief executive officer of Toyota's newest U.S. plant just south of this southwestern Indiana city.
"In size, our Tundra is smaller than Ford's F-150, but when you drive it, it will feel more like a car than other trucks."
Beyond this polite diplomacy there's no mistaking whom Toyota targeted when it went recruiting American management talent.
Norm Bafunno and Don Dees, general managers of production and production planning at TMMI, respectively, together logged 34 years with General Motors Corp. Most recently Mr. Bafunno was assistant plant manager at GM's Pontiac, MI, truck plant. Mr. Dees's last assignment at GM was director of paint operations for North American Operations.
Ironically, they had never met until they accepted their posts with Toyota. Today they spend at least as much time with each other as they do with their spouses.
"I wasn't looking to leave GM, but when they called, I told myself, 'Well, it's Toyota. I should at least listen,'" Mr. Bafunno says. "Then I began to think that my next assignment at GM could be overseas. Staying in the U.S. had a certain appeal. I went to school at Purdue, so Indiana didn't seem so strange. And the chance to get in on the ground floor of what Toyota is doing here was hard to resist."
What Toyota is doing here is refining its revered production system to build a full-size body-on-frame pickup truck, one that finally offers a competitive V-8 engine option, the first full-size pickup with a dual-overhead-cam design. Toyota also is trying to improve the way it selects workers, investing about $2,000 per employee in training before they build their first truck.
While many American manufacturers fret about the shortage of well-trained workers and the wages they must pay to keep them, Toyota has had the pick of the best folks southwestern Indiana has to offer, despite a jobless rate in the Evansville area of less than 3%. More than 58,000 applications were filed for the 1,300 jobs to be filled by next summer.
For production jobs, hourly wages start around $14 an hour and range up to $18. Skilled trades people are paid between $17 and $20 an hour. Benefits are comparable to what Toyota offers at its Georgetown, KY, plant. There are no on-site child-care centers or fitness centers, yet.
As with many of the Japanese and German-owned assembly plants in the U.S., most workers here have never worked in an auto plant before.
"We have people who worked in banks, breweries, taught school or have been farmers," says Tom Suter, general manager of human resources.
Through mid-September about 700 group leaders, team leaders and team members had been hired. Of those, 22% are women, 6% are minorities and the average age is 36.
By the end of 2000 there likely will be another 1,000 people hired here as Toyota adds production of a full-size sport/utility vehicle.
Each team consists of four to 10 people, including a leader. They work in a specific area of the plant, and each team member is trained to perform all the jobs for which the team is responsible.
Team leaders report to group leaders, each of whom oversees about a half-dozen teams.
The hiring process begins at a former elementary school building about five minutes from the plant. Toyota contracts with a Pittsburgh consulting firm, Development Dimensions Inc., which created the tests and evaluation process.
It begins with a series of paper and pencil tests designed to measure reading and math skills. Then applicants are asked to take part in a group exercise involving some aspect of a manufacturing process. This is followed by an intensive interview with a panel of evaluators who are looking for certain attitudinal traits and communication skills. The entire process takes about 20 hours for production candidates, slightly longer for skilled trades applicants.
Jennifer Adair is a newly hired team leader. She is 27, has a bachelor's degree in apparel merchandising from Indiana University and previously worked as an assistant manager at a Kohl's department store near Evansville.
"They definitely want to see who's going to have the stamina and persistence to get the job done," she says of her assessment.
She vividly remembers the rim-mounting exercise. For three hours she had to mount wheel rims at different points on a board.
"I had never used an impact wrench before in my life," says Ms. Adair, who will lead a team in the final inspection area of the assembly line. "But somehow I kept going. They placed a big emphasis on safety, especially in the way you lifted the rims."
Group leaders and most of the team leaders have made at least one three- or four-week trip to Japan for training at Toyota's Tahara plant. They spend about nine hours a day on the floor, learning the processes for which they will be responsible back home. Then they spend leisure hours together. The idea is to cultivate a camaraderie that they are expected to bring back to Indiana.
Mr. Bafunno says that the majority of the group leader positions will be filled by team leaders who demonstrate above-average leadership skills in their initial roles.
In contrast to Toyota's Georgetown, KY, assembly plant, where all of its first hires were trained by Japanese mentors, in Princeton, IN. the locally hired group and team leaders will train their own members.
"The people we are hiring not only have to be technically capable, they also have to teach," says Mr. Bafunno. "Are they able to prepare their team members so they feel comfortable and confident?"
Hand-picking a new work force has its advantages and liabilities.
"The biggest advantage is they are enthusiastic and looking for a challenge, " Mr. Bafunno says. "And because of our rigorous assessment process, people know what they are getting into. They come in here with no bad habits."
So what are the drawbacks?
"We have a lot of different people coming from a lot of different places and we have to get them all reading off the same page," Mr. Dees says.
The ceremonial first truck is not expected to come off the line until Dec. 10. The first salable trucks will be built in late January or early February 1999.
So there is ample time for training.
In an age of greater automation and deeper supplier involvement, Toyota's approach here almost seems like a throwback.
For example, GM has touted its body assembly process in Oshawa, Ont.; Pontiac, MI, and Fort Wayne, IN. At each location hundreds of welding robots frame the body shells of each new Chevrolet Silverado and GMC Sierra without the assistance of human hands. GM thinks it should assure quality and lower costs.
Here in Princeton, Toyota will build 100,000 trucks a year with a very lean work force of 1,300. But about 25% of the body welding will be done manually. A modest corps of 50 robots will handle the other 75%.
"When I first looked at it, I thought, 'What in the world is Toyota trying to do?'" Mr. Dees recalls. "This is the most manual body shop I've ever been involved with. But it lends itself to flexibility if all of a sudden there's a jump in demand for trucks with flareside fenders or some other new look."
Indeed, GM reduced the complexity and design of its new trucks. There still are more than 40 cab and bed configurations to satisfy its diverse base of customers, but initially there will not be a 4-door version. Tundra, meanwhile, has two body designs, a regular cab with 8-foot (2.5-m) long bed and a 4-door Access cab with a 6.5-ft. (2-m) bed.
Conventional wisdom has it that the second vehicle to be built here will be a truck-based SUV to compete with the likes of Ford Expedition, Lincoln Navigator, Chevy Tahoe and GMC Yukon. Yet those familiar with Toyota's knack for flexibility say it's not impossible that a car-based unibody vehicle such as the Lexus RX300 or its derivative could someday be built at this plant.
Mssrs. Dees and Bafunno look at their public relations colleague for guidance.
"Our second product will be built on our main body line, probably in the fall of 2000," says Mr. Bafunno. "We know markets are going to change. Are there going to be frameless vehicles out there in this segment? We don't know, but we've got to be prepared for that."
About the Author
You May Also Like