How to Shave 223 lbs.
A Consortium of Seven Auto Makers, led by Volkswagen AG, completes a 4-year project focusing on reducing the weight of a VW Golf body-in-white by 36%, bettering an original target of 30%. The Superlight-CAR project studied the design of a multi-material body as well as how a body shop could produce such a vehicle, given the different joining techniques required. The program's objective was to reduce
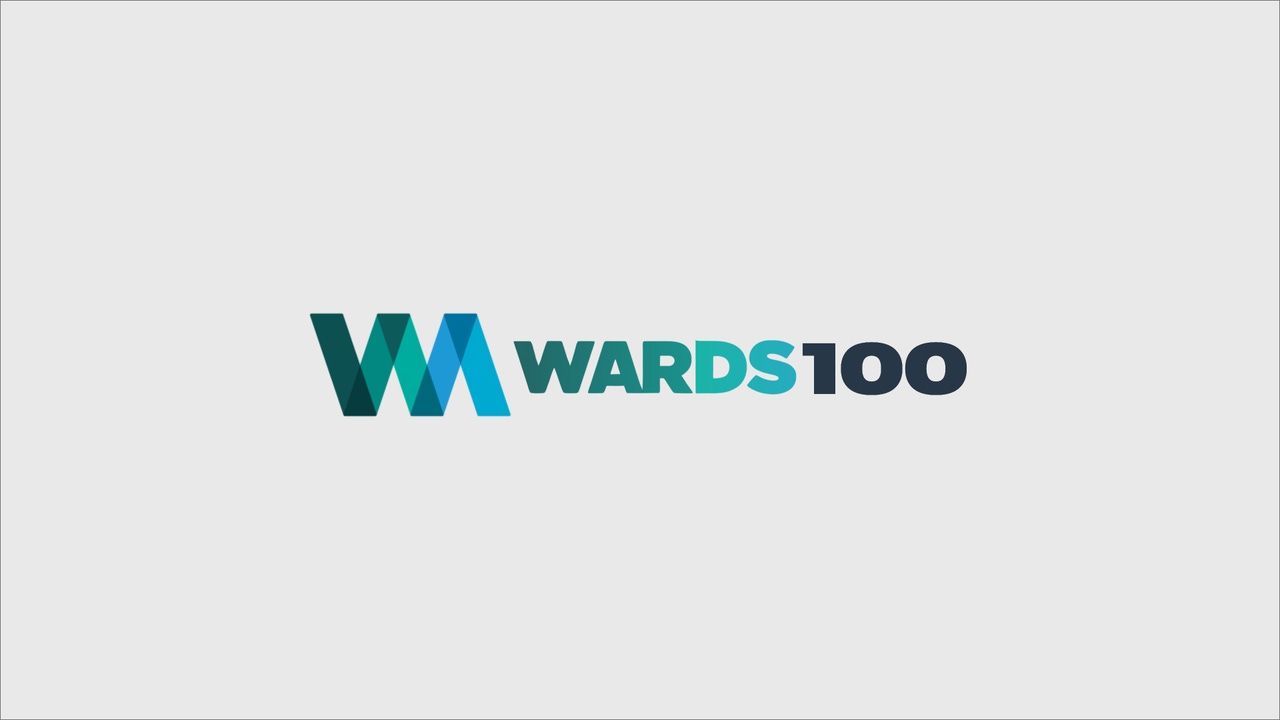
A Consortium of Seven Auto Makers, led by Volkswagen AG, completes a 4-year project focusing on reducing the weight of a VW Golf body-in-white by 36%, bettering an original target of 30%.
The Superlight-CAR project studied the design of a multi-material body as well as how a body shop could produce such a vehicle, given the different joining techniques required. The program's objective was to reduce the weight of a high-volume family vehicle without sacrificing safety, and the Golf was chosen because it is a perennial European best-seller.
Daimler AG, Fiat Auto Group, Adam Opel GmbH, Porsche AG, Renault SA and Volvo Car Corp. also participated in the €19 million ($26.5 million) project, along with 30 supplier companies and organizations. Funding of €10 million ($13.9 million) was provided by the European Union.
The completed body was revealed at a presentation by Volkswagen head of research Juergen Leohold in Wolfsburg, Germany.
The final concept weighs 397 lbs. (180 kg), 223 lbs. (101 kg) less than the original steel structure, an '05 Golf. The body is made of steel, 212 lbs. (96 kg); aluminum, 146 lbs. (66 kg); magnesium, 24 lbs. (11 kg); and plastic, 15 lbs. (7 kg). By using plastics in non-load-bearing parts, another 99 lbs. (45 kg) was eliminated.
Assuming a volume of 1,000 cars produced a day, such a body-in-white would cost €505 ($705) more to make, but the weight savings would reduce carbon-dioxide emissions by about 10 g/km, Leohold says.
With smaller engines, brakes and other elements possible due to the lighter body, the project estimates a total reduction of 20 g/km of CO2 emissions, saving 422 gallons (1,597 L) of gasoline over the 125,000-mile (201,170-km) lifetime of the vehicle.
Up to now, lightweight materials have been confined to upscale vehicles due to their higher costs, Leohold says.
The front end is the most critical part of the vehicle because it must carry the weight of the engine plus protect the passenger cabin in the event of a crash. Renault built six front-end longitudinal rails and two full front-end modules in 2008 for testing before Volkswagen assembled the final body-in-white.
“The more different materials, the more eclectic the joining technologies,” Volkswagen's Marc Stehlin said last year at a presentation of the project in Ljubljana, Slovenia.
Sub-groups of the project developed software tools needed to analyze information on recycling, cost and assembly of the multi-material approach.
The project began with three preliminary body ideas: a steel-intensive solution that eliminated 88 lbs. (40 kg) at a cost of less than €2.5/kg ($3.5/lb.), an economic multi-material approach that saved 137 lbs. (62 kg) at a cost of €5/kg ($7/lb.) and an advanced body that reduced 250 lbs. (114 kg) but cost €10/kg. ($14/lb.).
The final result incorporated ideas from the most advanced approach, but kept the additional cost of the economic model. Fiber-reinforced plastics were used for the rear floor and rear crossbeam. The roof was an experimental approach using warm-formed magnesium.
Shift to Lighter Unibody Architectures No Slam Dunk
subscribers.WardsAuto.com/ar/shift_unibody_architectures_080827/
Curbing Curb Weight
subscribers.WardsAuto.com/ar/curbing_curb_weight/
Read more about:
2009About the Author
You May Also Like