DCC Tackles Quality, Warranty Issues
In its first year in business, DaimlerChrysler Corp.'s $32 million Quality Engineering Center paid for itself, saving the company more than $54 million in repair costs alone. The 128,000-sq.-ft. (11,900-sq.-m) facility, which opened in Auburn Hills, MI in January 2000, pulls together about 150 employees from five different departments dedicated to reducing problems in finished vehicles and thus warranty
January 1, 2001
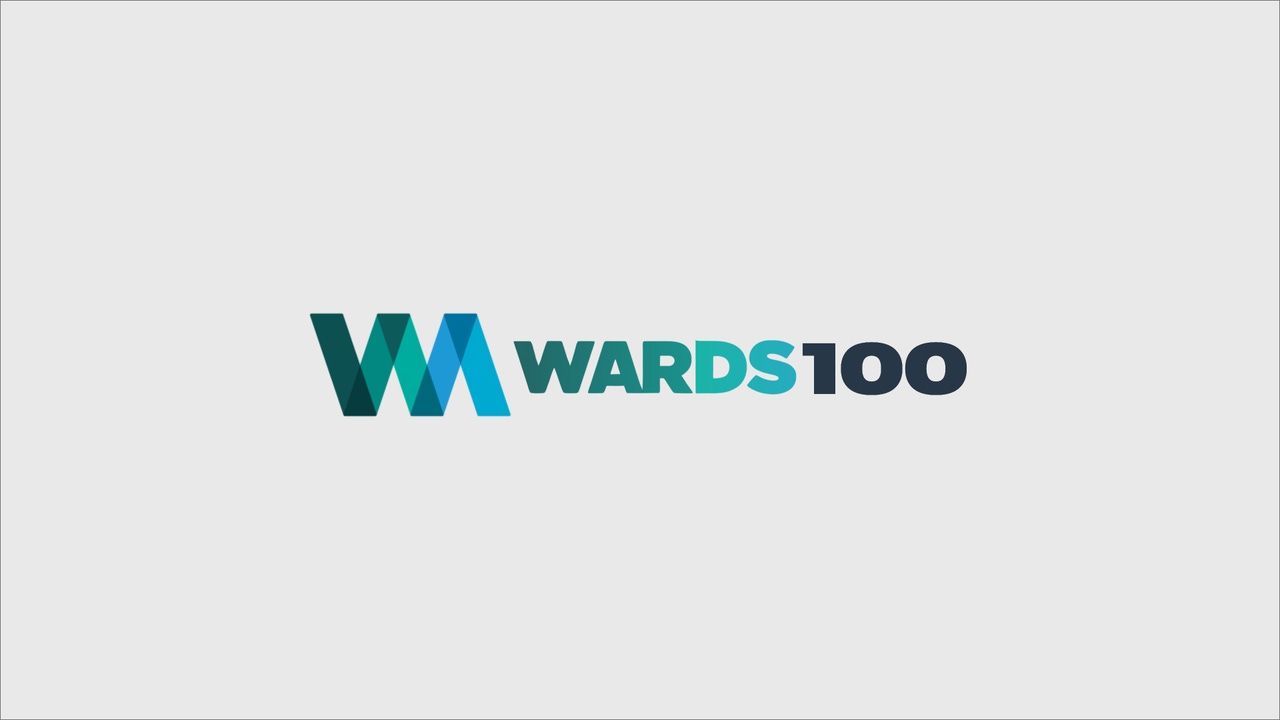
In its first year in business, DaimlerChrysler Corp.'s $32 million Quality Engineering Center paid for itself, saving the company more than $54 million in repair costs alone.
The 128,000-sq.-ft. (11,900-sq.-m) facility, which opened in Auburn Hills, MI in January 2000, pulls together about 150 employees from five different departments dedicated to reducing problems in finished vehicles and thus warranty claims. It has contributed to a 30% reduction in supplier-associated warranty problems alone.
“There is no other facility quite like this in the industry,” says J. Michael Burke, a senior manager at the leased facility a few miles from DCC's corporate technical center.
During a normal business day, 65 vehicles are evaluated and repaired while another 12 “root cause” meetings are conducted by employees and the roughly 100 supplier representatives visiting on any given day. The meetings, in small rooms for privacy, have resulted in at least 16 successful projects that were passed on to dealers.
The Parts Return Group analyzes the 600 to 700 parts that arrive daily from 160 dealerships across the country. The dealerships are selected by location, climate and volume and represent about 4% of the corporation's total volume. The defective part is sent to the quality center where it becomes an entry in the database, accessible to suppliers as well. Failure to send the part within 60 days results in the dealer being charged with the warranty claim. “That's the hook for compliance,” says Mr. Burke.
“We listen to the parts for an unbiased view of why that part came in,” says Bob Moser, director of service engineering. The part is studied to identify the problem and come up with a fix. The policy is: No part can stay more than 30 days. And the average is 16 days.
The goal is a fix at the plant level before more vehicles are built with the defect. “If we can cut one day of problem identification, we can cut out a couple thousand vehicles that won't experience the problem,” says Mr. Burke. Aftermarket fixes are passed on as well.
A team of as many as 40 engineers gathers every two weeks to review engines, including those made by Mitsubishi Motors Corp. and Cummins Engine Co. They are disassembled in an area that is a cross between a garage and an emergency room. A price tag is affixed to emphasize that a defective engine can result in a $2,500 warranty cost.
Parts also arrive that meet a list of 17 criteria, in an effort to detect repair trends. The criteria defines the population of parts by shift, color and geographic region.
“It uses a statistical base, not a person's bias about a problem,” says Mr. Moser. “We need to know trends and patterns of problems emerging.” He likens it to gill net fishing, where the size of the net determines the catch.
A Supplier Warranty Reduction Team works with suppliers to improve component performance.
The collaboration has led to programs such as a tire pilot with Goodyear in Syracuse, NY, and Atlanta. It allows Chrysler dealers to fix tire problems directly and gives the carmaker access to tire warranty information, while offering feedback to the tiremaker. It is designed to reduce customer confusion or the impression that the carmaker is foisting the problem off on the supplier. The pilot is being evaluated with an eye toward rolling it out across the country. The initial sense is that the gold-plated original can be scaled back; a tire with a problem near the end of its life cycle need not be replaced with a brand new tire.
The center also includes a research garage where employees bring their own vehicles for service. It services DC's 18,000 corporate-owned vehicles as well as pre-production or pilot vehicles, as part of their evaluation process.
This service garage is manned by engineers equipped with every known diagnostic tool and the philosophy that even a simple lube job can lead to the detection of pre-failure conditions during vehicle audit.
“We can stop the repair process at any time to delve deeper into information-gathering to find problems before they become failures,” says Mr. Moser. “We own the car, the driver, and know all of the operating details. We can cut the car into pieces if we need to, knowing we can build them a new car.”
In the Service Parts Engineering section, engineers design parts and processes that reduce the cost of repairs.
The Advance Diagnostics Research department targets “trouble not found,” warranty costs that account for 50% of complaints industry-wide. DC says it has reduced that figure after years of focussed attention.
Key to success is that, in this service department, there is no obligation to replace a part to pay for the effort. The payoff comes in cases like this: Dealers kept replacing a gas cap under warranty, while the supplier insisted the cap was sound. “The problem was that sometimes the nylon tether was getting caught and interfering with the seal,” says Mr. Moser. The problem was solved by moving the point where the tether attaches to the vehicle.
About the Author
You May Also Like