Up, Up & Away in the Bays
Auto makers' time studies try to make sure factory workers are operating efficiently in the building of vehicles. Now Rotary Lift and auto makers are working together on time studies to ensure that dealership auto technicians are working efficiently in the repair of vehicles. The intent is to cut down on warranty costs, says Matt Webster, vice president of sales and marketing at Rotary Lift, a lift
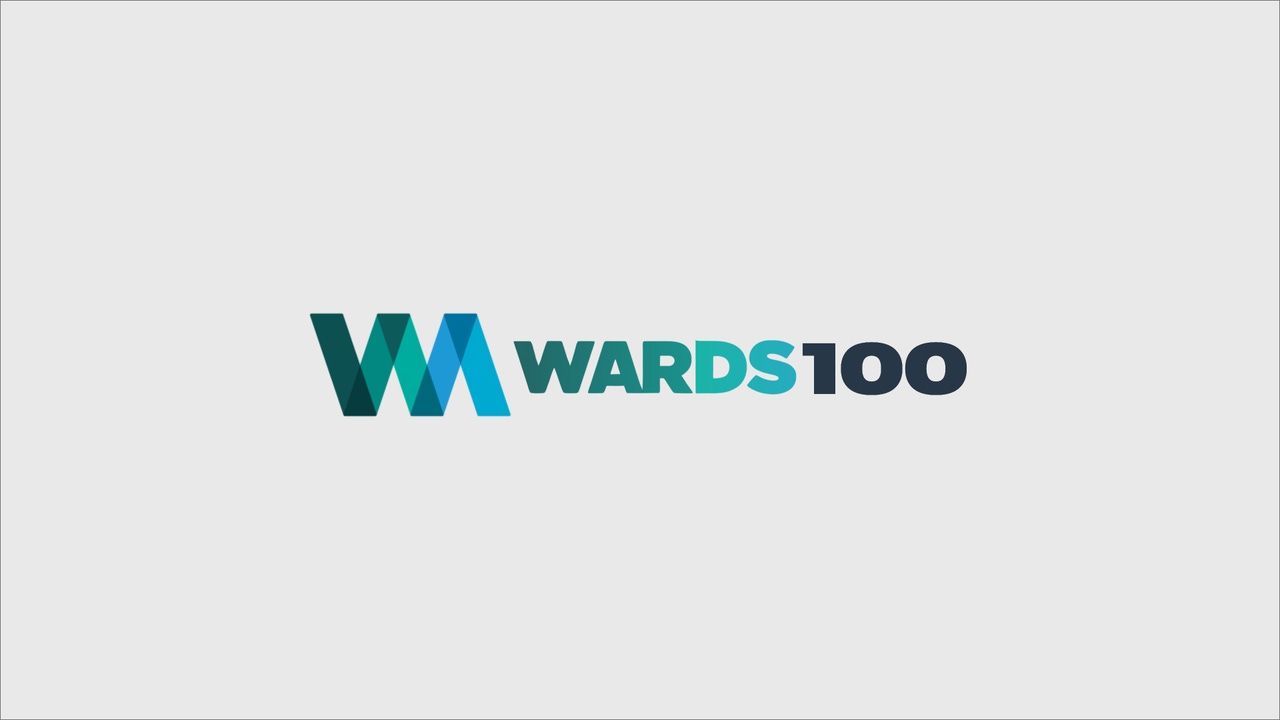
Auto makers' time studies try to make sure factory workers are operating efficiently in the building of vehicles.
Now Rotary Lift and auto makers are working together on time studies to ensure that dealership auto technicians are working efficiently in the repair of vehicles.
“The intent is to cut down on warranty costs,” says Matt Webster, vice president of sales and marketing at Rotary Lift, a lift systems manufacturer.
The firm is trying to lift sales by positioning itself as a “leader in maximizing service bay productivity.” Dubbed “techtivity,” it's become a big part of Rotary's product line design.
Features and options of late include faster lifting speeds, power units that slide away to increase work space, controls on both sides of lifts, and flip-up adapters for quicker contacts with various vehicles.
New hoists are designed to hold tools on the sides, making the lift “a work center,” says Webster. “Every task is streamlined and technicians get more done in less time.”
Rotary Lift President Eric Howlett says the Madison, IN, firm is changing as it moves “from being a lift systems manufacturer to a company centered on delivering productivity solutions.”
Modern lifts are also designed to take up less space, offering more work room for mechanics. Such equipment also eats up less floor space, a consideration in markets where property costs are at a premium.
Read more about:
2004About the Author
You May Also Like